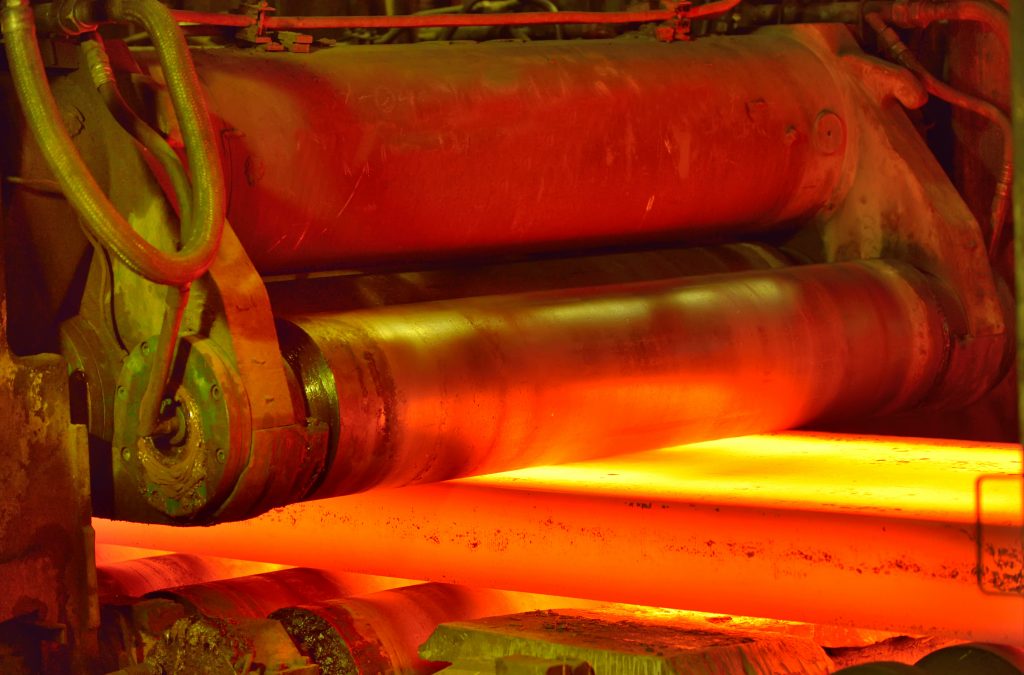
From controlling operating costs to maximizing profits, steel manufacturers must juggle a number of conflicting priorities. On top of this, optimal performance must be maintained, and this extends to the scheduling of hot and cold steel rolling.
However, it is often challenging to strike the right balance for performance and drive efficiency when considering the various complex rules and constraints around hot and cold mill scheduling. This entails both the process as well as the use of resources—in this case, getting the most value and use out of typically costly equipment like steel mills. In addition, steel mills are capital intensive and result in a bottleneck process, and in each process, there are different exceptions and disruptions. So, it is usually insufficient to create a single schedule and instead, frequent rescheduling is required depending on the situation.
Hot and Cold Steel Mill Scheduling
Hot and cold mill scheduling is all about being able to precisely determine:
- Which orders to produce in the coming days
- How to produce those orders by creating programs and defining program blocks
- When to produce them by sequencing mills according to all relevant rules
Accurately planning steel hot/cold mill schedule slots based on available resources and pending orders is a tough task, even for the most experienced planner. Each schedule must take into consideration which slabs can be slotted in to extend the schedule and minimize the waiting time between casting and hot/cold rolling. Should a disruption occur—for example, when the temperature of steel fails to reach its target composition and needs to be recast—processes have to be rapidly rescheduled to ensure that orders are not delayed.
Key Improvement Opportunities
This process requires detailed scheduling days or even mere hours ahead, for which real-time material and scheduling visibility is needed. Having a solution that provides these key capabilities can unlock your organization’s potential to make these improvements:
- Improve profitability by increasing resource utilization and throughput while lowering the cost of running machines.
- Improve production reliability by increasing quality with allowed transitions and minimizing unexpected breakdowns.
- Ensure visibility and control using a single source of truth to steer production, achieve end-to-end visibility and visualize impacts on business goals and KPIs.
- Maintain and grow customer base by increasing service and OTIF delivery performance as well as reducing lead times.
- Reduce energy consumption with hot charging.
DELMIA Quintiq for Hot and Cold Mill Scheduling
The DELMIA Quintiq solution for hot and cold steel mill scheduling enables manufacturers to capitalize on key improvement opportunities. Powered by world-record-breaking optimization technology, our advanced scheduling system optimizes programs and sequences within programs to ensure efficient and reliable performance every time—from material flows to rolling programs to sequencing. It captures and optimizes all rules and constraints unique to your business as well as that of your particular mill and allows you to define sequencing and setup rules and parameters. Many of our customers are now realizing the benefits of our solution, including:
- Increased on-time delivery by 15-30%
- Reduced costs by 5-20%
- Increased productivity by 3-5%
- Improved quality by 5-10%
To learn more about how the DELMIA Quintiq solution can help you optimize hot and cold mill scheduling to achieve planning accuracy, efficient production and reliable performance for your steel manufacturing, download our brochure now.
For more information about cold mill scheduling specifically, watch our on-demand webinar here.