Hallo zurück zum zweiten Tag der Dassault Systèmes User Conference, zu der sich 500 Anwender von CATIA, SIMULIA und anderer Lösungen im Congress Park Hanau versammelt haben. Frisch erholt nach einer schönen Abendveranstaltung mit weihnachtlichen Anklängen geht es direkt hineinntin die Parallelsessions. Wie schon gestern berichte ich live vom Event.
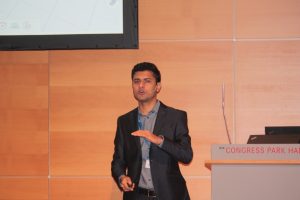
9:00, Brüder-Grimm-Saal B: Der Saal ist gut gefüllt für den Vortrag von Ronan Keswani von Dassault Systèmes, der über “3D Automated Engineering” spricht. Er zeigt, wie sich beispielsweise Ventile eines Atomotors automatisiert in den Zylinderkopf einsetzen lassen. Eine ingenieursfreundliche Skriptsprache ermöglicht es, 96 Bauteile mit einem Knopfdruck einzubauen – das lohnt sich bei der ersten Änderung.
Es ist möglich, in CATIA komplette Apps zu bauen, Keswani zeigt ein Beispiel, das mit Hilfe weniger Usereingaben eine 3D-gedruckte Drohne erstellt. Neben dem typischen, fixen Regelwerk eines Konfigurators – wenn der Anwender Propeller A aussucht, muss Batterie B verbaut werden – bietet die App auch ein Dashboard von Werten, bei denen es kein “Schwarz-Weiß” geben. Die App zeigt hier an, zu wieviel Prozent eine Bedingung erfüllt ist, beispielsweise wie nah das Massenzentrum an der geografischen Mitte liegt – je näher, desto besser sind die Flugeigenschaften.
Die dritte Möglichkeit zur automatisierten Geometrieerstellung ist die Mustererstellungsfunktion in der neuen Rolle der 3DEXPERIENCE Plattform xGenerative Design. Beim Erstellen einer Geometrie in diesem Tool werden automatisch Parameter und Gesetzmäßigkeiten des Musters definiert, die nachträglich geändert und erweitert werden können.
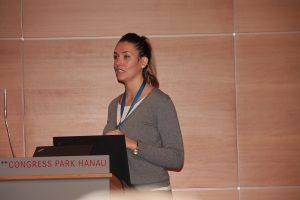
9:30: Federica Giuliani von Digital Orthopaedics spricht darüber, wie sich für medizinische Anwendungen anatomische 3D-Modelle automatisiert aus den CT-Scans des Patienten erstellen lassen. Interessant dabei: Das CT zeigt lediglich die Knochen, die Knorpel, Sehnen und Bänder werden rein auf Basis des in Flächenmodelle umgewandelten STL-Modells der Knochen aus dem Scan generiert.
Der manuelle Aufbau eines Fußmodells dauerte bis zu drei Wochen, nun dauert der Vorgang noch wenige Stunden. Mit CATIA lassen sich sogar Bänder definieren, die sich um einen dazwischenliegenden Knochen schmiegen. Die Bänder sind grundsätzlich vordefiniert und lassen sich durch Anwählen weniger Punkte im Modell erstellen. Die manuelle Arbeit beschränkt sich auf das Erstellen dieser Anbindungspunkte durch einen Arzt, doch auch dieser Prozess soll automatisiert werden, wie Giuliani auf Nachfrage berichtete.
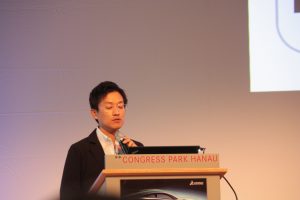
9:50, Brüder-Grimm-Saal A: Statt des erwarteten Vortrags von Geberit gerate ich in den Vortrag von Taiki Furuki von Kubota, den wir schon beim gestrigen Design-Roundtable kennenlernten. Der japanische Landmaschinenhersteller hat schon in den frühen 90er Jahren in der Designabteilung mit 3D-CAD gearbeitet, allerdings eher schlecht als recht. Nach einer Zwischenphase mit Designsoftware eines anderen Herstellers arbeiten die Designer heute gemeinsam mit den Konstrukteuren auf der 3DEXPERIENCE Plattform.
