This is the first of a 2-part series addressing the impact of adopting collaborative robots in the SME manufacturing environment.
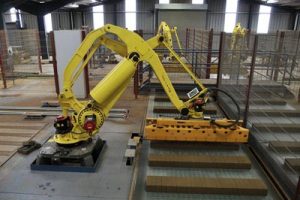
Although there is a lot of hype about robots taking jobs away from humans, the truth is today many industries still rely on human processes. According to the Boston Consulting Group, only 10% of tasks were performed by robots in 2015 across all manufacturing industries[1]. However, they expect this share of tasks to increase to 25% by 2025.
How will this happen? This will have to come from the largest sector of the manufacturing base: the small and midsized enterprises (SMEs)[2]. And, the enabler will be so-called collaborative robots, which fit the needs of SMEs much better than traditional industrial robots. The market for such robots is expected to grow at a Compound Annual Growth rate of 60% over the 2017-2021 period[3], exceeding 1$ billion by 2020 with 40,000 units sold[4].
What are collaborative robots?
As their name indicates, collaborative robots, also called cobots, allow workers to work side-by-side with them, as opposed to traditional robots which must be located in a secured, closed area for safety reasons.
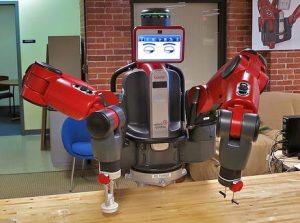
Manufacturers of cobots include:
Pioneers such as Universal Robots, a leader in the cobots market, and Rethink Robotics whose innovative Baxter and Sawyer cobots have received a lot of attention.
Established industrial robot makers thathave recently introduced cobots to their catalog. From the big four of Industrial Robots, we have the LBR iiwa from KUKA, the dual-arm YuMi robot from ABB, the HC10 from Yaskama Motoman and the CR-35iA from FANUC (which is based on the existing M20iA/35M robot with added rubber skin and force sensors).
Cobots eliminate the need for costly fences, do not use valuable shop floor space nor reduce access to equipment.
But this alone would not be enough for adoption by SMEs.
Why are cobots a good fit for automation in SMEs?
Human safety
For SMEs that want to embrace automation, worker safety is a major concern.
Power and force-limited cobots are equipped with force sensors that make the robot stop whenever they encounter an obstacle, so that a human feels nothing more than a gentle nudge. Such cobots often carry a low payload[5] and work at a slow speed. They also often have round corners and a soft surface and are even shaped to avoid pinch points[6].
In faster and heavier applications, the cobot can use its sensors to slow down as people approach and ultimately stop when someone enters a defined perimeter.
In any case, a risk assessment of the whole robotic cell is needed. For example, a cobot with a sharp part at the end of its arm may pose a risk, even though it is designed to be “safe”. The recently-released (Feb. 2016) ISO/TS 15066 specification provides long-awaited safety guidelines for collaborative robots. This publication is expected to foster a wide adoption of cobots.
Ease of deployment
Industrial robots are robust and efficient but often require skilled robotic programmers, which are usually not available in SMEs.
On the other hand, cobots are usually trained by demonstration. An operator gets hold of a cobot’s arm and trains it by following the desired path of movement and executing the desired end-of-arm tool commands (such as grip or release) – see this demonstration with the LBR iiwa cobot from KUKA. A tablet may allow operators to fine tune the operation settings.
In addition, cobots come with out-of-the-box or optional devices which make them ready for use (e.g. hand cameras for object recognition, adaptive grippers or suction cups, etc.).
As a result, implementation time is significantly reduced. For example, Paradigm, a manufacturer of high performance loud speakers, needed to increase their production throughput. In one month only, they deployed a cobot that performed the first phase of polishing speakers. A previous implementation have taken five months with a cartesian type robot.
Flexibility
We are entering the era of mass-personalization, with high mix and low volume production. This is especially true for SMEs and cobots can help with this challenge:
- They are lightweight devices. With no fencing required, they freely around the factory floor to the area where they are most needed.
- They are easy to reprogram (see above) and can therefore quickly help workers on a new task to meet a changing demand.
Affordability
According to a Barclays Equity Research report, the average selling price for cobots in 2015 is $28,177 per unit, with prices expected to decline 3-5% per year through to 2025.
This is much cheaper than industrial robots, whose prices range from $50,000 to $80,000 per unit according to RobotWorx, an integrator of industrial robots.
This allows a lot of SMEs to consider the usage of robots, which until now was believed to be unaffordable[7].
Summary
In this article we have seen that collaborative robots (cobots) are robots that can work hand-in-hand with workers in a shared workspace. Their ease of deployment, flexibility and affordability make them a good fit for SMEs.
Part 2 of this article will list some key applications of cobots, with examples from different industries. We will also discuss the expected impact of a wide adoption of cobots – for companies, for workers, for MOM systems[8] and for the society as a whole.
[1] It is also worth noting that 38% of the worldwide investments in industrial robots still came from the automotive industry alone (source: Work Robotics Industrial Robots report, 2016 – IFR Statistical Department)
[2] “Dramatic growth will come from the 90 percent of the market for robotics that isn’t yet automated. These are the small and midsized enterprises across the globe.” (The Business of Automation, Betting on Robots)
[3] According to a Research and Markets report.
[4]Source: ABI research
[5] Payload = carrying capacity
[6] See for example the convoluted shape of the KUKA LBR iiwa cobot.
[7] In case you wonder how cobots with advanced force-limited capabilities can be cheaper than industrial robots, the reasons are: a) Cobots are designed to have smaller payloads and are lighter, which reduces cost and b) Cobots have a lower accuracy and repeatability than industrial robots, which is acceptable since collaborative applications are usually less demanding. Cobots also have taken advantage of the decrease of sensor prices. For more information, see Why Are Collaborative Robots So Cheap?
[8] Manufacturing Operations Management systems