In our previous article, we talked about mine layout and how long-term economic viability of a block caving operation is calculated based on how much minable reserves will flow down through multiple columns of ore over time. This flow represents one of the main differences between block caving and other mining methods in terms of its influence on production.
Material flow in block cave mining introduces uncertainties that can change production outputs. Production scheduling without consideration of material mixing can jeopardize the long-term goals of the project.
Fragmented rock in the caving zone doesn’t always move down to draw points below them. The material can flow between adjacent draw columns before being extracted due to varying particle sizes and velocities. Rocks can fracture in a number of ways, and the nature of block caving and material flow mixing introduces uncertainties in key parameters such as grade and tonnage.
Fragmentation in caving operations can be divided into three categories:
- in-situ fragmentation, the natural fractures and discontinuities that exist within the rock mass.
- primary fragmentation, which occurs when the particles detach from the cave back as the undercut is created and the caving begins.
- secondary fragmentation occurs when the detached particles move within the draw columns in the caving zone.
This fragmentation and subsequent flow create uncertainties because parameters such as grade and tonnage are not fixed quantities. As a result, variability and randomness (stochastic) are injected into the process.
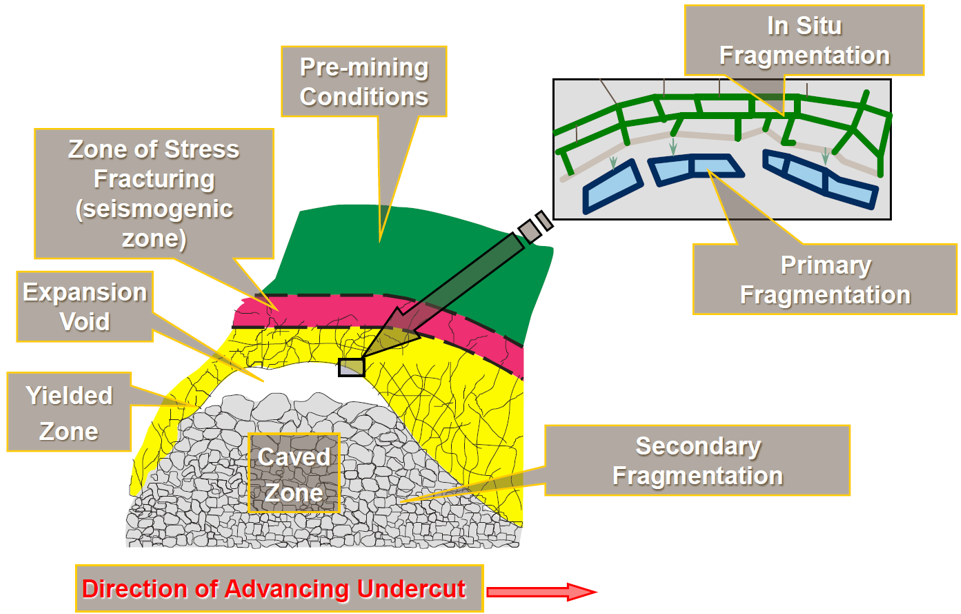
The GEOVIA User community: a community by and for GEOVIA users
Discover the community of reference for GEOVIA peer-to-peer support, materials and expert insights!
- Get started and make the most of your GEOVIA software
- Become an expert in your domain of interest
- Share your knowledge and experience
- Get help from experienced users
New member? Create an account, it’s free!
Learn more about this community HERE.