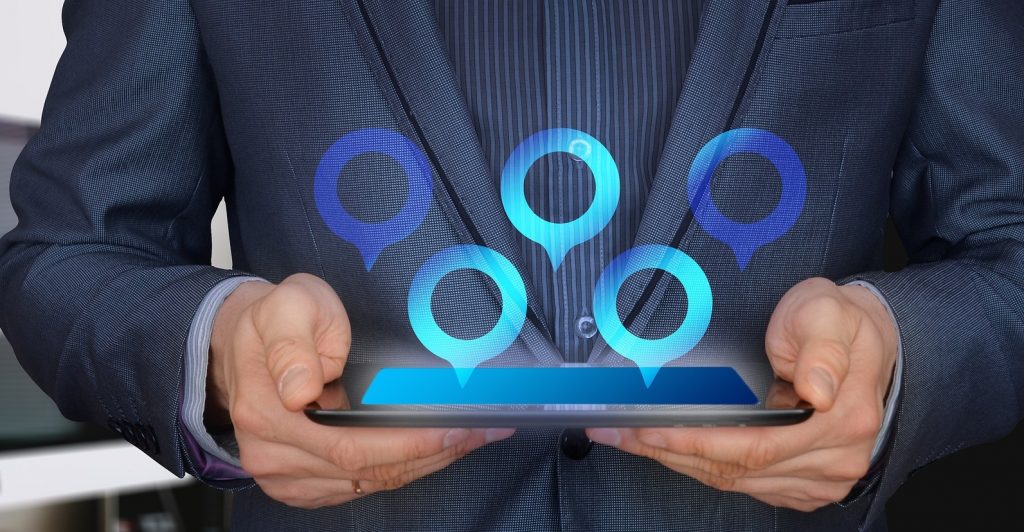
The term Digital Manufacturing has somewhat of a broad meaning that could describe many parts of today’s modern manufacturing process. In this article, we will assume the term describes the process of creating a virtual representation of each product as well as a virtual model of the entire production process. This includes everything from virtual process planning and production line design to full 3D simulation of the assembly process including robot interaction and human ergonomics impact.
These “digital twins” represent the digitized version of the “real” world product and factory production line. They provide a digital foundation to support the agility and flexibility requirements demanded of today’s manufacturers.
The creation and maintenance of a digital “world” as described above is a critical step to successfully adopting a digital manufacturing strategy. Each of the potential benefits of digital manufacturing is inextricably intermingled with the ability to establish a virtual representation of the product (Digital Twin) as well as the production environment, and to then maintain these along the entire product lifecycle.
The greater the accuracy and detail that is captured and reflected, the greater potential for benefit. Evaluating the impact of change in support of continuous improvement is exponentially less costly within a digital model than on the physical shop floor.
Those that embark on the digital manufacturing journey can expect to reap many benefits, both today and in the future. For those who are just starting or are considering whether to make the investment, here are 5 benefits you can expect to achieve, to help justify your commitment and decision.
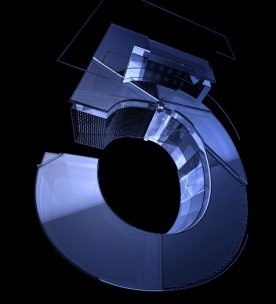
- Improve Operational Productivity – removal of paper or manual processes can lead to a significant improvement in productivity through less rework. The greater reliance upon human decisions on a production line, the greater a chance a mistake can happen. For products with high volume and low individual value, this trade off may be just fine. As product value increases, however, so too does the cost of rework. In addition, digital representations of production (or design) processes can be more cost effectively modeled, when compared to the physical world. As such, less constraints exist to experiment with new productivity scenarios, which might not have been given consideration in a “pure” physical world production environment. A digital manufacturing process that retains process consistency over time will yield greater output for the same input.
- Better Adherence to Process Improvement Initiatives – new process changes can be implemented with greater success if the new process can be easily added to the value chain, as an automated update that is more easily shared digitally across locations. For example, every time your Internet browser prompts you a new update is available and you agree to do the update, the update process performs as planned. This is an example of how streamlining process (or product) improvements can be achieved with greater consistency and widespread adoption when utilizing a digital platform to manage and schedule process improvements.
- Better Ability to Implement New Technologies – if you want to gain access to new capabilities, such as better collaboration between employees, predictive analytics, or machine learning technologies, then you will need to invest in building a digital or “virtual” platform to run and take advantage of these technologies. Just like the expression “You can’t win the lottery if you don’t play,” you can’t participate in the digital manufacturing technology transformation that is part of the Fourth Industrial Revolution if you don’t have the digital infrastructure to add new capabilities.
- Attract the Next Generation of Workers – according to a research study sponsored by Deloitte, job openings have been growing at double-digit rates since mid-2017 and are nearing the historical peak recorded in 2001. Further, the study reveals that a skills gap may leave an estimated 2.4 million positions unfilled between 2018 and 2028. The best source for new manufacturing employees is the next generation, ideally those with some education. The more you invest in a digital manufacturing suite of tools to enhance the work process and employee experience at your factory, the better chance you will have at attracting and retaining new workers. This includes remote applications to manage and report on both digital manufacturing processes and “real world” output and productivity metrics.
- Increase Operational Agility – in an always-on world with steadily increasing customer expectations, shortened product development lifecycles, and heightened global competition, manufacturers that respond faster to change can reap the benefits of increasing sales and market share. Embracing a digital manufacturing strategy across the entire enterprise can significantly enhance an organization’s ability to change quickly to new market conditions. “What if” scenarios can be easily modeled within a digital twin environment to quickly tell whether or not a potential process could work or provide insights quickly into potential challenges. Likewise, should a supplier experience a sudden interruption, a digital manufacturing strategy that extends to the supply chain could be critical in overcoming this issue faster. Replacement suppliers could be already on cue, synchronized to be available to support your production processes. This option might not be as easy to accommodate for those relying upon manual or paper-driven procedures.
As should be apparent by now, taking the time to duplicate the physical world with a digital replica offers many advantages – some obvious and some less intuitive. Identifying potential design or operations issues early in the process clearly save time, effort and resources by remedying these issues early on. Other benefits that are not as obvious is the creative freedom and potential for innovation that exists by having an environment where new possible scenarios can be more easily mapped out for consideration. In the end, those manufacturers investing in creating a digital world that replicates their physical world will reap many benefits that will translate into a competitive advantage – not only today, but for many years into the future. What side of history do you want to be on?