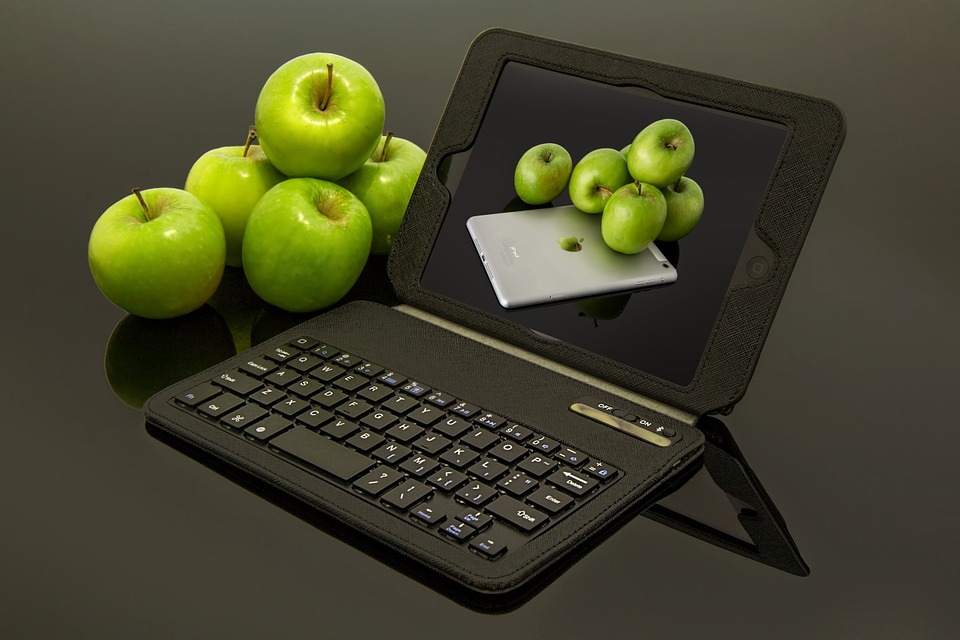
The concept of a digital twin has been around since 2002, first introduced by Dr. Michael Grieves as part of his research agenda at the University of Michigan. He had a vision that a Digital Twin could be created as a virtual representation of a physical product. Today’s technology, including the Internet of Things, advanced simulation, and highly sophisticated laser scanners, can now create a digital representation of almost any physical object. But, are all Digital Twins created equal? Has this concept now become a generic commodity?
The Two Types of Digital Twins
First, let’s better define what we mean by a “Digital Twin.” Then, we can proceed forward with an evaluation of the core attributes that should be considered in the evaluation of an “ideal” Digital Twin.
The Product Digital Twin – this twin is a virtual model that simulates how a physical product might appear and respond to changing environmental conditions or usage patterns. This Digital Twin simulates wear and tear, how materials might change under extreme heat or freezing conditions, or where the product might break in a real-world usage scenario. This knowledge can then be used to engineer a better, more reliable product.
The Production Digital Twin – this twin considers what goes on after a product has been designed and engineered. Here the focus is on the systems that will be used, which will define how it will be built, with what process, and in what order. How will the supply chain be managed, what equipment will be involved, and how will post-production support be provided? This Digital Twin extends beyond the four walls of a manufacturing enterprise and out across the extended value chain. By simulating these activities, it is possible to accelerate the ramp up of initial production for new product introduction, as well as be a source for future process improvement.
Before the Digital Twin
Computer Aided Design (CAD) applications trace their origins to the late 1950s when Dr. Patrick J. Hanratty developed PRONTO, the first commercial numerical-control programming system. In 1960, Ivan Sutherland MIT’s Lincoln Laboratory created SKETCHPAD, which demonstrated the basic principles and feasibility of computer technical drawing – the foundation for computer simulated images (source).
We have come a long way since that time. Virtual representations of the physical world are now quite common. The popularity of video games is just one example. CAD/CAE/CAM systems are now in use across a huge number of industries. Solution providers, such as Dassault Systèmes, are leading the way by offering innovative, robust simulation engines with far greater detail and sophistication than what was ever considered possible back in the 1950s.
The Future of the Digital Twin
A guiding principle led to the birth of a Digital Twin – this principle still holds true today. The sooner in the process that a change can be implemented, the less of an impact on productivity or the bottom line. Further, the closer or more accurately a digital simulation can reflect physical reality, the better it will perform in providing advance notification. The future of the Digital Twin will be led by advances that improve the accuracy and usability of the data and the user interface.
Here are a few of the top use case examples of how a Digital Twin is used today:
- Improve product quality
- Shorten NPI lead times
- Reduce manufacturing startup costs
- Increase throughput
- Ensure safe manufacturing
Better detail and accuracy of engineering and design specifications generates a more valuable Product Digital Twin. Similarly, better visibility into the production process will result in a Production Digital Twin that is more sought after. It seems reasonable to assume that the pursuit of better accuracy and visibility will continue to define the next generation of Digital Twins.
Any steps that you can take to streamline the process of obtaining greater accuracy and visibility in your Digital Twins will lead to greater process and operational excellence. Dassault Systèmes has taken a unique approach by offering Digital Twins that cover both realms – Product and Production. By creating a seamless integration flow of both twins, customers can better leverage this intelligence as an integrated component to a higher number of manufacturing, design and production processes.
The better these applications are integrated or operate from a single platform or user interface, the easier they will be to use and optimize, generating greater value. This is simply due to the fact that the data will be cleaner and more readily accessible as often and as quickly as needed.