This is Part 2 of a 2-part series on how manufacturing plants operate during the coronavirus pandemic.
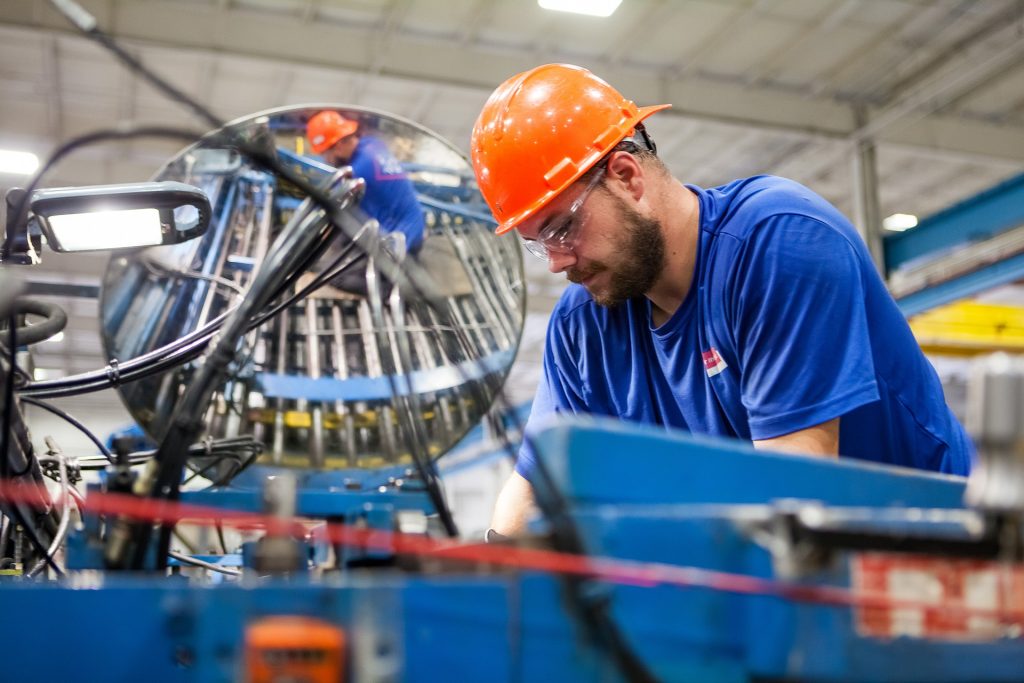
In the second part of the series, discover more as manufacturing plants operate during the coronavirus pandemic, many efforts focus on stopping the spread of the virus and keeping people from getting infected at work.
Consider Implementing a Behavior-Based Safety Approach
Most people appreciate getting positive feedback when they follow the proper procedures or otherwise perform as expected. An option called behavior-based safety uses that reality to help members of the workplace improve. It involves making objective observations about whether a person abides by safety rules and then providing comments based on what you see.
Pick several safe behaviors — usually no more than five — and focus on giving feedback associated with them. Provide corrective comments when necessary and focus on what the individual did — not the person committing the action. Provide specific things a person did well, too. Instead of only saying, “Thanks for driving that forklift safely, Anna,” tell her, “Thanks for driving slowly around that corner, Anna.”
Invest in Connected Wearables
A growing number of companies offer Internet of Things (IoT) wearables for industrial use. Those could help keep the workforce safer and alert managers to things they might miss. Some devices assist with maintaining distance and conducting contact tracing associated with the coronavirus. Others track signs that could indicate a person is getting fatigued and needs a break.
Since many of these high-tech wearables allow managers to see metrics in dashboards, they provide information that help people spot trends and increase safety. For example, a close look at the data could show that most safety-related mistakes or accidents associated with a team happen after prolonged periods on the clock. That could indicate the need to insert more breaks into the workday.
Commit to Ongoing Training
Holding regular training sessions is an excellent way to show that safety at work is a long-term priority. Some companies only host training sessions at the minimum frequency required to meet regulatory standards. Others may hold topic-based training for one day following an accident but never revisit the subject.
Even the most well-intentioned people need information periodically to help them remember safety procedures and understand the importance of following them. Getting those specifics helps safety become an ingrained part of their workdays, rather than something that occasionally pops into their minds. Educating your workers about how to stay safe proves the company takes it seriously and expects them to do the same.
Steady Progress Is the Aim
These tips will help you turn your manufacturing facility into a safer place in the post-coronavirus world. When implementing these suggestions or others, remember that you want to progressively move in the right direction without making people feel frustrated or overwhelmed. Enhanced safety is not something you can achieve and maintain in a few weeks. Treat it as a continual goal.
For additional information on manufacturing during covid-19 as well as how to do more for less, read my blog, “5 Ways to Make Your Manufacturing Plant More Sustainable in the Age of COVID-19.”