Industrial buyers want equipment customized to meet their specific operational needs and requirements, but still demand competitive pricing. Modular product architectures are making it faster and more efficient to customize standard products for the mass market while avoiding the complexity and high costs traditionally associated with engineered-to-order processes.
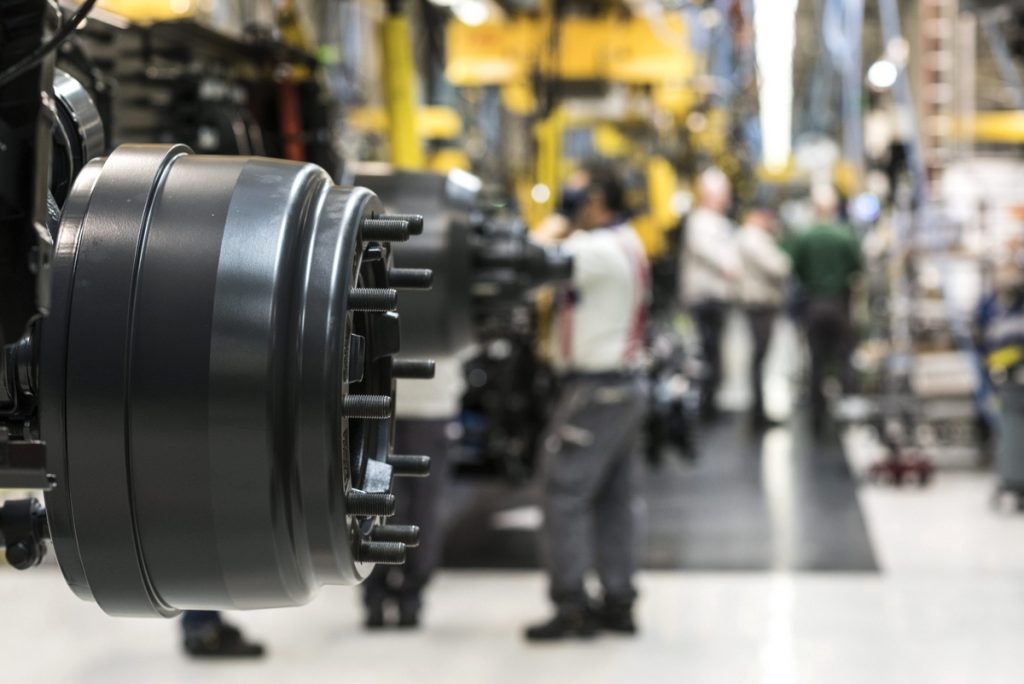
Minnesota-based mechanical test equipment manufacturer MTS Systems Corporation once required 11,000 unique part numbers to build 150 product variations of its servohydraulic load frames. Now, it uses just 800 unique part numbers – 90% fewer – to build more than 100,000 product variants.
In Helsinki, Wärtsilä used to spend 10 years developing a single new medium-speed engine for its marine customers. Since reducing the number of unique parts from nearly 7,000 to fewer than 4,000, it has developed a series of engines that can be adapted for different fuels depending on customer requirements – in half the time at half the cost.
MTS Systems and Wärtsilä are among a growing number of industrial equipment (IE) manufacturers that have mastered the art of fulfilling diverse customer requests for customized products without increasing costs and production time, or decreasing quality. Their secret? Modularization.
MINIMAL PARTS, MULTIPLE VARIANTS
Pioneered by truck and bus manufacturer Scania in Södertälje, Sweden, in the 1960s, modularization breaks complex products into a collection of standardized components that can be mixed and matched to quickly create a wide range of products without the usual costs of customization.
“Whole product families can be formed based on the same limited number of modules, and the internal complexity can be kept to a viable level,” said Jana Golfmann, senior consultant of Ernst & Young’s Advisory Practice. “Modularization is the most efficient way for IE manufacturers to develop varied product line assemblies and achieve mass customization with economies of scale.”
Modularization comes with a long list of benefits.
“Modularization can cut part numbers by 50%-60%, thereby reducing the cost of materials by 10%-15% and decreasing assembly and manufacturing times by at least 25%-35% – and that’s before manufacturers have even looked at the product itself,” said Sam Burman, managing director for SPJ Consulting, which helps companies develop modularization concepts.
“One truck company I worked at reduced its part numbers from 45,000 to 15,000 but created billions of product variant possibilities for one customer. Ultimately, fewer parts and less manufacturing time increases revenue.”
China-based Chongqing Yinhe Experimental Equipment Company (CQYH), which builds environmental testing machinery for the military, aerospace and automotive sectors, provides more proof for the power of modularization. CQYH inputs customer requirements directly into its modular architecture solution, allowing customers to quickly approve 3D models and eliminate physical prototypes.
“With our modular architecture solution, we accelerated order fulfillment and reduced design errors by 50%,” CQYH CEO Zhixian Zhang said. “Moreover, our R&D activities have become better organized and, although the number of newly developed parts is falling, the number of orders keeps going up. We’ve increased our turnover from RMB40 million (US$58 million) to RMB150 million-180 million (US$218 million-$261 million).”