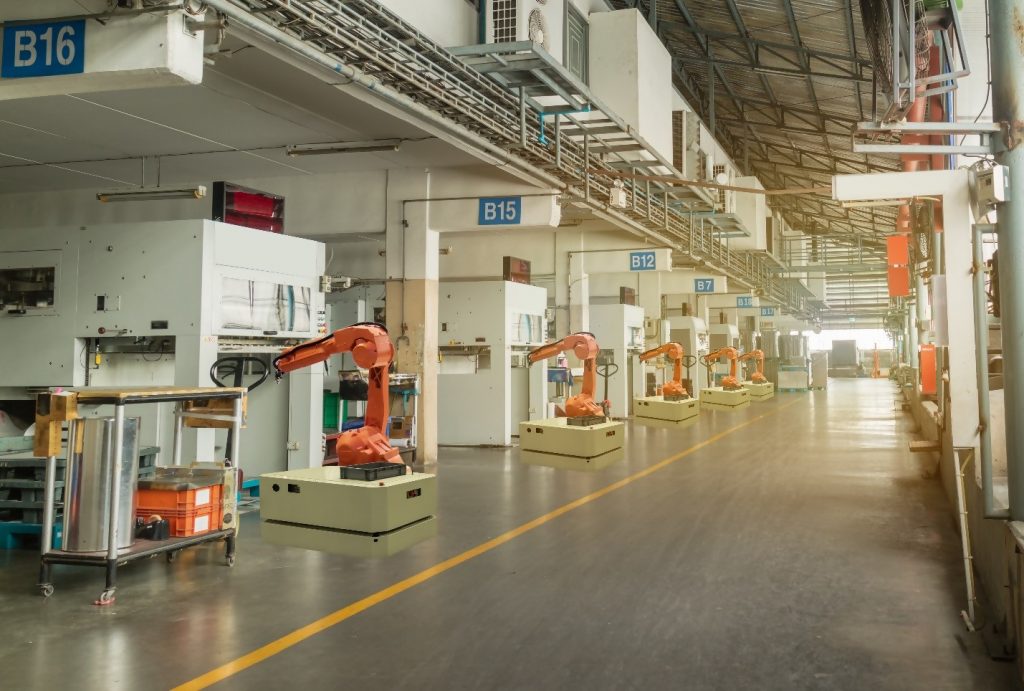
The question that seems to get asked more often than not is to talk about how many industrial applications we can name for machine learning. Well, frankly that’s the wrong question. Machine learning is not a device you can plug into a production line and make the production line operate better than it did before. Machine learning is a process that needs inputs from many devices to feed data to it so that data can be collected, evaluated, and used to develop knowledge about how a production line produces the products and parts it does. That knowledge can then be used to determine how production line can have a higher throughput of parts, operate at a lower cost, and run more reliably. In that way, machine learning transforms an industrial operation into a system of systems that can get products to market faster at a lower cost so the company that owns it can remain competitive in its market and keep their customers happy by delivering the products they want. If you’re going to put a label on that application of machine learning, it’s a higher profit margin that will create more innovative products to make the customers even happier.
Process-Based Machine Learning – A Complex Systems Engineering Solution
From Wikipedia via the peer-reviewed Springer journal, Machine Learning;
“Machine learning (ML) is the scientific study of algorithms and statistical models that computer systems use to perform a specific task effectively without using explicit instructions, relying on patterns and inference instead. It is seen as a subset of artificial intelligence. Machine learning algorithms build a mathematical model based on sample data, known as “training data,” to make predictions or decisions without being explicitly programmed to perform the task.”
Let’s add a modifier to the idea of machine learning and call it “process-based” machine learning. That allows us to get to the heart of the matter in identifying the industrial technology that had to be created or modified because of the desire to use machine learning computer algorithms to enable the era of smart manufacturing.
