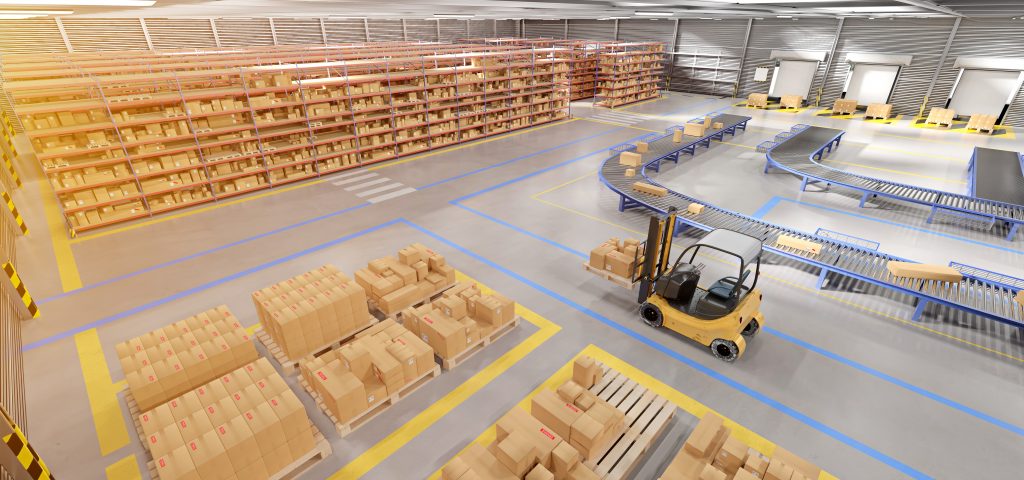
In this blog series, I’ll take a look at the current state and future evolution that can be expected within the world of supply chain planning software through the lens of Dassault Systèmes DELMIA.
You will discover:
- A detailed overview of what supply chain planning is
- An explanation of the importance of supply chain planning for manufacturers
- A breakdown of the key elements in supply chain planning including demand planning, supply planning, sales and operations planning, production scheduling, integrated business planning, logistics planning and workforce planning
- A summary of the key advantages afforded by great supply chain planning and a short introduction to how DELMIA are uniquely positioned to help
What is supply chain planning?
Before I get into the software itself, it is useful to start with something of a definition of the supply chain management process itself prior to moving on to the solutions that support it.
A compact definition is especially useful in this case, as supply chain planning software comes in so many guises and has so many functions. It can be daunting to navigate the landscape of modules and features, even for long standing veterans of the industry.
For the purpose of this blog, I will make use of the Association for Supply Chain Management (ASCM) definition as follows:
Supply chain management is defined as, “The design, planning, execution, control, and monitoring of supply chain activities with the objective of creating net value, building a competitive infrastructure, leveraging worldwide logistics, synchronizing supply with demand, and measuring performance globally.”
From this definition alone, several planning puzzles that any software solution will need to cover in order to meet the multifaceted challenges posed by supply chain management (SCM) are revealed.
For example, several potential topics can be selected from this definition such as:
- Supply chain design
- Supply chain planning
- Supply chain execution
- Supply chain monitoring and control
- Supply chain logistics
- Supply chain performance and net value
For each of these areas, one or more software applications may be used, either as a collection of best-of-breed solutions, or as part of a fully integrated digital platform. Whichever approach is taken, the key objectives of this software solution can be typically summarized into three core areas:
- Improved visibility
- Improved decision making
- Improved collaboration
Why do manufacturers need an effective supply chain plan?
Necessity, as the saying goes, is the mother of invention. The necessity for the advanced supply chain planning software solutions comes from the ever-increasing size, scope, complexity, and interconnectedness of today’s supply chain networks.
It is no longer sufficient to strategize in months, plan in weeks and execute in days. Instead real-time network status updates and immediate propagation of the consequences across the supply chain network to trigger immediate updates to the planning proposals–including automated scenario generation and scoring–is the order of the day. Leading companies strive to have the right product in the right place at the right time for the right price with the right margin. Add to this the lowest environmental impact possible.
Without an effective supply chain plan, manufactures cannot make accurate and timely decisions on what to buy, what to make, what to move, what to stock, when to launch and when to discontinue. They are left with the reactive, fixed, inflexible solutions of the past. This leads to poor visibility, limited collaboration and—worst of all—poor decision making.
Key elements of supply chain planning
As you saw from the earlier definition, supply chain planning software needs to include a wide variety of planning puzzles in order to be able to cover the full gamut of challenges faced.
