How digitalization can help manufacturers build smart, efficient and sustainable processes
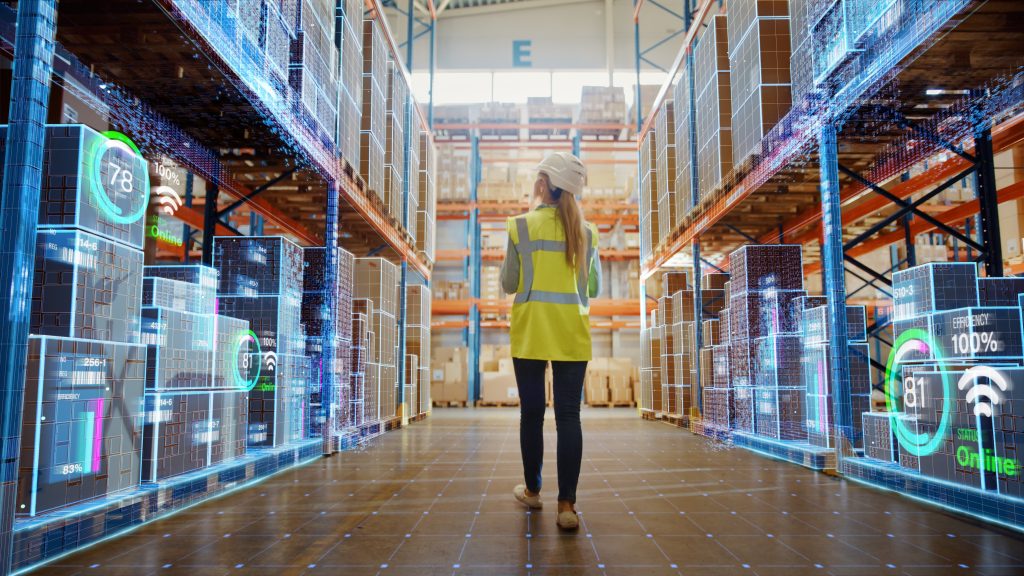
As the Paris Agreement’s carbon-neutral target draws closer, more and more manufacturers are beginning to make sustainability a business priority. Today, the manufacturing industry alone is responsible for 54 percent of the world’s energy consumption and 20 percent of carbon emissions. It is high time that industry at large take the right corrective and transformative steps in order to help realize a greener way of working.
The Ellen MacArthur Foundation addresses that by adopting a circular economy, the manufacturing industry can save up to US$630 billion a year on raw materials in the EU alone. Though there are many leaders now making the switch to energy efficiency and sustainable manufacturing practices in their plants, there is still a ways to go in order to improve their processes. Manufacturers need to adopt a disruptive digital solution in order to achieve their sustainability goals and continue tackling climate change as well as ensure business longevity and relevancy.
Digitalization to drive circularity and waste reduction
The Ellen MacArthur Foundation, in collaboration with Material Economics, highlights that 45 percent of global carbon emissions can be eradicated simply by rethinking manufacturing, distribution and production. Manufacturers can apply circular economy principles in the five keystones of manufacturing, which are aluminum, cement, steel plastics and food. In doing so, they can help advance carbon neutrality—equivalent to cutting current emissions from all transport to zero.
This can be achieved through the digitalization of manufacturing operations for sustainable practices. Dassault Systèmes can help facilitate this with the 3DEXPERIENCE platform and Virtual Twin Experience—the latter of which is a key digital enabler.
Using the 3DEXPERIENCE platform, manufacturers can create a virtual 3D model of their physical processes. The Virtual Twin Experience, powered by the 3DEXPERIENCE platform, enables manufacturers to optimize their processes from product design to manufacturing through sustainability-focused decisions, allowing them to create a digital thread and infuse sustainability from start to finish. By simulating hundreds of different scenarios from every point of the digital thread, manufacturers can make responsible choices—from purchasing raw materials to creating a sustainable value chain.
Realize sustainable value through innovation
Digitalization will continue to make its way through the manufacturing industry. Those who have already embraced technologies like artificial intelligence (AI) and the Internet of Things (IoT) are set to gain a competitive advantage in terms of price points and time to market.
Such digital capabilities are what ignite and sustain the circular economy. The Virtual Twin Experience found on the 3DEXPERIENCE platform fosters sustainable innovations by giving manufacturers end-to-end visibility of their processes. Leveraging this, manufacturers will be able to see a significant drop in valueless by-products, likewise the reliance on precious non-renewable resources, while being able to optimize waste management and extend material lifespan.
Read the full article, “Circularity Requires Digitalization” to learn more about how to achieve sustainable manufacturing with the power of Virtual Twin Experience. Plus, discover more resources, including:
An event replay, “Two Heads Are Better Than One: Accelerating Sustainability Through Virtual ‘Twin’ Technology” to uncover how emerging virtual twin technology can help you transform your business to become more sustainable.
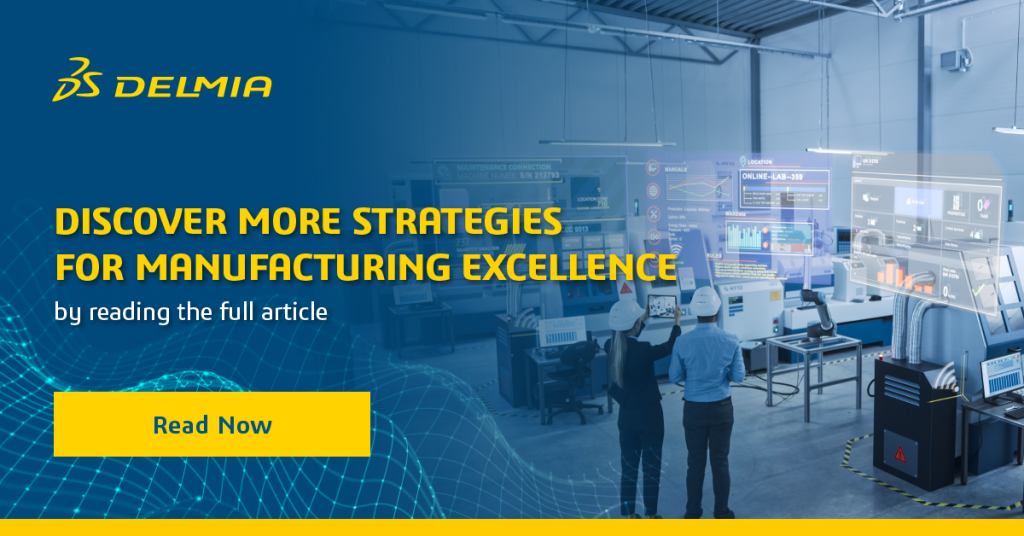