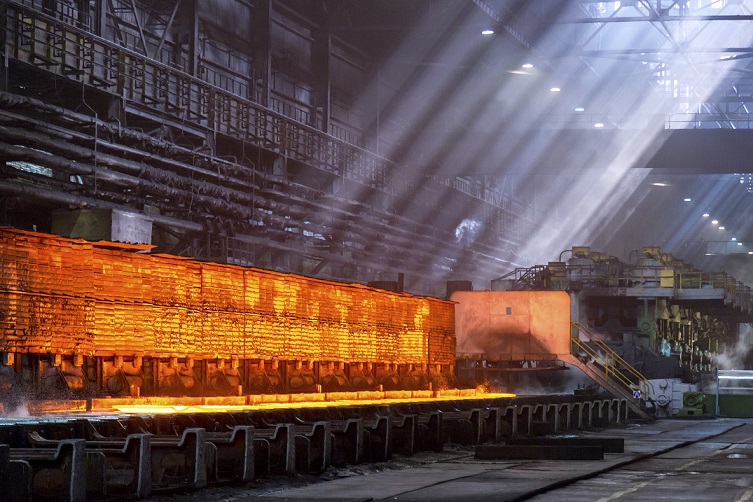
The outlook for the steel industry in 2015 remains cautious.
Overcapacity, particularly from China, is still an issue even though global demand has risen marginally in the past year. Steel prices are down, and companies are consolidating or going bust.
In this highly volatile market, it’s key that steel manufacturers focus on improving cost effectiveness and operational efficiency. Many are turning to new technologies, better data analytics, to realize these gains and resist competitive pressures.
But no matter the solution, good planning fundamentals never change.
Plan and schedule around your KPIs
As your business grows and evolves, it’s crucial that your plans grow with it. Problem is, when plans and schedules are refined over time, they tend to veer off course.
Your planners need to be able to see the consequences of every decision, so that the best choices can be made. Simply put: To remain true to your KPIs, you cannot lose sight of them.
ABS, Italy’s top specialty steel producer faced similar challenges. The company was having trouble optimizing its resources and handling complex manufacturing processes.
For example, ABS’s production simulations were done using spreadsheets, and planners had to make many manual readjustments. KPIs were not used in planning and scheduling, and adjustments were made independent of business goals.
[Tweet “To remain true to your KPIs, you cannot lose sight of them.”]We worked with ABS with their KPIs in mind, and deployed a solution in just 18 months. It helped ABS meet its primary production goal of 100% delivery of all products on time and in full (OTIF). The DELMIA Quintiq solution was also integrated seamlessly with their existing SAP ERP platform, which kept the impact of implementation to a minimum.
Key takeaway: Swift, interactive KPI-based scheduling and re-scheduling is the key to achieving complete business control and responding effectively to a dynamic environment.
Execute according to your unique rules and constraints
Does this sound familiar to you? The planning department creates a schedule, only to have it modified by the night shift leader later because the schedule ignores production rules and uses inaccurate estimates of production times.
FNsteel, a major European steel producer, was planning based on the orders it was receiving, instead of the capacity it had on the floor. This led to the accumulation of temporary stock, because wires that needed additional treatment remained idle until another order was finished.
When we worked on the FNsteel solution, we made sure to incorporate its shop floor knowledge into the system to create optimal plans for all processes. The results are staggering:
- Increased productivity from 85% to over 93%
- Reduced production cycles by 10%
- Decreased temporary stock by almost 50%
Key takeaway: Your plans are only as good as the execution. Are your planners incorporating shop floor knowledge in their plans?
[Tweet “Your plans are only as good as the execution. Equip your planners with the best tools.”]To sum up, when looking at supply chain transformation initiatives, getting the basics right can make a big difference. Make sure they’re firmly grounded in the things that matter most: Your goals and capacity to execute.
For more on supply chain transformations, discover the seven DELMIA Quintiq advantages top steel manufacturers are enjoying today.