Willkommen zu Tag 2 der Liveberichterstattung vom 3DEXPERIENCE Forum EuroCentral in Leipzig. Nach einem anregenden Abend, mit dem der Event gestern startete, geht es heute “in medias res”. Der Tag ist von 9:00 bis 17:00 Uhr vollgepackt mit interessanten Keynotes, Workshops und Sessions, die das Motto der Veranstaltung “Experience the Future of Industrial Design, Engineering and Production” in die Realität übersetzen.
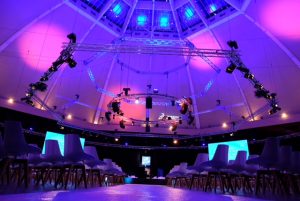
9:00: Gleich geht es los in einer der ungewöhnlichsten Umgebungen, die ich je gesehen habe: Genau unter der Kuppel des Kohlrabizirkus ist eine runde Bühne aufgebaut, um die herum Stuhlreihen angeordnet sind. An den Stoffwänden des runden Saals wurden vier weitere Bühnen aufgebaut, die aktuell als Videowände dienen, aber später noch eine wichtige Rolle spielen werden.
9:15: Andreas Barth eröffnet die Veranstaltung. Es geht los mit Keynotes von Kunden, die schon heute Themen wie Industrie 4.0 oder Additive Manufacturing umgesetzt haben. Smart Citys, Generative Design und andere Zukunftsthemen werden in einem Block “Science & Simulation” behandelt. Aber auch handfeste Themen wie Change Management und Produktion werden behandelt.
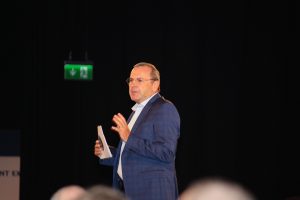
Barth präsentiert Zahlen aus dem Bereich Zentraleuropa: 1.700 Mitarbeiter in 30 Niederlassungen erwirtschafteten über 43 Prozent des Umsatzes von Dassault Systèmes. 20 Prozent der Mitarbeiter sind in Forschung und Entwicklung beschäftigt.
Kreisel Electric nutzt die 3DEXPERIENCE Plattform, Barth sagt: “Dort sendet man keine E-Mails mehr, die gesamte Kommunikation läuft über die Plattform.” Das Unternehmen hat seine Elektomobilitätslösung in die verschiedensten Fahrzeuge eingebaut, um zu zeigen, wie flexibel diese ist: Vom VW Bully Typ 1 bis zu einem Rennwagen von 1971.
Neue IDC-Studie: Die Zahl der Firmen, die sich mit Industrie 4.0 beschäftigen, ist vom letzten Jahr zu heute von 53 auf 86 Prozent gewachsen. 90 Prozent der Firmen geben an, dass sie zu viel Zeit in der Koordination zwischen den Abteilungen verlieren. Das Thema Cloud wird immer relevanter für die Unternehmen. Cloud ist nicht die Lösung für alle Probleme, aber ein guter Weg, schnell mit PLM zu starten und optimal als Implementierung für bestimmte Unternehmen.
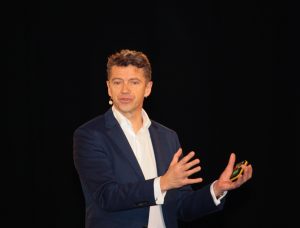
9:30: Laurent Blanchard, Executive Vice President, Globale Operationen (EMEAR), globale Allianz und Services, erläutert die Prinzipien von Dassault Systèmes und den Weg von 3D CAD über 3D DMU zu 3D PLM, der schließlch zur 3DEXPERIENCE Plattform führte.
Innovation ist ein Kern der Dassault-Lösung, Milliarden von Innovationsinvestments werden auf der 3DEXPERIENCE Plattform in reale Produkte umgesetzt.
Agilität: 30 Prozent der Arbeitszeit wird mit Suchen verbracht – welch ein Potential, Zeit für Innovationen freizuschaufeln.
