This is Part 1 of a 2-part series on how manufacturing plants operate during the coronavirus pandemic.
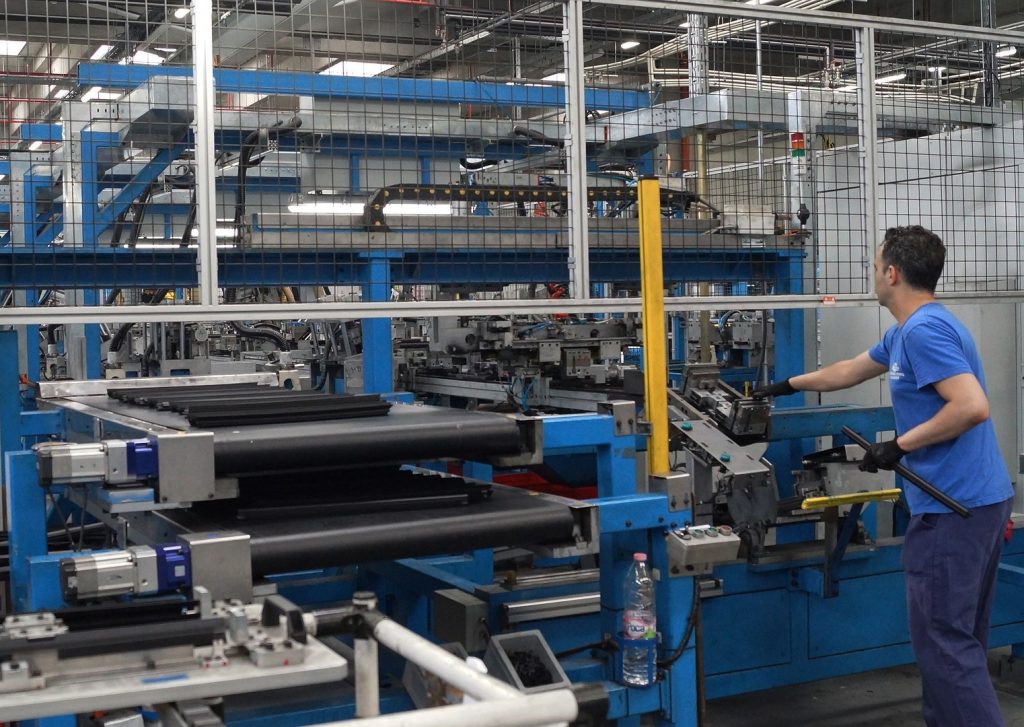
As manufacturing plants operate during the coronavirus pandemic, many efforts focus on stopping the spread of the virus and keeping people from getting infected at work. Those are valid and crucial concerns, but facility managers and team leaders should also investigate how to prioritize safety from a broader perspective. Here are some actionable ways to do that.
Create Teams Dedicated to Overseeing Safety at Work
While it’s true that staying safe is everyone’s responsibility, many companies find it necessary and valuable to build specific teams responsible for ensuring that people and locations follow the best safety practices. Molson Coors — the oldest brewer in North America — has a technical governance team at each of its locations. Then, at the corporate level, there is a centralized team responsible for employee safety and adequate working conditions.
Taking that approach gives employees a continual point of contact if safety questions arise or if people feel concerned about certain workplace scenarios. Creating teams also makes it easier to get in the habit of having all the responsible parties periodically come together to review the current circumstances.
Get Employee Input About How to Reduce Risks
It’s okay if people in a company’s top positions do most of the legwork concerning new safety practices. However, they should not do that without first consulting with the workers who spend time directly in the targeted areas. People who spend most of their time in offices rather than on the factory floor, for example, may not be clued into many of the things that worry individuals who do.
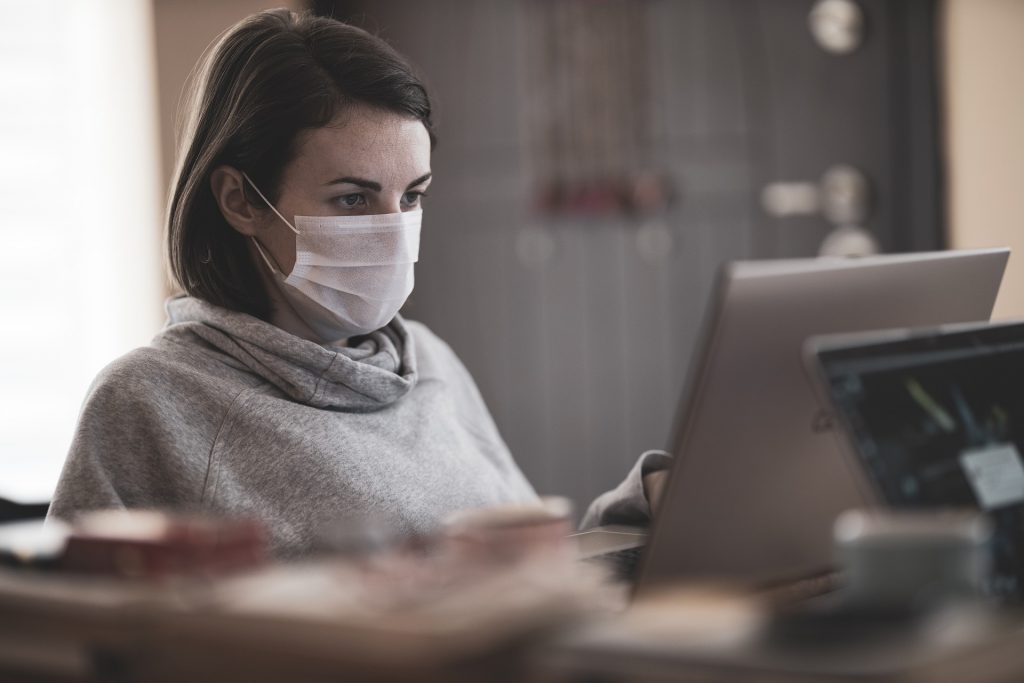
In one facility, employees expressed that they’d like barriers in the places where workers often have to stand close together to do their tasks. The company came up with a low-tech but effective solution made from PVC pipes and stretch wrap. It tried the method at one location. Then, after finding it successful, the business shared instructions with people at the brand’s facilities elsewhere.
Follow Reputable Guidance About COVID-19
Public health researchers warn that the novel coronavirus is highly contagious. Keeping people as safe as possible means most workplaces must make some changes. Plant managers should familiarize themselves with guidance for the manufacturing sector and consider the best ways to put new practices in place.
Some changes might involve modifying workstation locations so people can stand at least 6 feet apart from one another. Others may require you to invest in more supplies, such as hand sanitizer and masks. Consider how training fits into COVID-19 precautions, too. Workers may need to learn the proper ways to put their protective equipment on or take it off, for example.
Explore How to Make the Facility Floors Safer
Statistics from 2017 indicated that more than one-quarter of workplace injuries that required people to take time off the job concerned slips and falls. Part of your post-COVID-19 safety plan may involve installing a new slip-resistant option, such as resinous flooring. It’s a durable and easy-to-clean material, making it an excellent choice for high-traffic areas like manufacturing facilities.
Beyond the materials used for flooring, think about how markings on the surface could prevent injuries. You could use them to designate traffic lanes or warn people they are walking into a hazardous area. The visual cues reinforce the information employees need to know to avoid harm.
Don’t miss part 2 of this series as I explore further into manufacturing and safety.
For additional information on manufacturing during a pandemic as well as how to do more for less, read my blog, “5 Ways to Make Your Manufacturing Plant More Sustainable in the Age of COVID-19.”