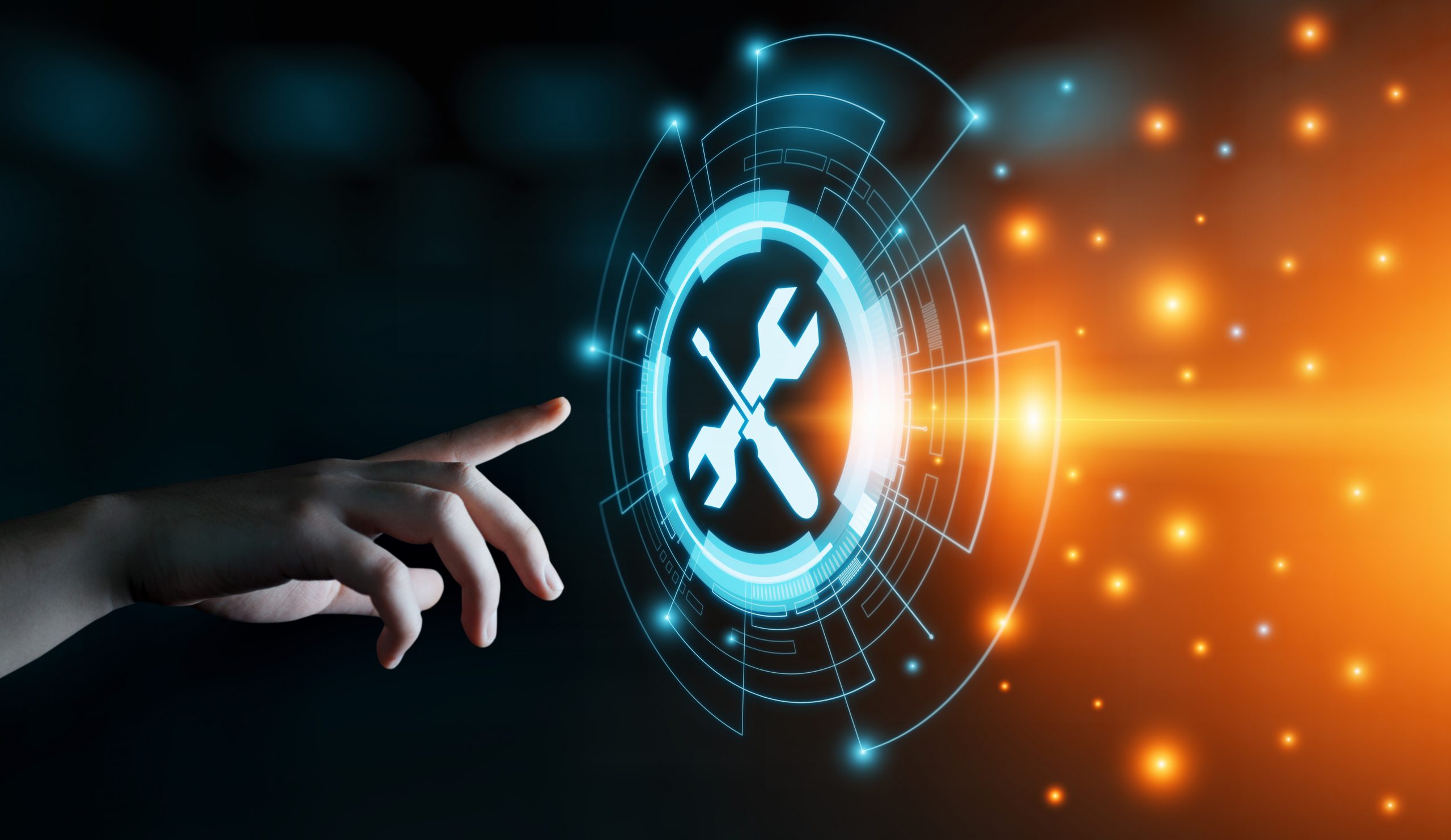
Regular equipment maintenance is important and necessary to ensure the proper performance and working condition of manufacturing equipment. If not done in time, you risk unexpected equipment breakdown, reduced overall lifetime, increased maintenance costs, wasted energy and further disruption. Although preventive maintenance can minimize these risks, it can also lead to over maintenance with unnecessary costs, equipment downtime and reduced output.