Sehr wenige Firmen haben Zugang zu Datenanalyse. Blanchards Beispie für Agilität ist Ericsson, die von einer hardwarebasierten zu einer Softwarefirma werden mussten. Auf Basis der Dassault Systèmes-Plattform wurden unter anderem Social Media-Funktionen für die interne Kommunikation implementiert.
Return on Investment: Ein Industrial Equipment-Anbieter erwirtschaftet 60 Prozent seines Umsatzes mit Wartung und Services. Der digitale Zwilling kann hier große Verbesserungen bringen, weil sich Wartungseinsätze besser planen und damit verkürzen lassen.
Die 3DEXPERIENCE Plattform ist ein Betriebssystem für das Softwareportfolio des Unternehmens, ebenso wie ein Geschäftsmodell – als Plattform für den Marketplace, auf dem Dassault Systèmes Menschen zusammenbringt, die sich ihre Fähigkeiten gegenseitig zur Verfügung stellen. Als Beispiel dient der 3D Printing Marketplace, auf dem 3D-Druckerbesitzer ihre Dienste anbieten können.
Daten aus allen Quellen – Dassault-eigenen und fremden – lassen sich auf der Plattform zusammenführen – Voraussetzung für moderne Unternehmensprozesse.
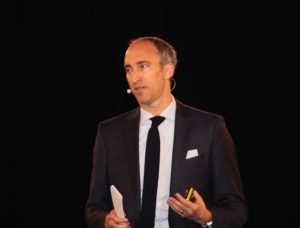
10:05: Luz G. Mauch, Senior Vice President Automotive bei T-Systems International: 2012 gab es erstmals mehr internetfähige Devices als Menschen auf der Welt – ein “tipping point” für die Digitalisierung. Die Ausgaben im IoT-Bereich sind riesig – aber ein großer Teil dieser Ausgaben passiert außerhalb Europas: Bis 2020 sollen in Europa 43 Mill. Eurio in IoT ausgegeben werden, weltweit sind es 442 Mill.
Die Telekom betrieb 2006 6 Mio. Telefonzellen, heute sind es unter 20.000. Die Telekom verdient aktuell mehr Geld mit dem Verkauf ausgemusterter Telefonzellen als mit den Gesprächen, die in den verbliebenen Zellen geführt werden. Die Zahl der SMS-Nachrichten sinkt, WhatsApp vervielfachte die Anzahl der Messages mehrmals – die Digitalisierungswelle rollt schon heute.
Die europäischen Telco-Companies verlieren pro Tag 100 Mio. Dollar an die digitalen Unternehmen aus Asien und den USA. Der Druck, dies Unternehmen zu verändern, ist also riesig. OTC ist die Open Telekom Cloud, betrieben im größten Rechenzentrum Europas.
Das Ziel der Telekom ist es, IoT-Provider zu werden. Schon heute arbeiten Firmen von Startups bis zu Riesen wie Microsoft oder SAP auf der Plattform. 1.400 Mitarbeiter alleine für Security-Lösungen, unter anderem mit der Suche nach Schwachstellen in den Computersystemen in Autos für die Hersteller.
Die Telekom investiert jährlich 30 Mio. Euro in die Netze, der Return-on-Investment dauert typischerweise über 10 Jahre.
Mit seiner ersten Plattform für Connected Cars scheiterte das Unternehmen, jetzt wird ein neuer Anlauf genommen, dieses Mal in einem Ecosystem von Partnern, die Mehrwert schaffen. Hier werden unter anderem die Daten gesammelt, die die Automobilhersteller bei ihren Tests autonomer Fahrzeuge erzeugen, um diese zu dokumentieren – das sind Terabytes pro Tag.
