Steel plays a crucial role in almost all industries—even in those where its application is not as apparent. The food industry, for instance, depends on steel for its use in building greenhouses. Steel is a very versatile material as its composition and internal structure can be adjusted to tailor its properties. It can be made with many different characteristics, for example, different chemical compositions to increase strength, durability, etc.
There is another important aspect of this material: recyclability. Steel is one of the most recycled material in the world. Steel scrap can be blended through the recycling process to produce different types of steel to meet changing customer demands. For example, old steel used in an industrial context can be recycled into consumer products such as home appliances, automobiles and more. As such, steel will be the backbone of the future circular economy. In the following graphic, you can see why steel already has excellent circular economy credentials and can even have the potential to drive more sustainable operations for many organizations.
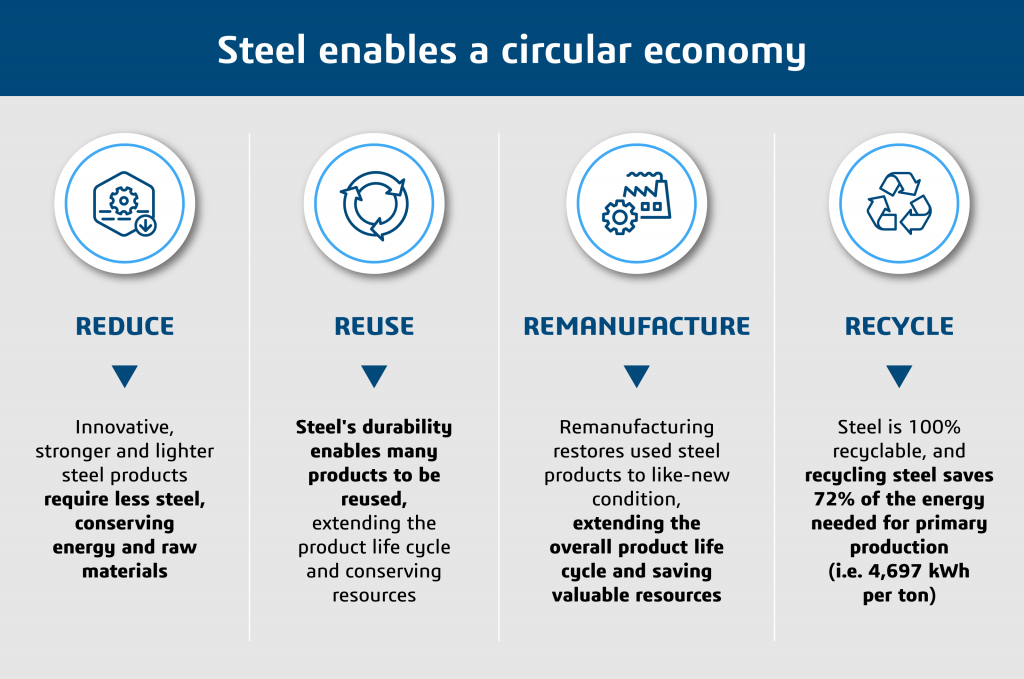
Although steel can extend the life cycle of products and is a key enabler for a circular economy, the steel production industry itself is lagging in terms of sustainable practices and operations. The production of steel is an energy-intensive manufacturing process and the amount required for it is typically generated by burning fossil fuels whose carbon emissions further contribute to the global climate crisis. Reaching the goal of ‘net-zero’ emissions will require digital transformation. Though many steel producers have already started their transformation journey, the transition to green steel won’t happen overnight as significant investments are needed. Also, it is unclear how long this transition, for example, the adoption of green hydrogen-based steel, will take.
Furthermore, the introduction of new technologies also presents more challenges for steel players. Green hydrogen-based steel, for instance, creates the need for a significant capacity increase in electricity derived from renewables. Instead of waiting for those large-scale changes to happen, steel manufacturers can start now and transform their operations for greater efficiency. However, there are still barriers in the technology domain, which revolve around business process factors that each steel producer can (and should) start to tackle immediately.
Technological challenges
Steel manufacturers need digital tools to drive better, faster and data-driven decision-making as well as implement more sustainable practices. However, due to the reliance on largely manual processes such as legacy planning tools and systems, the industry has been struggling to keep up with the pace of innovation, let alone sustainability. In addition, increased traceability of steel products and better sorting and monitoring of inventory depends on digital and automated processes for faster and more efficient processing. Overcoming this challenge means digitalizing steel manufacturing and operations across the supply chain to improve visibility and agility.
Supply chain challenges
The steel industry is in great need for supply chain innovation. Better visibility and collaborative planning of the entire value network is essential: scrap producers, steel manufacturers and downstream users all need to better align their strategies to drive more efficient, sustainable production. As volatility has been the dominant feature in the industry, accurate demand and supply planning is necessary for the creation of lean plans, enabling the development of various scenarios and data-driven decisions that are in line with organizational objectives.
