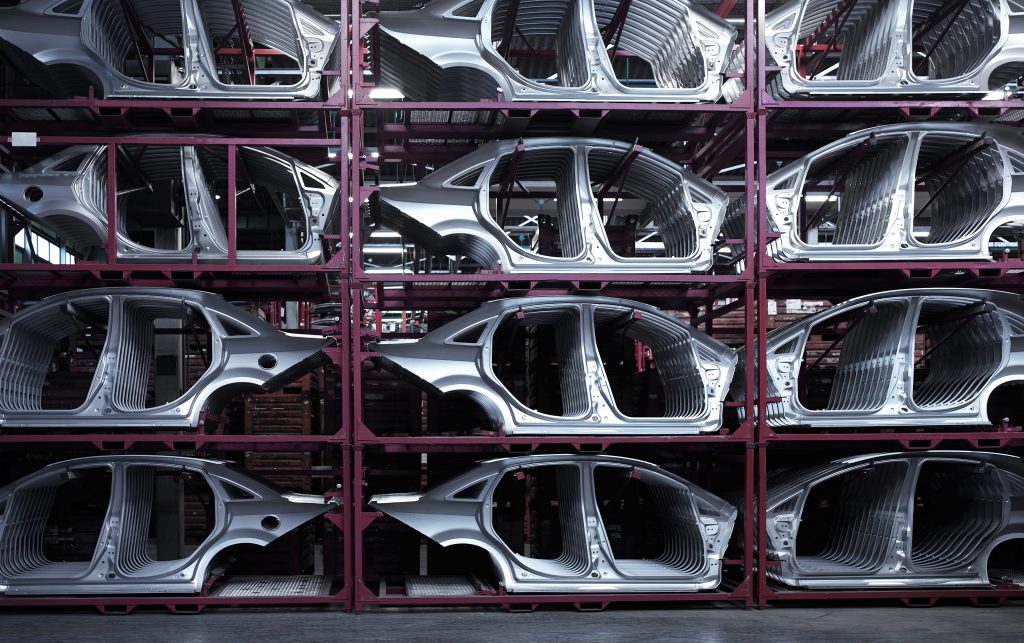
Today’s supply chains are becoming more complex and dynamic. For the automotive industry in particular, the transportation of goods – small, large, custom-made – needs to run as smoothly as possible. Logistics processes and strategies must be able to adapt to this multivariable environment and accommodate these demands, down to the smallest detail.
While the automotive industry is proactive in developing strategies to optimize manufacturing processes, many important aspects are siloed, especially one crucial element: The container, which plays an important role in ensuring seamless logistic processes.
Product variants determine the characteristics of the containers’ shape, form and size. Sometimes, the containers are small boxes that hold hundreds of screws and sometimes they are custom-made units that transport large doors. The need to manage special container returns further complicates the situation.
Before planners make decisions that will have an impact across the value chain, they need to consider a number of possibilities such as having multiple exchange ratios of specific components when managing container returns.
Planning for complexity
The final assembly line sets the pace in automotive manufacturing. At this point in the production chain, suppliers throughout the complex delivery network must deliver their products just in time (JIT) and just in sequence (JIS) for vehicles to be assembled as planned.
Not having the right container in the right place at the right time can jeopardize entire automotive supply chains, resulting in costly production downtimes. To mitigate and eliminate these costly risks, manufacturers need to involve container management much earlier in the planning process.
By integrating and optimizing container management, your planners can:
- Foresee the containers’ characteristics for different products and the effects they have on the transport and production plan
- Minimize the risk of inefficient returns management, and
- Consider diverse scenarios in the production chain before making decisions.
With the right planning solution, planners can examine the interplay between varied parts and containers from pickup to storing to unloading – all in the correct sequence, well before they execute their plans.
Furthermore, this planning solution should help intensify product protection, reduce labor and increase efficiency in freight and storage to directly reduce operating costs.
A robust system that calculates the details of each scenario enables planners to confidently make the right decisions with complete consideration for total freight costs, schedule adherence, kilometers driven and further production. They can also propagate any changes or decisions in real time across all areas, driving cost efficiency.
One integrated plan
Planners need to deploy the right strategy in the dynamic supply chain ecosystem, and integration is the answer. Planners can then include container management early on and determine the best scenario for the entire supply chain. This is because containers are an important resource to manage well, along with production resources, tools and other key equipment.
For optimized container management, planners need to have a single production plan that covers multiple production resources and assembly lines within a manufacturing plant. This gives planners full transparency and the freedom to plan beyond silos.
An integrated planning solution must also be able to propagate and display the effects of changes, decisions and disruptions in real time across all production steps. This enables planners to automatically check the availability of all resources such as materials, containers and appropriately skilled staff. Data from previous plans and the planner’s experience can also be used to enhance plans.
With integrated planning, planners can have the confidence to optimize complex automotive supply chains as they work on a single source of truth. To further optimize your results, rely on 3D simulation capabilities so that your teams can optimize various container designs as well as simulate container and product behaviors.
The result? Reduced freight and handling costs, increased efficiency during the transportation process and enhanced critical problem solving.
Find out how you can optimize your automotive logistics strategies here.