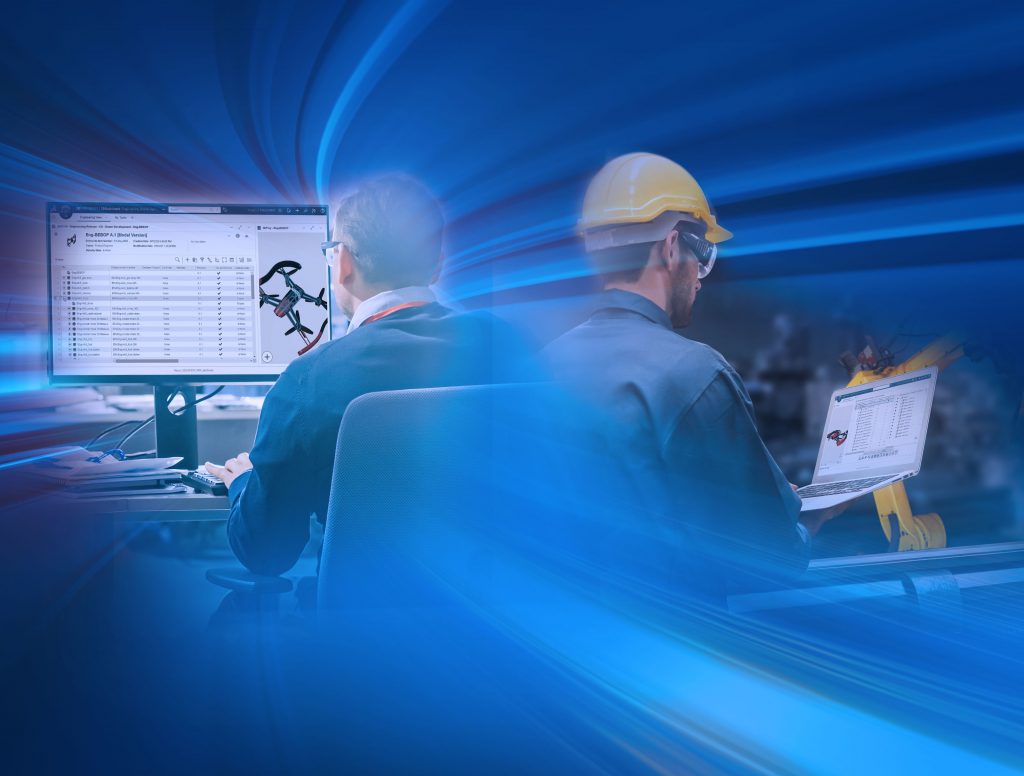
In a continued effort to capture customer demand from competitors, the need to bring products to market faster and with high quality is increasing. This is a hard enough challenge, let alone considering reducing costs to drive more sustainable business. With increasing product complexity (especially with high technology components), every aspect of the manufacturing process needs to be streamlined.
The product development process is an area of opportunity that can address these challenges. The product engineering and manufacturing engineering roles often work from disconnected data and processes. This inhibits the efficiency of production operations and can lead to unseen costly and time-consuming errors in manufacturing.
A critical aspect of this process is the fact that each role has a different view of the product definition – the Engineering and Manufacturing Bill of Materials (EBOM and MBOM). While both are important, they are typically individually optimized and maintained separately. This digital “gap” in the continuity of operations needs to be unified to eliminate the functional silos and validate and optimize product designs as an integrated whole.
The 3DEXPERIENCE platform provides a better way by offering a virtual product definition for multi-discipline collaboration. It offers an accurate, up-to-date representation of the product throughout the engineering to manufacturing process. The BOM does not disappear in this context; the virtual product model simply becomes the master definition from which all stakeholders can now see their own view (MBOM or EBOM).
This means all stakeholders now see product updates and collaborate in real time to:
- Define and review manufacturing intent of items
- Identify potential manufacturing issues virtually
- Explore alternate design and manufacturing strategies
- Ultimately validate design updates and changes with confidence
Connecting engineering and manufacturing in this way provides significant benefits to product operations. The increased efficiency and agility speed time to market while increasing the quality of the final product and reducing the cost of operations.
In industry, we can see compelling examples that show the value:
- 30% Cut in post-production engineering errors
- 50% Reduction in design errors
- 25% Reduction in product quality problems
- 50% Reduction in engineering change management
By moving from a BOM-centric process to a virtual product definition, product development becomes more efficient and less error prone. Time to market accelerates with faster exchange of information between Engineering and Manufacturing. A common product definition and an enterprise-wide change process eliminates the friction associated with multiple BOMs.
To learn more, please download our new eBook here.