Mauch verkündet die brandneue Partnerschaft der Telekom mit Dassault Systèmes im Bereich Security, Open Stack und Cloud auf Basis der 3DEXPERIENCE. Zitat aus der Pressemitteilung:
Dassault Systèmes wird mit dieser Partnerschaft seinen deutschen Kunden die Open Telekom Cloud als Infrastruktur zur Nutzung der 3DEXPERIENCE Plattform anbieten können. Heute schon beziehen 56 Prozent von 100 befragten Industrieunternehmen in Deutschland PLM-Dienste als Cloud-Services, wie eine auf dem 3DEXPERIENCE Forum in Leipzig veröffentlichte Studie von International Data Corporation (IDC) ergab. Die Umfrage ergab weiterhin, dass 83 Prozent der Befragten eine Datenspeicherung in Deutschland als wichtig ansehen. Dies unterstreicht die Wichtigkeit der Partnerschaft zwischen Dassault Systèmes und Deutsche Telekom, dem führenden deutschen Cloud-Anbieter.
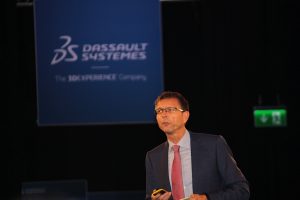
11:30: Nach der Kaffeepause spricht Kurt Bengel, CEO der Cenit AG. Er spricht über “smartPLM: Strategic Pillar for Digital Transformation in Engineering”. IT folgt der Unternehmensstrategie und umgekehrt. Digitalisierungsinitiativen sollen Effizienz steigern und neue Geschäftsmodelle ermöglichen. Gutes Beispiel: Ein Landmascinenhersteller will autonome Fahrzeuge anbieten – für den Transport in automatisierten Produktionsumgebungen und alas Service. Die Umwälzungen, die eine solche Fokuserweiterung für das Unternehmen und seine Prozesse bedeutet, ist nicht zu unterschätzen.
Langjährige Erfahrung und vorkonfigurierte Lösungen auf Basis der 3DEXPERIENCE Plattform sind das Erfolgsrezept, mit dem Cenit seine Kunden bei der Digitalisierung unterstützt. Unterschiedliche Produktstrukturen für unterschiedliche Abteilungen und deren Anforderungen lassen sich auf einer Plattform umsetzen. Bengels Key Messages: Think Big – Start small – Start now!
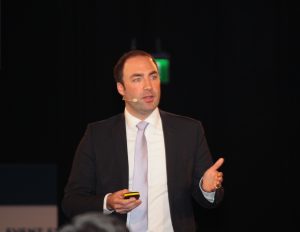
Vice Director Production und Head of Industrial Engineering bei der imperial-Werke oHG
11:55: Rouven Vierfuss ist Vice Director Production und Head of Industrial Engineering bei der imperial-Werke oHGin Bünde. Das Unternehmen ist Teil der Miele Group. Sein Thema: Digitalisierung in der Produktion. Hier wurde aus einem Forschungsprojekt eine Implementierungsstrategie entwickelt. In Bünde, dem Kompetenzzentrum u.a. für Dampföfen und Kochfelder, arbeiten 600 Mitarbeiter.
Aufgrund der vielen Varianten – alleine im Bereich Dampföfen werden über 700 Varianten gebaut – arbeitet imperial mit einem speziellen Produktionssystem, das 2010 eingeführt wurde. Gleichzeitig wurde von Fließbandarbeit auf eine Produktion umgestellt, in der ein Werker ein Gerät komplett montiert.
2013 wurde mit Unterstützung des Bundesforschungsministeriums ein Projekt namens “Smart Factory IT” gestartet. Ziel war es, multiadaptive cyberphysikalishe Produktionssysteme zu entwerfen. Es wurden in Zusammenarbeit mit den Werkern drei Use Cases definiert und in IT-Systeme überführt. Ein großes Problem für die Werker waren die vielen Medienbrüche in ihrer Arbeit. Es wurden drei Apps entwickelt für Vorarbeiter, Montagearbeiter und Reparaturen.
Die Apps erleichtern die Kommunikation und zeigen dem Werker jeden Montgeschritt an. Der Vorarbeiter kann mit seiner App den Produktionsfortschritt kontrollieren und bestimmte Geräte lokalisieren.
