Seeing a virtual product in 3D on a computer screen is good, but the small screen makes it easy to miss the fine details of complex products – details that could be expensive to fix later. The arrival of low-cost head-mounted displays is eliminating that challenge, allowing designers and engineers to experience their creations at life-size scale.
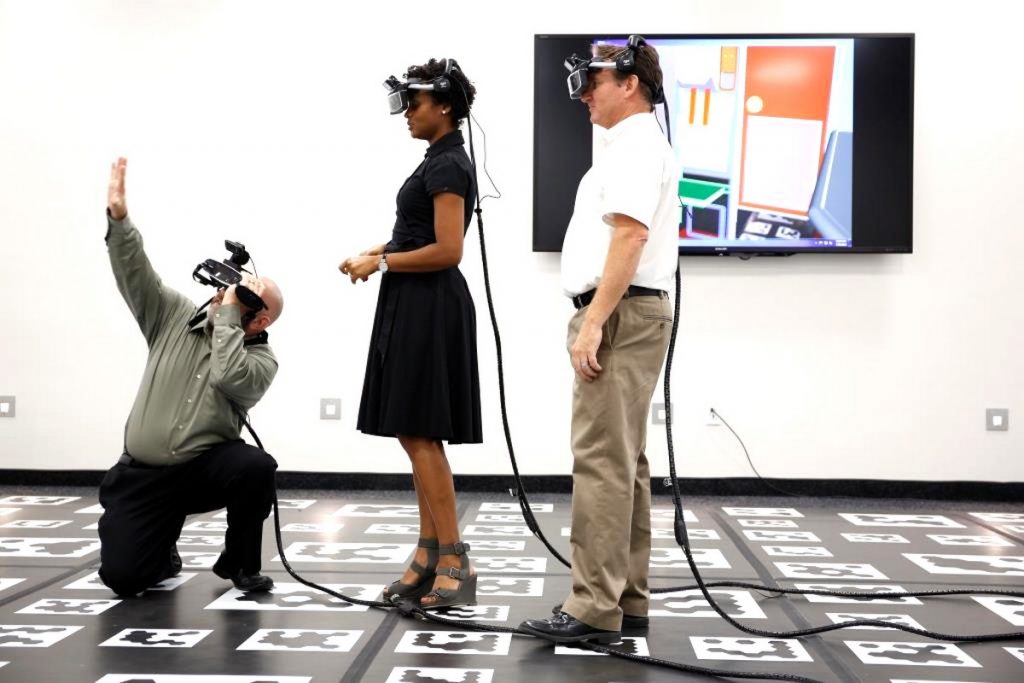
Development of 3D design software revolutionized product development. The ability to see those 3D models in immersive virtuality (iV) is about to revolutionize it again.
“VR allows you not just to look at the 3D models, but to experience them,” said David Nahon, director of Immersive Virtuality at 3DEXPERIENCE Lab at Dassault Systèmes (publisher of Compass). “That is a game-changing development. Looking at a model on a desktop is good, but the full-scale experience of the model gives you the capacity to asses a lot of elements you might not notice on the small screen, before you invest in any further expensive development.”
The world’s wealthiest corporations have used iV technology in Virtual Reality (VR) CAVEs for nearly two decades, but high cost and complexity limited its use primarily to expert users in design and engineering. Low-cost head mounted displays (HMDs), newly introduced in 2016, are making immersive experiences available to companies of all sizes, however, while expanding access to more users than could ever fit in a CAVE.
“Many manufacturing industries have interest in VR,” said Hervé Fontaine, vice president of B2B Virtual Reality for HMD maker HTC Vive. “With the product lines of Vive designed specifically for enterprises, anyone who is using 3D software can suddenly view their model in VR.
“Rather than building a physical prototype to look for mistakes, they will be able to spot errors in VR at a much earlier point in development than they have been able to do on a computer screen, which will save them lots of time and money.”
Continue reading the rest of this story here, on COMPASS, the 3DEXPERIENCE Magazine