Introduction
There are many online videos of collaborative robots cooking pancakes, serving a cup of tea or mixing cocktails, but it is difficult to find serious information about the simulation of these Collaborative Robots, or Cobots. But from an industrial point of view, keep in mind the production fundamentals: Human safety, ergonomics, performance, quality, offline validation, installation set-up, and training. How does Simulation integrate these concepts and result in the best compromise?
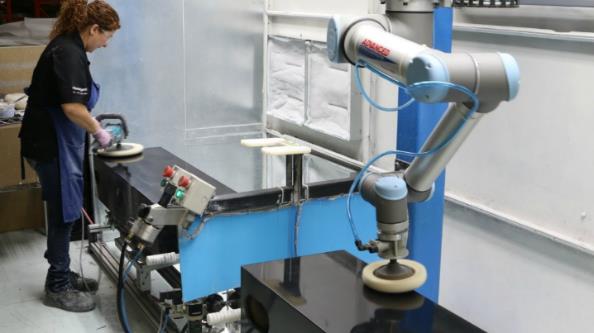
What is Cobotics?
Wikipedia defines a cobot, or co-robot (collaborative robot) as a robot intended to physically interact with humans in a shared workspace. This is in contrast with other robots which are designed to operate autonomously or with limited guidance.
Other basic definitions include:
- Humans working with a robot or vice versa
- Humans working with a robot not protected by materialized fences
- Humans assisted by an articulated and motorized actuator
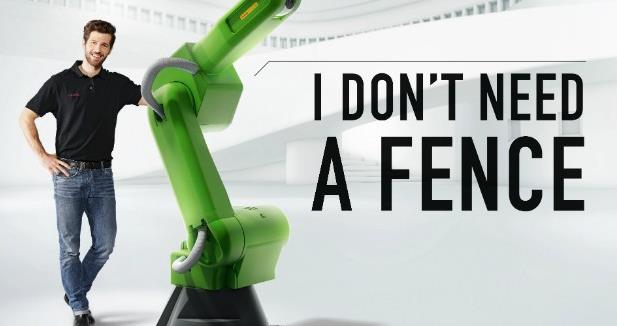
Examples of Cobotic Applications
Loading / Unloading End Effector or Tooling – for this process, the human and cobot perform the same task in a shared workspace, which is the value provided by a collaborative environment.
Hand Guiding – Lift Assist – Load Positioning – the human is assisted by an articulated and motorized actuator in a shared workspace. This type of collaborative task reduces the frequency of repetitive actions and allows for a better working condition.
The Value of Simulation in Cell Layout Design
Secure Accessibility for both humans and robots
Simulation enables users to detect possible collisions, even during a simple process. In this scenario, the simulation illustrates a possible collision between the cobot and the product being produced (the seat) To avoid the collision, the operator simply needs to move the seat onto the conveyor. Now the issue is easily corrected, resulting in a shorter ramp-up of the production phase.
Secure human tasks using ergonomics validation
Ergonomics simulation provides the relevant tools to ensure that workers avoid injuries and have the best working conditions. This allows non-ergonomic experts to easily see how workers will perform their tasks.
Human / Robot interaction validation
Simulate in real time the collaborative tasks between humans and robots.
Simulations and demos help to demonstrate the human and cobot interaction. Take the simple process of a turbo being mounted on an engine. This picture shows the human doing the most complex tasks involving flexible parts such as air hoses. The cobot is positioning the turbo, which would be tiresome for the human. By placing the turbo at an optimized position, the human can perform his tasks in a comfortable position.
Optimize production capacity
In this turbo mount use case, despite the narrow shop floor surface, the simulation validates the cobot / human interaction to include takt time verification.
Human Safety Compliance
Human safety is one of the most critical challenges as cobots are not fully protected by fences. The Industry has produced safety standards such as ISO/TC 15066, which is dedicated to cobot installation. Thanks to the immersive experience, Simulation takes this important safety standard into account.
This picture shows the obvious danger faced by the operator even when working with an “intrinsic secure cobot”. For workers, eyes remain the most critical risk, as simple contact from a cobot can dramatically damage human eyes.
The second picture simulates a work cell station with immaterial walls that reduce the speed when the operator’s hands approach the cobot, or completely stops it when he gets too close. These types of use case simulations are possible and can be validated thanks to the Virtual Commissioning environment. More on Virtual Commissioning, which is the process of using simulation technology to test plant changes before actual changes take place, in a future article in this series.
In a future blog, I’ll elaborate more on the Virtual Commissioning environment as well as additional benefits in Cobot Simulation.