Daily business challenges
Daily disruptions in the form of production timeline pressures, equipment downtime, and more are aplenty on the steel production floor, which make controlling operating costs and maximizing profits an even bigger challenge to manage. Furthermore, the fluctuation of metals prices due to shifting demand patterns impacts steel producers’ already thin profit margins. Here, production optimization plays a key role in helping steel producers cope with such changes. An integrated platform approach to optimizing production, scheduling and execution will enable steel players to get a leg up in this area.
Technology trends that drive the modernization of steel production
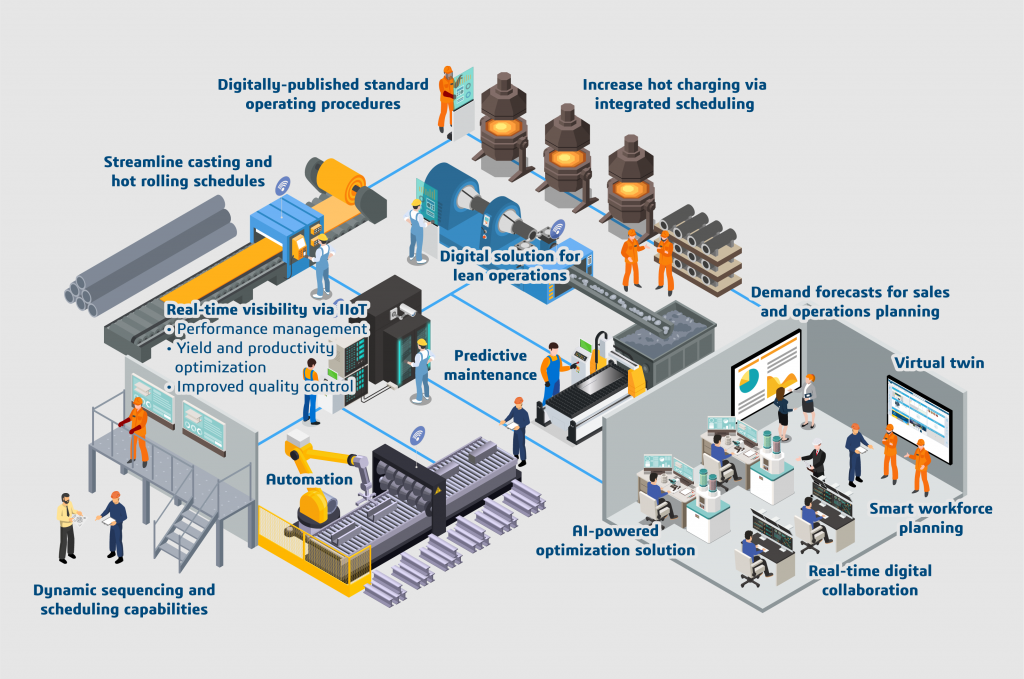
The graphic above highlights key metals manufacturing trends that are in place today. Driven by a spectrum of technologies, including automation and robotics, artificial intelligence (AI)/machine learning (ML), IIoT and analytics, these trends will require the following digital capabilities:
- Automation, robotics and operational hardware to digitize and automate processes for faster and more efficient processing.
- Digitally enabled workforce through digital connectivity (connected mobility, VR and AR).
- Integrated enterprise, platforms and ecosystems for identification of supply chain issues and root-cause analysis.
- Next-generation analytics and decision support for operational flexibility and efficiency.
7 competitive capabilities for sustainable steel transformation
Enacting these trends requires the right solution to support your business’ unique needs and goals. DELMIA, powered by the 3DEXPERIENCE® platform, offers these capabilities that culminate to form a complete solution for sustainable transformation, tailored for the steel industry.
- The Virtual Twin Experience: Enables an accurate virtual representation of your supply chain and operations, allowing you to test and optimize processes and resources before executing them in the real world.
- Sales & Operations Planning (S&OP): Bridges the gap between business strategy and operations, with CO2 emission KPIs that can be considered in the optimization strategy and leveraged to make trade-offs during planning and reporting.
- Master Production Scheduling (MPS): Helps fine-tune supply and demand data and forecasts to deliver accurate and timely production plans throughout the entire production supply chain, including increasing delivery performance for customer orders with more realistic delivery expectations.
- Detailed scheduling: Helps plan material flow, combine orders and create batches to generate ideal sequences in order to find the right balance between optimal production efficiency and best delivery performance.
- Collaborative operations: Empowers the steel workforce to find new ways to innovate by bringing people together in a structure that guides discovery, analysis and better collaboration.
- Manufacturing Operations Management (MOM): Provides a comprehensive core platform for manufacturing excellence, enabling you to control and synchronize operations on a global scale.
- AI/ML-driven platform: Helps create a value network of the future through closed-loop, intelligent decision automation in all components of the supply chain.
To learn more about how to transform your metals organization for sustainability, resilience and operational efficiency, read our latest eBook.