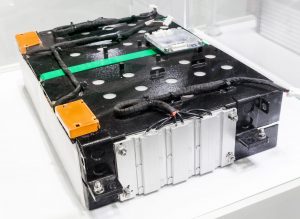
Electric vehicles (EVs) are essential for lowering emissions in modern cities. The performance goals for zero-emission, lithium Ion battery-based EVs include improved capacity, faster charging with more refresh cycles and similar or (better still) reduced cost for current vehicle fleets. In addition, the total operating cost, range and safety of EVs are critical considerations.
The industry recognizes that the current generation of Lithium-ion (Li-ion) batteries degrades too quickly, resulting in significant range loss over time for EVs—and increasing the risk of catastrophic failure for batteries. Current EV batteries are one of the few systems where fuel and oxidant are stored in the same place…much like rockets and explosives. Designing materials that don’t explode will always be top of mind for EV builders and battery developers alike.
To address these challenges, manufacturers leverage modeling and simulation on individual scales to understand the design trade-offs inherent in batteries, especially the chemistry at the electrode surface, the stability of the electrolyte interface layer and how these properties relate to battery performance. Unfortunately, different departments in R&D organizations often do not talk to each other, especially those working on different scales of the same problem. They do not truly collaborate but instead are locked in organizational silos that can disrupt R&D success.
Dassault Systèmes has taken the lead in promoting a more collaborative work environment by developing an integrated multi-scale modeling approach to the computational exploration of chemical space for battery electrolytes.
Expanding the Chemical Space for Electrolytes
An open-access, scientific paper entitled “Multi-scale Electrolyte Transport Simulations for Lithium Ion Batteries” published in November 2019 in the Journal of The Electrochemical Society takes a first step toward addressing these challenges with the aid of simulations that do not require the time-consuming and costly redesign of materials. The paper focuses on Li-ion electrolytes, the most flammable part of the battery, which is typically optimized relatively late in the engineering process after other major battery design decisions have been set in stone. For this reason, changes in the electrolyte formulation can be implemented on engineering time scales that are typically much shorter than the lead times involved in novel materials discovery.
The paper describes a fully automated workflow for a given electrolyte composition, salt concentration and temperature—a workflow that creates a link between multiscale, atomistic simulations and battery cell performance. In this cross-scale approach, approximately 200 solvent molecules and an appropriate number of ions for each salt concentration were packed randomly into a simulation box using the Amorphous Cell module in BIOVIA Materials Studio software. The electrolyte structure and ion dynamics were then obtained using molecular dynamics simulations.
The workflow allows scientists to model the ion flow through the electrolyte and thus characterize its charge transport properties by tracking the motion of ions throughout the simulations. This provides the opportunity to computationally explore the physicochemical factors impacting electrolyte performance, e.g., establishing the effect of individual additives on macroscopic cell performance. The authors describe how fully predictive models can optimize any combination of solvents, salts and additives for any purpose and directly calculate the final cell performance for formulations.
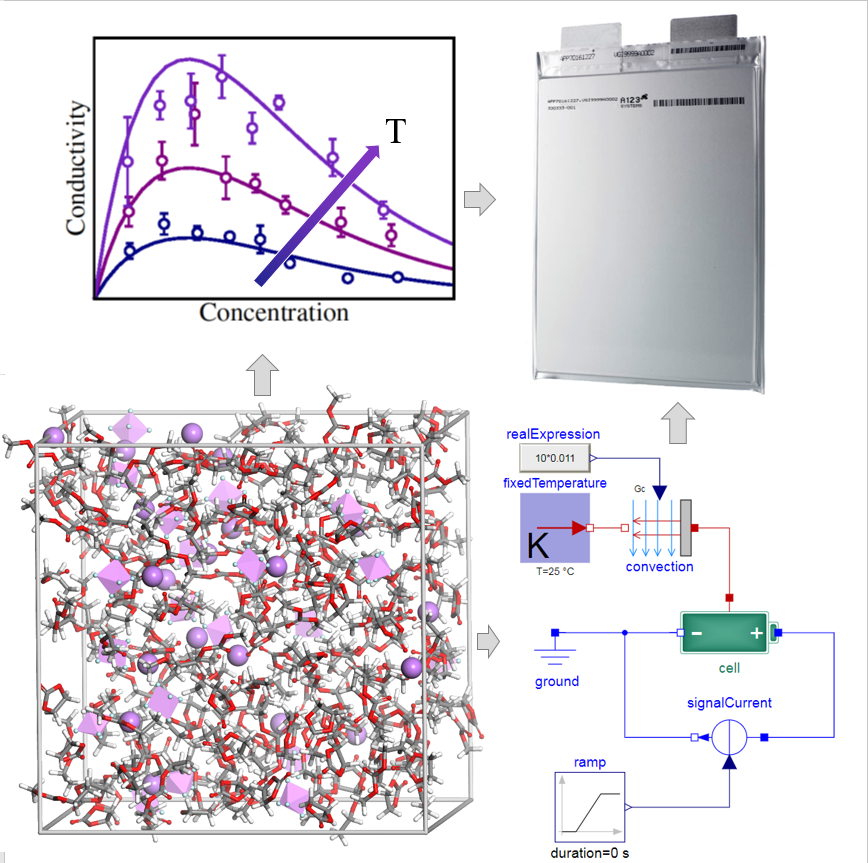
A Valuable Collaboration between Industry and Academia
BIOVIA Dassault Systèmes has played a significant role in this important scientific paper. The lead author, Dr. Felix Hanke, is a Fellow on the BIOVIA Science Council, which is responsible for advancing the highest levels of scientific research and innovation across the industries served by BIOVIA. Dr. Hanke emphasizes the valuable social and collaborative efforts required to establish this direct computational link between electrolyte chemistry and battery cell performance.
“It’s a true multi-scale model,” says Hanke. “To build it, we needed to integrate atomistic simulation from BIOVIA and continuum modelling from CATIA, another Dassault Systèmes brand. This combination allowed us to link the molecular composition of the electrolyte to the final performance of the battery cell. The project also involved collaboration with the Faraday Institution, the UK’s leading battery research center. A mathematician from Faraday helped with model validation. Finally, we also teamed up with the UK’s Centre for Doctoral Training (CDT) in Computational Methods for Materials Science. Dassault Systèmes is the industrial partner of this organization with BIOVIA providing access to Materials Studio software for teaching and research. Every year BIOVIA hosts a group of CDT students for a week to work on projects of our choosing, and the idea for this paper began during one of these visits. The paper’s authors include three students from the University of Cambridge, two from the Department of Chemistry and one from the Department of Engineering.”
This important, open-access paper—a collaborative contribution by Dassault Systèmes, industry and academia—has established a seamless, multi-scale link between the molecular composition of liquid electrolytes in commercially-available batteries and their electrochemical performance. An entirely in silico approach to electrolyte formulations can be a successful strategy for efficiently and cost-effectively identifying suitable additive battery components going forward.