Die Reparaturabteilung sucht und beseitigt Fehler, die in der Montage gemacht wurden. Mit dieser App kann erstmals eine Rückmeldung über Montagefehler gegeben werden. Der Werker, der den Fehler gemacht hat, wird anonym infornmiert und beim nächsten Montagevorgang expliozit darauf hingewiesen, dass er beispielsweise ein Kabel nicht richtig eingesteckt hat.
Erste Implementierung auf dem Shopfloor war Pick-by-light, eine Unterstützung für die Werker, die mit Lichtsignalen anzeigt, welches Bauteil als nächstes montiert werden soll.
In den aus dem Projekt gewonnenen Ergebnissen wird nun eine Strategie namens “Production 2025” entwickelt. Die Digital Continuity wird über die 3DEXPERIENCE sichergestellt, Dassault Systèmes steuert das Produkt- und Prozessengineering bei, so kann Miele externes Know-how nutzen.
14:05: Nun zeigt sich der Clou des Saals: Die Stühle sind nicht mehr auf ie Bühne in der Mitte gerichtet, sondern zu den vier Bühnen am Rand. Mittels Kopfhörer kann man sich in eine der Sessions einklinken – es laufen also vier Sessions gleichzeitig in einem Raum. Das gibt mir die Möglichkeit, mehrere Vorträge gleichzeitig anzuhören. Los geht es mit dem Vortrag von thyssenkrupp zum Thema “Mastering the Complexity – Supply Chain Management” und “Systems Engineering and Simulation” von MAN Diesel & Turbo.
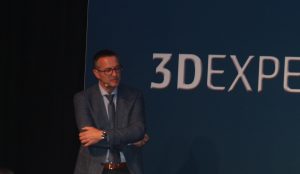
thyssenkrupp bietet seinen Kunden eine riesige Variantenvielfalt. die zudem aus vielen verschiedenen Werken in Deutschland und Europa kommen können. Die Organisation der Lieferkette innerhalb des Unternehmens ist also sehr komplex. Aus dem SAP-System kommen die Aufträge in den Quinti Company Planner, der von der gleichnamigen Dassault-Tochter stammt. Hier wird entschieden, in welchem Werk und auf welcher Produktionslinie der Auftrag gefertigt werden. Über einen Scheduler, der ebenfalls von QuintiQ kommt, werden die Aufträge jeder Produktionslinie organisiert und an die eigene Leitung der Produktionslinie übergeben. In der anderen Richtung laufen die Informationen über die freien und belegten Kapazitäten – recht komplex also.
Wolfgang Meißner von thyssenkrupp erläutert, wie er mit Hilfe von Studenten, deren Blick nicht vom Wissen über den aktuellen Stand getrübt ist, die Chancen der Nutzung von Industrie 4.0 erarbeitete. Die Nutzung von Big Data ist ein Weg, etwas mehr Voraussicht in die Planung zu bekommen, indem man aus der Vergangenheit eine typische Auftragsfolge erkennnnt.
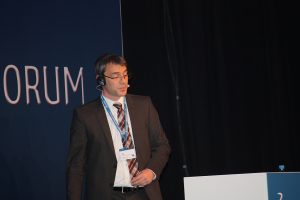
Peter Böhm von MAN Diesel & Turbo hat ein ähnliches Thema: Die Großmotoren von MAN sind extrem kundenspezifisch, oft werden Features einer Baureihe in anderen Baureihen verlangt. Hinzu kommt die Größenspreizung, beispielsweise werden über zehn Meter lange Kurbelwellen modelliert mit Radien von unter einem Millimeter Radius.
Simulation und Systems Engineering sind dabei wertvolle Hilfsmittel, um die extrem hohen Anforderungen der Kunden an Wirtschaftlichkeit und Zuverlässigkeit stellen. “Für uns ist die Simulation das einzige Mittel, unsere Motoren zu untersuchen. Wir können nicht einfach mal einen Prototypen bauen.” Dazu werden kreative, ja sogar künstlerisch angehauchte Entwickler gebraucht.
