Part 1 of a 2-Part Series
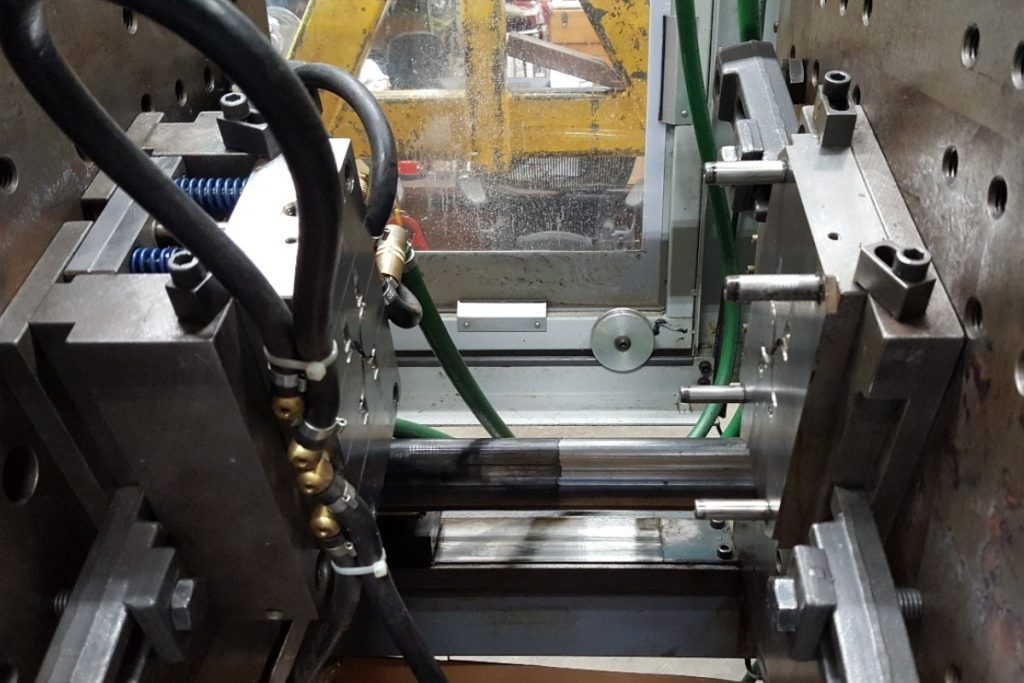
Injection molding is one of the most prolific manufacturing techniques in the world — but it’s not without potential frustrations. One of these is the time and precision required to ensure your machines, molds and build materials are interacting with one another the way they’re supposed to.
To accomplish this, an injection molding company must use either their machines’ built-in quality controls or take the next step up to either a pressure-based system or a vision-based one. For several reasons, “machine vision” is becoming the new favorite when it comes to performing inspections and calibrations of your production equipment and ensuring a steady flow of high-quality parts. Here’s what you should know.
Why Do Existing Methods Fall Short?
Injection molding specialists are likely already familiar with some of the existing mold protection techniques and products — as well as their importance in quality control and staying solvent in a competitive industry. Until this point, manufacturers typically relied on low-pressure clamps and clamp settings, pressure sensors or non-contact sensors to detect workpieces in the mold and ensure their successful release.
You may have seen demonstrations where machine operators placed extremely delicate items between the two halves of a mold. With the correct sensors and pressure settings, the mold should reverse itself automatically as it makes contact with the object, without damaging it.
These demonstrations are always a good piece of theater, but the realities of operating this type of equipment compromise its effectiveness:
- As molding machines operate, its complex components change temperature repeatedly, which can introduce changes to these delicate settings.
- Over time, even the lowest low-pressure mold close settings might result in short-shot parts and other damage to workpieces.
- Relying on pressure-based mold protection means workers spend more time monitoring and adjusting machine parameters than performing valuable work.
These combined shortcomings mean workers tend to waste valuable time and effort optimizing their machines, and that castoff parts and wasted materials are more likely.
This lack of consistency and precision to our injection molding workflows will likely bring harm to the molding machine itself. Poorly optimized pressure settings require force for the tooling to stop its movement. Even a small amount of unnecessary force could damage the machine and the mold, especially if the mold has delicate features or details. Finally, even your cycle times are likely to feel the pinch, since pressure-based systems rely on a slower closing speed for the mold.
As far as using sensors for mold protection goes, there’s a different set of complications entirely. If you deal with simple designs and tools, you’ll usually choose molds with fewer cavities. The more cavities, the more sensors the project requires — and each one needs individual adjustments. For anything but the most straightforward runs of simple parts, this is not an effective technique either, from a time or financial perspective.
For any company operating with lean principles in mind — which is most — or those that are particularly sensitive to time constraints and deadlines, it makes sense to look for a better way.
Machine vision — or vision mold protection — is a relatively unheralded technique for protecting injection molds, as well as the workpieces within.
In part two of this conversation, we’ll take a deeper dive into what machine vision looks like in practice and the types of processes which stand to reap the most benefit. We’ll also explore the potential downsides. If you’ve considered a new approach to quality control and mold protection in your injection molding projects, you won’t want to miss it.
Continue the conversation in the DELMIA Fabrication Community on SwYm. Membership is free.
https://r1132100503382-eu1-3dswym.3dexperience.3ds.com/#community:45