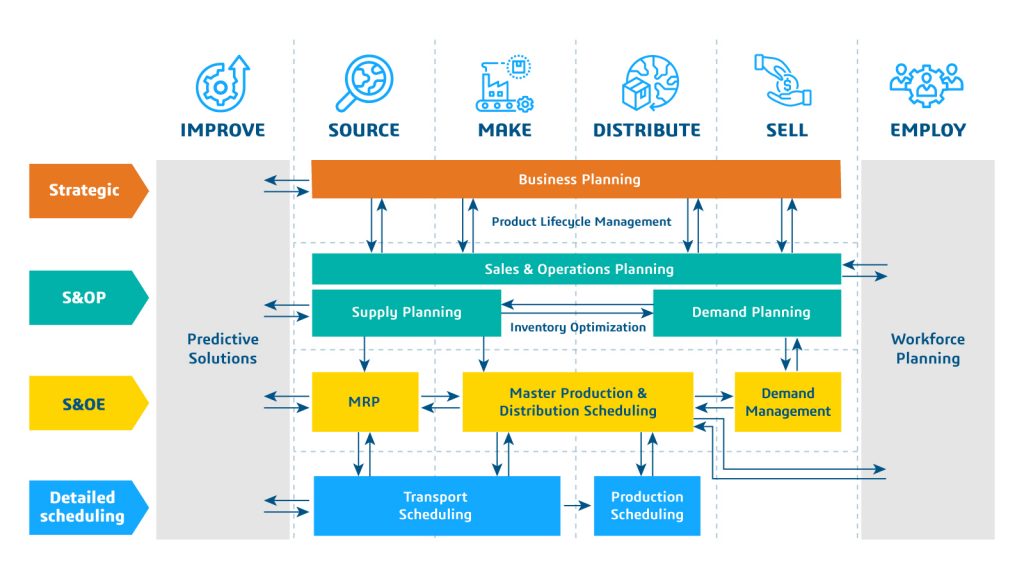
Most software solutions are only able to cover a limited number of areas, but with DELMIA all aspects are fully addressed.
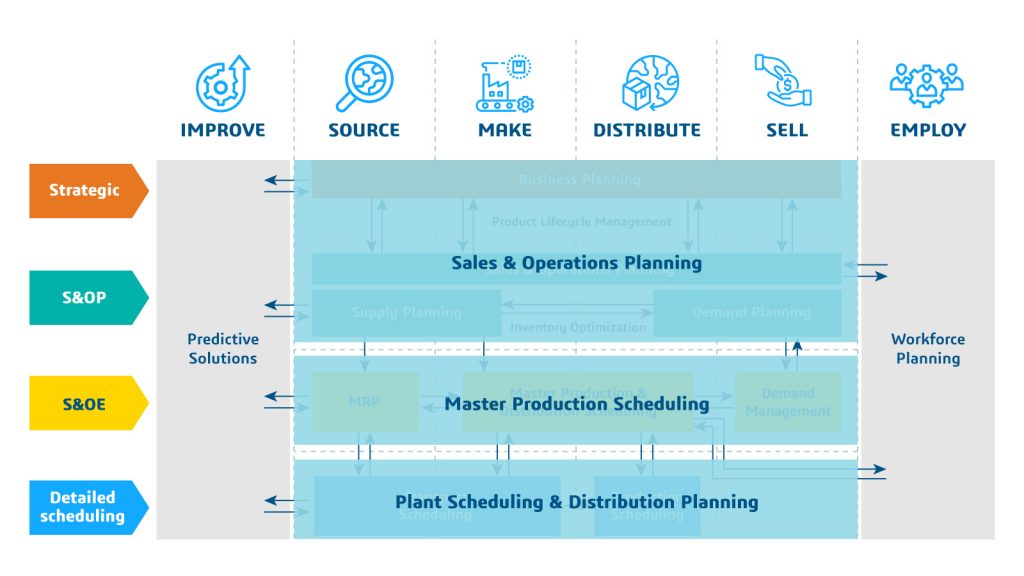
Referring back to the planning topics contained within the ASCM definition, each one is covered with a fully integrated planning suite including:
- Demand planning Often considered the gateway to improvements in supply chain planning, demand planning has the objective to better predict the demand in the market place. This includes, the impact of events, product portfolio changes, competitor activity, market intelligence, and external factors such as temperature, economic indicators and price changes. Demand planning is a highly collaborative process which combines advanced statistical forecasting techniques and machine learning with the experience and intuition of the planning team to establish and moderate the demand plan.
