Despite being highly automated in many of their operations, most life sciences companies have not embraced smart manufacturing. Bridging this gap, experts say, will help life sciences companies control costs and be more responsive to patient needs.
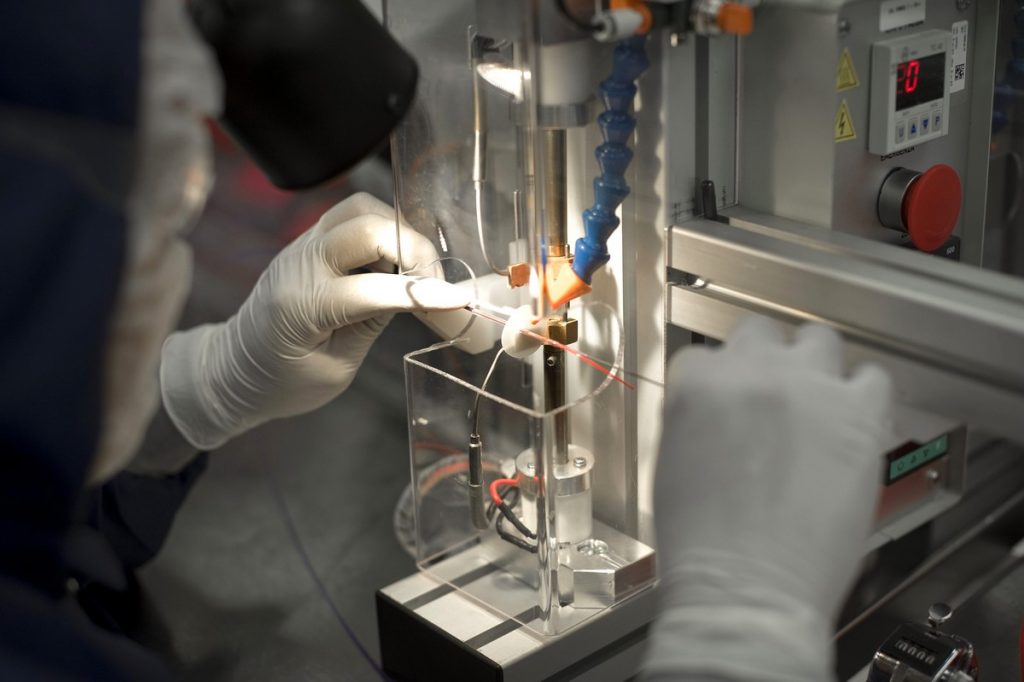
With health care payers such as insurance companies and national health systems carefully screening what costs they reimburse, and new therapies serving ever-smaller patient populations, pharmaceutical, biotech, and medical device manufacturers are looking toward the data generated by their processes for clues to capturing efficiencies.
“Most life sciences organizations are already collecting loads of data from automated manufacturing systems,” said Daniel R. Matlis, president of Axendia, a life sciences analyst and strategic advisory firm based in greater Philadelphia, with offices worldwide. “But collecting data is not enough; the value lies in extracting and distilling the data into information and knowledge to support smarter decisions.”
Benefits can include higher product quality, reductions in defects, as well as enhanced operational effectiveness and improved yields, Matlis said. “Gleaning intelligence from data can ultimately drive the shift from reactive to predictive approaches to product quality, which in turn improves patient outcomes.”
Smart manufacturing, Matlis said, requires automation in routine production and quality operations to generate data, plus ongoing analytics that support rapid and intelligent decision making. In life sciences businesses, much of the data for smart analytics comes from networks of manufacturing devices enabled for the Internet of Things (IoT).
PROCEEDING WITH CAUTION
”IoT is an enabler to improve product quality and increase production system throughput,” said Dennis Brandl, founder of BR&L Consulting, a Cary, North Carolina, firm that specializes in manufacturing IT, operations technology and industrial automation.
However, the life sciences industry has been cautious in adopting digital technologies, in part due to fears about changing a validated process that regulators have approved.
“When a bio-pharmaceutical product is submitted to regulators for approval, the chemistry and manufacturing controls are locked down,” Matlis said. “Changes that materially alter the manufacturing process must then be resubmitted for approval by regulators. As a result, companies often avoid making changes to manufacturing processes during the exclusivity period out of fear that the regulator might come back and push back on how they are doing it now.”
And yet, many aspects of digital measurement do not change the validated process itself.
“Putting sensors on a machine to monitor operations and time in operation is not really changing the machine or the validated production process per se, ” said Marcus Ehrhardt, a New York City-based principal at global consulting firm PwC’s Strategy&. “Given this fact, companies can take many steps toward operations digitalization without re-registering a product.”
The benefits, Ehrhardt said, are well worth the effort.
“By applying digital technology, companies can significantly increase visibility into their supply chain operations and make better and faster decisions,” Ehrhardt said. “Digitalization allows companies to fully integrate their supply chains and improve operational processes, making them more adaptive and responsive. As a result, planning accuracy, manufacturing efficiency and productivity, inventory levels, and service levels improve.”
Continue reading the rest of this story here, on COMPASS, the 3DEXPERIENCE Magazine