In zwei Artikeln zum 3D-Druck wurde schon gezeigt, wie die Möglichkeit, individualisierte Produkte zu fertigen, die Medizin und den Consumerbereich revolutionieren kann. Ein anderer Aspekt der additiven Fertigungsverfahren bekommt – im wahrsten Sinn des Worts – Gewicht, wenn es um den Flugzeugbau geht: Es lassen sich nahezu beliebige Formen fertigen, auch hohle Teile und Gitterstrukturen. Dies ermöglicht signifikante Gewichtseinsparungen, die wiederum den Treibstoffverbrauch und damit auch die Emissionen des Flugverkehrs senken.
Vögel besitzen hohle Knochen, die teils mit komplexen, feingliedrigen Gitterstrukturen ausgesteift sind. Schon lange versuchen Konstrukteure, diese Strukturen nachzuahmen, wie beispielsweise die Verstrebungen früher Flugzeuge zeigen. Doch nie kamen die menschlichen Strukturen auch nur ansatzweise an die Effizient der natürlichen Gebilde heran – es waren beim Weg von der Konstruktion über die Fertigung bis zum realen Bauteil einfach zu viele Kompromisse notwendig, um die Teile zu vertretbaren Kosten fertigen zu können.
Das ändert sich mit den additiven Technologien grundlegend: Erstmals ist die geometrische Komplexität des Werkstücks kein Kostentreiber mehr, der Konstrukteur ist in seiner Formgebung völlig frei und kann nach bionischen Gesichtspunkten geformte Gitterstrukturen einsetzen. Die Ergebnisse von Topologieoptimierungsalgorithmen, die früher nur ansatzweise und damit ineffizient umgesetzt werden konnten, lassen sich nun in der optimalen Form in die Realität überführen.
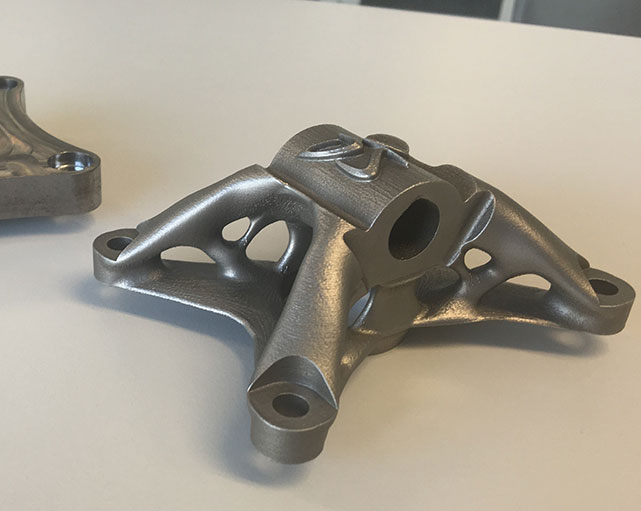
Doch auch die Möglichkeit, preiswert einzelne Bauteile herstellen zu können, spielt in der Luftfahrt, wo extrem lange Lebenszyklen üblich sind, eine wichtige Rolle. Ein gutes Beispiel findet sich in einem Video von Airbus zum Thema 3D-Druck: Das Unternehmen benötigt pro Jahr 50 bis 100 Stück einer Sitzabdeckung, deren ursprünglicher Hersteller längst nicht mehr verfügbar ist. Mit Hilfe von 3D-Druck lassen sich diese Teile herstellen, ohne dass eine teure Spritzgussform gefertigt werden muss.
Gravierender ist jedoch der Spareffekt durch leichtere, an den aktuellen Zweck optimal angepasste Bauteile. Eines der bekanntesten Beispiele sind Einspritzdüsen für die neuen Triebwerke, die ab 2018 unter anderem im A320neo eingesetzt werden. CFM International, ein Joint Venture zwischen GE Aviation und Safran, ersetzt eine aus 20 Teilen zusammengesetzte Einspritzdüse durch ein einziges 3D-gefertigtes Bauteil. Das Geheimnis dabei ist die hochkomplexe interne Gestaltung, die für eine optimale Spritvernebelung sorgt. Diese konnte mit herkömmlichen Verfahren nur „scheibchenweise“ hergestellt werden, was die vielen Einzelteile und teilweise unterschiedliche Lieferanten bedeutete. Ein weiterer Clou ist, dass das gedruckte Teil auch fünfmal stärker ist als herkömmlich hergestellte Einspritzdüsen.
Die neue Einspritzdüse, von der 19 Stück in einem LEAP-Triebwerk sitzen, ist 25 Prozent leichter und so sorgt das LEAP-Triebwerk für einen um etwa 15 Prozent niedrigeren Treibstoffverbrauch der Turbine – zudem sinken CO2– und Lärmausstoß. GE will ab dem Jahr 2019 pro Jahr 40.000 dieser Düsen herstellen – hier geht es nicht mehr um Prototypen und Kleinserien, sondern um Großserie. Der 3D-Druck spielt in diesem Szenario seine freie Gestaltungsmöglichkeit aus.
In diesem Bereich werden wir noch viele Innovationen sehen – auf der einen Seite bei den Anbietern der AM-Maschinen, die beispielsweise eine kontinuierliche Prozessüberwachung implementieren, auf der anderen Seite bei den Flugzeugherstellern, die die Vorteile des AM immer besser zu nutzen wissen und damit immer größere Vorteile daraus ziehen.
Auch hier nochmals der Verweis auf das Bitkom-Positionspapier 3D-Druck mit weiteren Einblicken und Empfehlungen rund um den 3D-Druck.