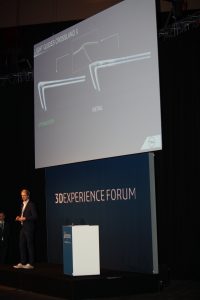
14:45: Die Sessions wechseln, ich begleite Dr. Kai Korthals von Claas bei seinem Vortrag “Von der Digitalisierung des Engineering zu Systems Engineering” und Philipp Röckl von Opel, der zum Thema Beleuchtungssimulation spricht.
Bei Autos sind die Front- und Heckleuchten heute nicht nur Beleuchtung, sondern Stilelemente und sogar Markenzeichen wie die flügelförmigen Tagfahrleuchten vorn und hinten bei Opel. Philipp Röckl zeigt, wie detailliert die Lichtsimulation ausgeführt wird – hier wird sogar die Glühwendel des Leuchtmittels modelliert. Die Form des Lichtstroms beispielsweise eines Scheinwerfers ist gegeben, ebenso die Form des Scheinwerfers aus dem Styling. Aufgabe der Simulation ist nun, den Reflektor so zu gestalten, dass die Beleuchtung den technischen und regulatorischen Anforderungen entspricht.
Zur Visualisierung ist eine Berechnung auf Basis realistische Physik notwendig, zudem benutzt man gemessene Materialdaten, um eine völlig realistische Visualisierung der Beleuchtung zu erreichen. Die Zukunft sind hochauflösende Lichtsysteme, die beliebige Formen projizieren können.
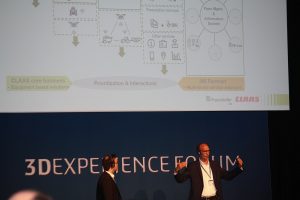
Bei Claas geht es um Smart Farming – der Landwirt der Zukunft arbeitet mit intelligenten Maschinen. Trotzdem muss eine Plattform, auf der deren Daten zusammenlaufen, auch ältere, “dumme” Geräte berücksichtigen und einbinden können. Smart Farming erfordert, wie Dr. Korthals ausführt, smart Engineering. Das klassische V-Modell hilft hier jedoch wenig weiter, wie sein “Mitsprecher” Dr. Christian Tschirner vom Fraunhofer IEM zeigte. RFLP ist ein besser geeigneter Ansatz, um auch komplexe Modelle abzubilden wie einen Traktor mit einem Ladeanhänger, der Heu aufnimmt. Mit Hilfe der 3DEXPERIENCE wurde in einem Pilotprojekt ein Modell Based Systems Engineering-Prototyp aufgebaut, der nun ausgebaut wird bis in die Fertigung und in den Service. Statt des V-Modells ist man nun beim “Multi-V-Modell” angelangt.
Interessanterweise arbeitet man auch bei Claas an ungewöhnlichen Arbeitsmodellen, in diesem Fall einem Co-Working-Space namens Greenhouse. Tschirner: “Die Basis jedes erfolgreichen Softwareprojekts ist Kommunikation und ein offener Geist.” Eines der nächsten Projekte ist ein Gaming-basiertes System.
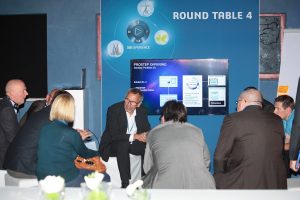
In den Bereichen rund um den zentralen Saal finden parallel Workshops statt, in denen in kleiner Runde über die verschiedensten Themen diskutiert wurde, vom generativen Design über Smart City und BIM bis hin zu firmenübergreifender Collaboration. Hier ist eine ganze Reihe von Partnern beteiligt, unter anderem Technia Transcat, PROSTEP, Sogeti, Microsoft, Cenit und em: engineering methods. Die Diskussionen, die ich kurz besucht habe, waren außerordentlich lebhaft und tiefschürfend.