- Supply Planning Once we are in possession of a demand plan and/or a set of orders to be fulfilled, the role of supply planning is to determine the best way to leverage the end-to-end supply network in order to satisfy that demand. Supply planning is the strategy map for an enterprise, with all the pieces of the supply chain and their capabilities and constraints laid out for battle with the planning team as the generals who set out the strategy and objectives to be achieved. Supply planning is able to evaluate countless possible plans and identify the winning moves by evaluating all the possibilities and scoring them against the Key Performance Indicators (KPIs) of the business.
The plan with the highest score will be proposed, along with a number of alternative scenarios for consideration.
- Sales and Operations Panning (S&OP) is a process and often a planning solution. In S&OP the medium and long-term objectives of the organization are considered in conjunction with the strategic demand and supply plans as prepared in demand planning and supply planning. The S&OP process is about brining all the relevant information and experts together on a regular basis in order to identify potential issues with supply or changes in demand early. Armed with this insight, the ultimate objective is to bring this to the executive decision makers. They are typically the ones who decide and authorize the implementation of changes in the supply network so the issues identified can be mitigated long before they become a constraint to the success of the organization.
- Production Scheduling With the strategic plan assured, the dependencies between the orders, intermediates and raw materials or components are determined. The detailed steps required to produce the finished items in the most efficient way through all the necessary production operations across all the different lines, machines, processes in all the different workshops must be decided. The optimization of this plan is the intention of production scheduling. In production scheduling all the individual tasks required to manufacture each item in order to fulfill every order are planned in real time. In today’s modern, complex manufacturing environments, the sequence that operations are performed can have a profound impact on the overall equipment efficiency (OEE) of the lines. A poor sequence will often incur large amounts of setup or changeover time. They may not fit well with the availability of the workforce and can create conflicts with critical tooling availability. Production scheduling considers all these rules and constraints. It will determine the best sequence in order to perform all the manufacturing operations so delivery dates are met and the factory operates in the most efficient way.
- Integrated business planning (IBP) is in some ways the offspring of S&OP. Like S&OP, IBP is a process and also often a collection of software solutions. What differentiates IBP from S&OP is the scope of the inputs considered and the timeliness of the decision making. In S&OP the main decisions are around balancing the supply situation with the demand situation over a mid to long term strategic horizon. Decision making is generally periodic—monthly or weekly. In IBP the real-time immediate challenges within the supply chain are also included. Re-planning decisions are taken on a daily basis in order to best resolve any issues on the ground right now. In IBP the concept of real-time monitoring and control of the as-is supply chain state with control tower visualizations of all the in progress shipments, inventory positions, customer orders, transfers etc. Is combined with the short, mid and long terms plans ahead to give a complete overview of the expected supply chain performance; historically; currently and in the near, mid and long term. Give the huge amounts of data this provides, automated decision making is a critical competency in IBP with sophisticated optimization and machine learning algorithms constantly reviewing the state of the supply chain on each and every update to see if the plans will still work well of if a change is needed.
- Logistics Planning Logistics is the glue that joins our global supply networks together. Many if not all manufactures will make use of a multi modal logistics network of planes, trains & automobiles not forgetting ships of course. Which may include both their own fleet, 3rd party haulers, shipping agents, air freight booking, see freight booking, container ports and Freeports plus all the challenges and variable constraints of the road network, rail network, air network, shipping lines, port berths, takeoff and landing slots etc. Multi-Modal logistics planning solutions are designed to take all of these capabilities and constraints into consideration in a continuous time basis and work out the best way to move anything that needs to move either internally or externally. The objective is to first prepare the best plan to make this happen and then monitor and adjust those plans in real time when changes occur; for example re-routing trucks around traffic jams or switching to air fright from sea when a critical need arises.
- Workforce Planning No business can operate without its workforce and any company’s workforce is one of its greatest assets and resources. Like any other resource however, making efficient, fair and appropriate use of that asset given the continuing variations in demand and the need to supply can be a major challenge. Especially whilst enduring that all relevant labor laws are adhered to, holiday and rest days are respected, sickness is covered, training is planned for, skills are maintained, recruitment is planned and tasks are assigned in an equitable manner to those with the right skills to do it. Workforce planning is designed to plan ahead in terms of matching the workforce and skills mix required to meet the demand. Alongside looking at the day of operations to schedule and assign tasks to the right people, such that the work can be completed and as far as possible everyone is treated equally and has their preferences considered, whilst always ensuring that all the relevant working time regulations are followed.
Look for Part 2 of this blog series next week,