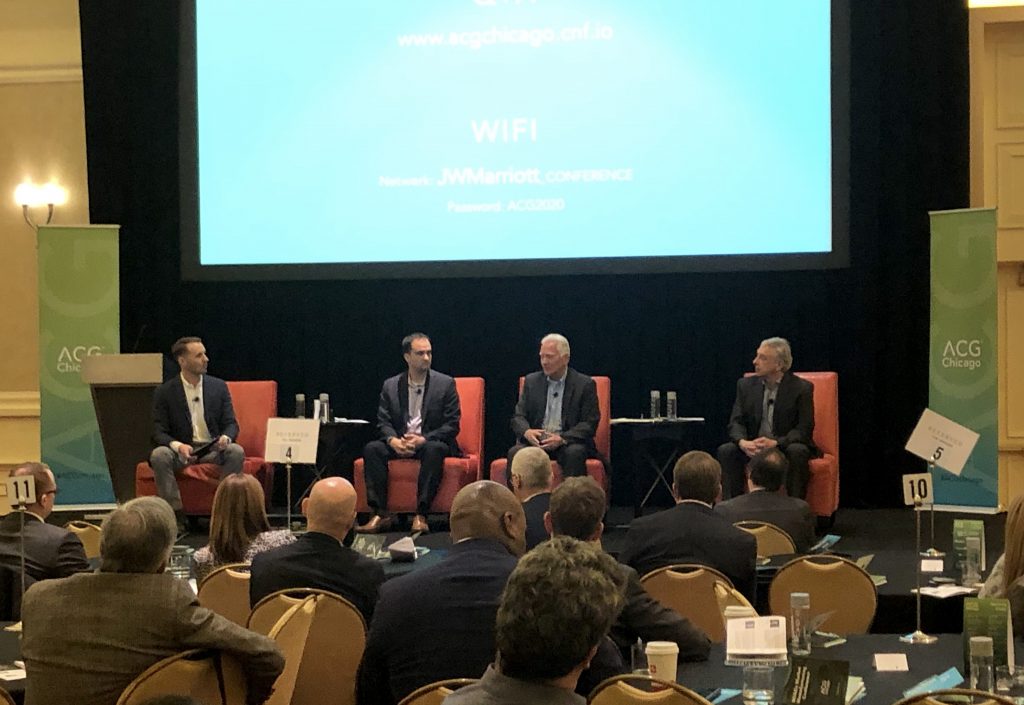
We are more than six months into the COVID 19 global pandemic. We all have read about the toll this has taken on humankind. However, Covid as a global crisis has been also called the great enabler: we are discovering many things that we did not know about ourselves. With a small, fast pivot of the business and supplies we can enable companies to do things they thought they might not have otherwise been capable of doing.
As a crisis, it is clear the Coronavirus took the world by surprise, and in retrospect, the world was less prepared than we would have liked. Covid has also revealed issues like the frailties in many areas of global supply chain: shortages created when raw material needed to complete a product are stuck at a border, and the pandemic holds those materials indefinitely. Or, the importance of digitalized manufacturing and how digitalization has enabled companies to pivot faster to new and more innovative products, processes or never-produced products needed to save lives in the pandemic.
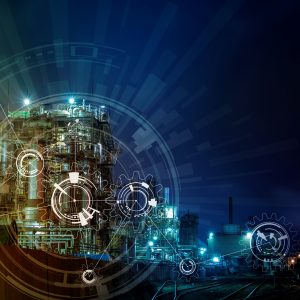
Digitalization has enabled companies to pivot faster to new and more innovative products, processes or never-produced products needed to save lives in the pandemic.
Earlier this year BC (Before Covid) I participated in in a panel discussion. The topic was “leveraging technology to achieve operational excellence”. This is even more applicable now than six months ago. At that time the audience was the Association for Corporate Growth Chicago (ACG Chicago). This 300-plus audience was primarily the financial arms of many mid-market manufacturing companies with a focus on turning operations and improvements into ROI. There was a real need to understand the value of change and improvements in manufacturing in terms of financial benefits or costs.
There were two primary issues to the discussion: how do we accomplish the goal of operational excellence and where do we start? One place to start is in assembling a well-represented, well-formed steering committee. Identify metrics, analytics and projects to drive business improvements. Determining which technologies to adopt starts with solid project governance and understanding the maturity and readiness of your plant’s ability to accept change.
The discussion was well-received and planted seeds for at least a starting point. A few lingering question that came out of this were:
- Should we re-shore our supply chain? What percentage of that supply chain makes the best financial sense and what are best practices?
- What is the value of digitalizing the manufacturing?
- Can a small to mid-sized business afford to digitalize?
These became coffee break side bars.
Coronavirus took the world by surprise. DASSAULT SYSTÈMES has been on the path of enabling manufacturers with digitalization tools for many years. When science and the digitalization of manufacturing meet on the factory floor, it leads to what Scott Galloway of NYU Stern says: “Coronavirus is the great accelerator”. That means turning the impossible to the possible like producing ventilators for the world, with a global team from open-sourced plans shared by MIT. DASSAULT SYSTEMÈS is proud to have been a part of that and much more. With all those who have been doing their part to design and simulate construction of a new hospital. Sixty-percent of all worldwide COVID-19 trials are being monitored using a Medidata platform. These are a few points worth mentioning.
All of this makes me hopeful we can come together and solve these global problems together.
I wanted to thank Craig Smith of ACG, Joel Schneider of Liberty Technologies, Sargon Guliana of the Deublin Company and ACG Chicago for letting me share your stage and for the great conversation.