Investing in equipment for a business, whether you work in construction, manufacturing or anywhere in between, is an expensive proposition. Heavy equipment can easily cost tens of thousands of dollars, making it difficult or even impossible for small businesses to afford the expense. Leasing equipment is also an option, but when is it better to buy and when is it better to lease. Let’s take a closer look at these two options and see when you should purchase your new heavy machinery and when you should choose to lease.
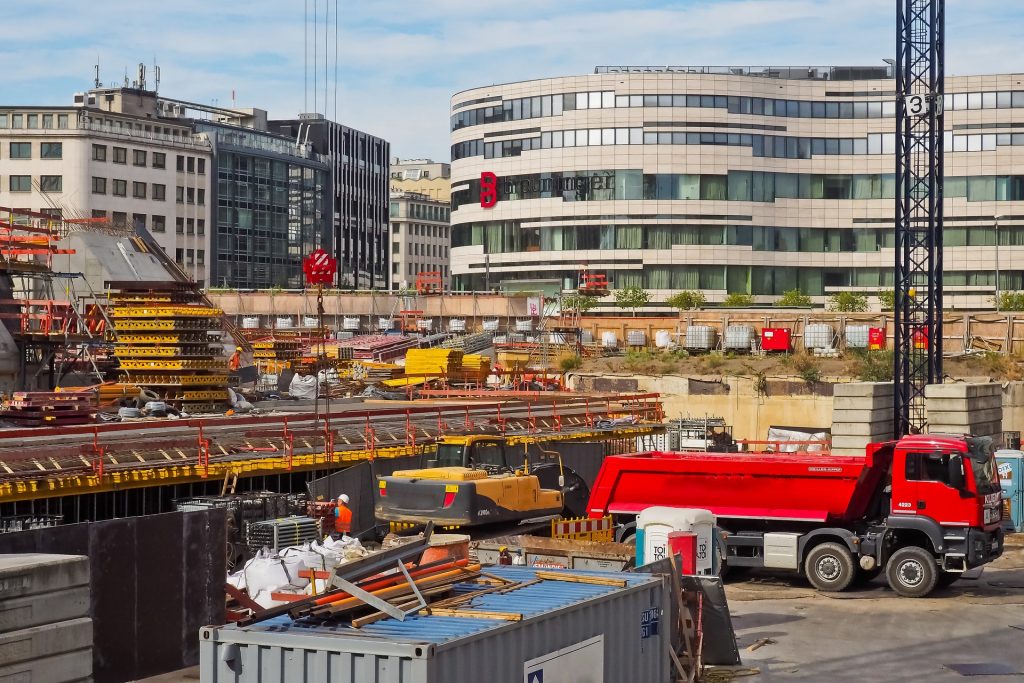
Advantages — Purchasing
Purchasing construction or manufacturing equipment is expensive — there’s no way to avoid it. There are some benefits to purchasing machinery rather than leasing it, however. First, you own the equipment outright, so there are no monthly or annual fees to continue using the equipment. There are also some significant tax breaks for purchasing new heavy equipment.
You also aren’t limited as to how you can use the equipment. If you’re leasing or renting your hardware, the leasing agency might put limitations on use, such as you can only add a certain number of miles to the odometer, or can’t run the machine in the rain, etc. With equipment you own, there are no such restrictions and you can use it how you see fit.
Advantages — Leasing
Purchasing a new piece of equipment outright might be out of your price range, which is where leasing comes in. It’s often easier to obtain financing to lease equipment than it is to obtain a loan for a purchase. While you are paying monthly or quarterly to use the machinery, you’re saving money in the long run on maintenance and upkeep. In most cases, rental and leasing companies maintain their own fleet of mechanics to keep each piece of equipment in good working order.
Leasing or renting also gives you the option to obtain specialty equipment that you might not use every day without spending the funds to purchase it. If you start using that specialty machine more than 60 or 70% of the time, then you can transition to buying it but until you reach that benchmark, you don’t need to spend the money.
Disadvantages — Purchasing
One of the primary disadvantages of purchasing your construction or manufacturing equipment outright is the cost. You’re either responsible for the entire cost up front or will need to have the credit to obtain a loan to cover the cost which also leaves you on the hook for interest charges as you repay the loan. Additionally, you will also be responsible for maintenance costs and repairs.
Purchased equipment also begins to depreciate as soon as it leaves the lot. The longer you use it, the more value it will lose, making it challenging to manage any sort of return on investment. You also have to worry about your equipment becoming obsolete — a real worry in today’s world as the Internet of Industrial Things starts to make its way into manufacturing and construction.
Disadvantages — Leasing
When it comes to leasing if you’re using this option for the equipment you use every day the costs are going to add up quickly over time. Leasing, even if all your payments are on time, does not build up any equity which makes it more challenging to obtain a business loan. You don’t get any of the tax benefits of owning, and you may even end up using obsolete or out of date equipment. Rental agencies may not have the newest equipment because it is not cost effective to purchase brand new machinery if you’re just going to be leasing it out.
Choosing the Right Equipment
Whether you lease or buy your equipment will depend entirely on your needs — and it might vary from piece to piece. Just stick to this golden rule — if you use a piece of equipment more than 60 or 70% of the time, stop wasting money and buy it. Buying equipment also helps you to build equity, which you can translate into business loans as needed.
You don’t need to own every piece of equipment on your jobsite, but anything that gets used every single day should have your name on the title. Save the leasing for specialty equipment or things that you can’t quite afford to purchase yet.