Machine learning uses data, or more explicitly, training data, to teach its computer algorithm on what to expect from the production machines it’s monitoring to obtain that training data, relying on pattern recognition and inference to develop the capability for the algorithm to make decisions and predictions without having to write code to be explicitly programmed to perform that task. The training data is collected, processed, and evaluated in a structured sequence of steps to prepare that data for use in the machine learning algorithm. That structured sequence of steps is a process, and the creation of that process introduces new technologies in the form of IoT devices to create the data, networks to store and process the data, and computers process and clean the data for accuracy and relevancy. That my friends is a system as represented by the image (March 2019) above. More importantly, that diagram is a system of systems (SoSe) due to the increasing complexity of its operation. We will see what that technology means to machine learning shortly.
Industrial Applications and Transformations Attributed to Machine Learning
The list of new technology that can be attributed to machine learning is exhaustive and not possible to be covered in its entirety in this article. Thus, we will hit on the higher-level issues that are more readily identifiable.
Predictive Maintenance – The possibility of being able to predict disruptions to the production line in advance of that disruption taking place is invaluable to the manufacturer. It allows the manager to schedule the downtime at the most advantageous time and eliminate unscheduled downtime. Unscheduled downtime hits the profit margin hard and also can result in the loss of your customer base. It also disrupts the supply chain causing the carrying of excess stock. The need to bring additional manpower to bear via your third-party field engineering support can cost a lot of money as well. A PwC study, Digital Factories 2020: Shaping the Future of Manufacturing, predicts that the adoption of machine learning to enable predictive maintenance is expected to increase among manufacturers by 38% because of the ability to increase profit margin by eliminating unscheduled work stoppages.
IT/OT Convergence/Network Security – The development of machine learning will also drive many business model modifications in the manufacturer standard operating procedures. That’s especially true in the organizational makeup of the company.
The computer network (IT hallowed ground) will be co-located with the operational sensors on the production machinery so that data can be collected and sent to the data warehouse as training data for machine learning purposes. There will be a need to tear down the wall of silence, separating the two groups internally and allow for collaboration and cooperation.
The floor operators and technicians will be significantly impacted if the network is not reliable or for some reason gets hacked via a denial of service attack, which will bring production to a stop. The OT sensors and devices will be affected as much as the IT network and computers. Industry Week confirms these issues.
Smart Manufacturing Digital Design and Innovation/Digital Twin Development – the ultimate objective of artificial intelligence and machine learning is to enable the development of a digital twin of the production floor. The creation of the digital twin would take place as an effort under a model-based systems engineering process (MBSE) using the machine learning algorithms and knowledge gained as a foundation. The digital twin would serve as a platform for running what-if scenarios to learn what we don’t know today. The digital twin can also serve as an end-to-end model to be used in designing higher reliability parts and adjusting the interactions between production line machines to improve performance. The possibilities are endless.
Connecting all these pieces, industrial cyber-physical systems are the primary enabling technology, which refers to an emerging data-driven paradigm focused on the creation of manufacturing intelligence using real-time pervasive networks and operational data streams. These cyber-physical systems enable objects and processes residing in the physical world (e.g., manufacturing facility), to be tightly coupled and evaluated by advanced predictive analytics (e.g., machine learning models) and simulation models in the cyber world, to realize self-configuring operations. Thus, this research presents an industrial cyber-physical system based on the emerging fog computing paradigm, which can embed production-ready PMML-encoded machine learning models in factory operations, and adhere to Industry 4.0 design concerns about decentralization, security, privacy, and reliability. (Peter, O’Donovan, Gallagher, Bruton, & O’Sullivan, 2018)
The Rest of the Story
If we dig deeper underneath the big-ticket items, there are thousands of other impacts that machine learning will have on smart manufacture ring and the industrial processes that make it all work. Other topics of interest to pursue:
- Optimized semiconductor manufacturing that can use root-cause analysis to reduce testing costs.
- Quality control and overall equipment effectiveness metrics by measuring the availability, performance, and quality of assembly equipment using the improved neural networks that can learn the weaknesses of the machines and minimize their effect on production.
- Building the connected supply chain. Logistics will always be the long pole in the tent of any manufacturing operation. Inventory management processes can be significantly improved using machine learning techniques.
Continue the conversation in our DELMIA SwYm Communities. Membership is free.