Predictive Maintenance
Predictive maintenance helps determine the condition of the equipment to estimate when maintenance will be necessary. It allows convenient scheduling of corrective maintenance when needed and can prevent unexpected equipment failures. By turning unplanned stops into shorter and fewer planned stops, you can increase equipment availability and lifetime, improve safety and environmental impact and optimize spare parts handling. It is also an Industry 4.0 initiative.
Rule-based predictive maintenance requires continuous data collection by sensors; hence, another name for this is condition monitoring. Predefined rules and predefined thresholds generate alerts. Machine learning-based predictive maintenance relies on large sets of historical failure data used with machine-learning algorithms to run different scenarios and estimate the probability of things going wrong, and when. This data- and model-driven approach provides insights for maintenance and repairs allowing organizations to avoid unscheduled disruptions in operations or production.
Laboratories with their large number of costly and sensitive testing instruments are one application area where predictive maintenance can make a difference. It can help in the production of pharmaceuticals, household or cosmetic products. It can also help process industries in the production of chemicals as well as discrete manufacturing industries like automotive, aerospace or industrial equipment. In all these industries, delays in time to market can result in significant losses in revenue or market share.
How does it help?
Machine learning-based predictive maintenance utilizes a large amount of historical data collected from a substantial number of instruments (about 100) that are equipped with sensors connected to an IoT (Internet of Things) platform. These sensors measure and deliver data related to voltage, temperature, pressure, rotation and vibration for a full year. The data might be streaming data that requires real-time processing, averaging or sampling on the fly. This “telemetry” data contains time stamps (e.g., 2018-03-26T20:36:02.316Z) and includes contextual data on machine age and type. Hereby the system excludes “error” and/or “on-breaking” signals sent out by the machines at particular times.
Additional data collected includes any maintenance records of scheduled and unscheduled visits, which are related to machine parts or components that needed to be replaced either due to failure or because they were suspect.
Machine Learning can help to compute the time to failure, time since fault (error) and maintenance events. Effective machine learning-based predictive maintenance may require lagged or averaged features, as the future state of the system depends on both historical data and current data. The algorithms are trained using historical failure, maintenance and events data and configured to estimate the probability of failure over different operating horizons (e.g., 14 days, 30 days or 6 months). The system then transforms the data on 3h and 24h sliding windows with the data from different sources combined on a timestamp (Multi-category Bayesian Model).
BIOVIA Pipeline Pilot, Dassault Systèmes’ solution for advanced machine learning, supports Predictive Maintenance. Pipeline Pilot users get direct access to methods development and extensions, while Workbenches guide them through a best practice workflow to build the models required for Predictive Maintenance. Organizations can then publish these models so that they can be consumed within the user workflows for predicting failures, equipment lifetime and optimal maintenance schedules.
Pipeline Pilot also supports automated model learning allowing updates by automatically rebuilding models as new data comes in. This keeps model predictions relevant when production parameters change or new equipment comes on line.
The Value
By using BIOVIA Pipeline Pilot for Predictive Maintenance, organizations can optimize maintenance expenditure by operationalizing identified maintenance needs and prioritizing and initiating maintenance where required based on the predictions. They can optimally schedule maintenance within the equipment operating cycle.
Pipeline Pilot also helps to reduce operational costs by minimizing equipment downtime, by supporting early identification and repair of equipment at high risk of failure and by driving asset replacement decisions for equipment at high risk. It also helps to reduce repair costs by eliminating unneeded replacements and extending the asset life based on data-driven, root cause analysis of failures. These capabilities can also help to improve product quality in upcoming product versions.
With Pipeline Pilot, manufacturers can shift reactive maintenance to predictive maintenance. This can increase uptime, optimize maintenance and lower repair costs. As a result, organizations can deliver better predictability to their customers, optimize product prices and be more competitive.