Auch in den Pausen ging die Informationsvermittlung nahtlos weiter. An den Infopoints rund um den zentralen Saal stellten verschiedene Dassault Systèmes-Bereiche und die anwendesenden Partner ihre Lösungen vor. Unter anderem konnten Anwendungen mit VR- und AR-Brillen ausprobiert werden.
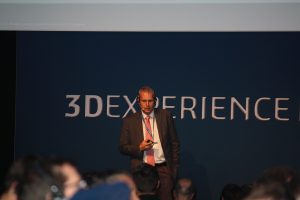
16:00: Die finale Sessionrunde bietet unter anderem den Vortrag “Industry 4.0 above the clouds” von Airbus – hier ist mit Cloud ausnahmsweise die reale Wolkendecke am Himmel gemeint, in dem sich die Airbus-Produkte bewegen. Vice President Research & Technology Jens Gralfs erläutert, dass alle 1,5 Sekunden irgendwo auf der Welt ein Airbus startet oder landet. Ein Langstreckenflogzeug ist 6.500 der 8.760 Stunden eines Jahres in der Luft – und das bei einer Lebensdauer von 30 und mehr Jahren. Das zeigt, wie hoch die Qualität eines Flugzeugs sein muss.
Airbus wird 2019 alle fünf Stunden ein neues Flugzeug fertigstellen. ” Für eine solche Massenfertigung waren Flugzeuge nie gedacht, wir müssen also alle Baugruppen an diese neuen Gegebenheiten anpassen.” Immer mehr Flugzeuge auch der kleineren Baureihen sind in der Lage, den Atlantik zu überqueren, was das Kabinenlayout komplexer macht.
Bisher erfordern Flugzeuge sehr viel Handarbeit und komplexe, riesige Hellinge und Betriebsmittel. Im Autobereich wird genau andersherum gemacht: Die Karosserien werden für die Fertigung in der Schweißstraße hin entwickelt, bei der Flugzeugentwicklung wird bisher auf die Fertigung kaum Rücksicht genommen. Parallel zum Bau des Flugzeugs wird sehr viel getestet, was ebenfalls die Produktion verlangsamt.
Interessante Gedanken: “In Sachen Cybersecurity ist es eine positive Tatsache, dass wir 3.000 Softwarewerkzeuge einsetzen, die mangelhaft vernetzt sind. Je stärker wir alle Daten auf eine Plattform bringen, desto mehr Gedanken müssen wir uns über Datensicherheit und -integrität machen.” “Unser Problem heute ist nicht der Mangel an Daten, sondern was machen wir mit den Daten und wie verteilen wir sie an die richtigen Stellen?”
Airbus hat ein Scan-System entwickelt, das die 32 Schließzapfen einer Flugzeugtür und die Aufnahmen im Rahmen scannt und mittels künstlicher Intelligenz die optimale Justierung berechnet. Dies erleichtert und verkürzt einen heute noch sehr aufwändigen Arbeitsgang.
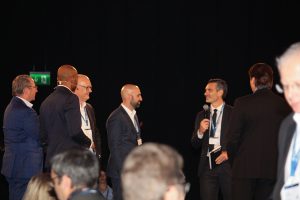
16:30: Das Wrapup beginnt mit Andreas Barth und seinen Kollegen, die sich bei allen Sprechern, Moderatoren und den Teilnehmern bedanken. Eine Live-Umfrage zeigt, dass dei meisten Besucher hier sind, um Kontakte zu knüpfen, aber auch um Neues und mehr über die Vorteile der Dassault Systèmes-Lösung zu erfahren. Fast 80 Prozent der Besucher wollen sicher oder sehr sicher beim nächsten Forum wieder dabei sein – das spricht sehr für die Veranstaltung und das Programm. Von meiner Seite kann ich sagen, dass ich sehr viele Informationen mitgenommen habe. Wir sehen uns im nächsten Jahr!