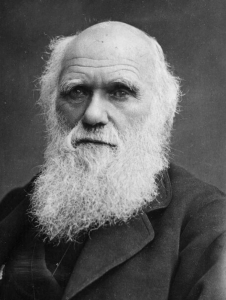
“It is not the strongest of the species that survives, nor the most intelligent that survives. It is the one that is the most adaptable to change.”
– Charles Darwin
The ability to adapt quickly to change separates the survivors from those destined to extinction. This concept exists in biology, but is equally true in manufacturing operations, especially in today’s hyper-competitive global market. Just look at the headlines to see examples every day. Companies like HP, Sony and Sharp, which at one time where the leaders in their respective markets are now fighting for their survival. While there might be a situation where too much flexibility led to indecision, my assumption is that every manufacturer seeks to improve their operational flexibility.
From a manufacturing operation perspective, what can be done to help achieve the needed agility to survive? Manufacturing operations typically does not control Marketing, Sales or Product Design, so has limited influence for change in these areas. However, manufacturing operations can have a substantial impact on areas such as product quality, production costs and on-time deliveries. It comes down to how your operations are managed. How easily can processes be changed? This is not a simple task, and in some industries it is incredibly challenging. Let’s take a look at some aspects that can create these challenges.
Companies operating in the Life Sciences or Aerospace industries are well aware of the lengthy regulations and compliance initiatives that must be completed before products can be sold. Processes must be certified, materials must successfully pass quality checks and a comprehensive traceability audit must be prepared in case of a future recall. These requirements can heavily impact the degree of change that is allowed to adapt. Any time a process change is needed, an accompanying set of validation and authentication steps must be completed to ensure compliance.
This compliance challenge has driven a transformation towards paperless manufacturing in these industries. An all-digital approval process is more efficient and easier to administer and update – as often as needed. But, with an ease of making changes, it becomes critical that a process improvement is accompanied by appropriate governance to ensure the approval process is maintained. Only authorized employees should be afforded the opportunity to perform a process change.
Regardless of whether or not you operate in a regulated industry, governance plays a role in maintaining strong control over how your processes are standardized across plants. Without this standardization, simple tasks such as product numbering consistency, product returns, RMA documentation and packaging guidelines would vary from plant to plant, increasing process variability and inefficiency. Beyond your own “four walls,” improving operational flexibility means that your suppliers must also be capable of responding quickly to change. If suppliers can’t re-program delivery schedules to occur consistently with the right documentation for every delivery regardless of how often it changes, then your ability to respond quickly to a product shift or market demand change will be significantly impacted.
From a labor perspective, if you decide that a specific plant must now start producing a new product – perhaps to meet unexpected demand – then your ability to respond quickly to change will be hurt if your staff must be trained prior to performing this type of change. Manufacturers that have consistently standardized their production processes across plants will be able to more easily adapt to change. This standardization can’t occur without the right governance processes in place to ensure standardization compliance throughout the enterprise.
Lastly, when it comes time for a new product introduction, those manufacturers that have effectively standardized their processes surrounding a product launch will be better suited to adjust as new feedback is gained from the marketplace. Packaging changes, new distribution practices or pricing modifications will all be more readily accomplished with consistent business processes across locations. This standardization translates into a faster response to change and a more successful product launch.
How well do you govern your processes? Is change time consuming and expensive, or a condition that you have mastered? If you seek to improve your agility, perhaps process standardization might be a good next consideration to explore?