Die Designer arbeiten mit AR/VR sowie mit Mixed Reality, in der der Designer seine eigenen Hände in der virtuellen Fahrerkabine sehen kann, beispielsweise für Einbauuntersuchungen.
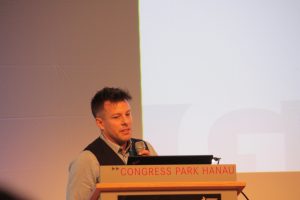
10:10: Nun doch noch der Vortrag von Thilo Cramer von Geberit, der über den “Rollout der 3DEXPERIENCE und von CATIA im Geberit Design Studio” spricht. “Ich weiß nicht, ob Sie Geberit kennen, aber ich bin sicher, dass Sie unsere Produkte heute morgen benutzt haben, führt Cramer den Schweizer Sanitärspezialisten ein.
Geberit nutzt CATIA V5 und die 3DEXPERIENCE Plattformen in allen Bereichen des Unternehmens von der Gebäude- und Fertigungsplanung über die verschiedenen Produktkategorien bis hin zu den vor wenigen Jahren zugekauften Sanitärkeramikdesignern, die derzeit ein anderes 3D-CAD-System ablösen.
Die Einführung der 3DEXPERIENCE startete 2016, wobei es vor allem in den ersten beiden Jahren eine Reihe von Problemen sowohl auf Dassault- wie auch auf Geberit-Seite kam. Inzwischen haben sich die beiden Partner aufeinander eingestellt und die Transition läuft so reibungslos wie solch ein Prozess möglich ist. 2020 soll der Umstieg auf die Plattform abgeschlossen sein.
Der Widerstand im Design Department gegen die Einführung von CATIA V5 endete mit einer bemerkenswert guten Demonstration der Designwerkzeuge in der 3DEXPERIENCE mit Imagine & Shape und Natural Sketch. Die Designer konnten beim ersten Workshop Wasserhähne designen, die heute genau in dieser Form produziert werden.
11:10, Paul-Hindemith-Saal: Es geht weiter mit dem Medizintrack im großen Saal, Denis Feindt von Synopsys spricht über die Erstellung qualitativ hochwertiger CAE-Modelle aus 3D-Bilddaten. Er zeigt, dass die Verarbeitung der Ergebnisse bildgebender Verfahren nicht nur in der Medizin, sondern auch im Maschinenbau interessant ist, beispielsweise im Reverse Engineering oder der Qualitätssicherung. Synopsys bietet dafür die Software Simpleware. Simpleware bietet auch Modelle menschlicher Körper, die nicht personalisiert, sondern auf Basis statistischer Daten erstellt wurden. So kann ein Forscher an einem Modell des typischen 60-jährigen Europäers forschen.
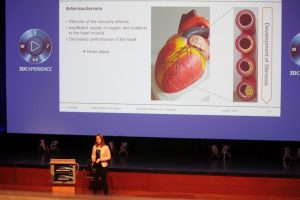
Im CT-Scan entstehen Schichtbilder, deren Elemente als Schnitte genutzt werden, um daraus je nach Abstand der Schichten teils extrem detaillierte 3D-Modelle zu erstellen. Diese werden unter anderem benutzt, um Prothesen und Implantate anzupassen – Feindt zeigte ein Bild eines Unterkiefer-Teilimplantats, das einem Patienteneingesetzt wurde. Das 3D-gedruckte Teil konnte im Kontext des 3D-Modells des verbliebenen Unterkiefers und des Schädels individuell angepasst werden, bevor es 3D-gedruckt und implantiert wurde.
11:35: Lisa Wiesent von der OTH Regensburg berichtet über die numerische Analyse von Stents mit Abaqus. Stents verformen sich beim Einsetzen – in dessen Verlauf sie mit einem Ballonkatheder auf den Durchmesser der Ader aufgebogen werden – oft so, dass die Ränder beim Ausdehnen zuerst an die Aderwand anliegen und diese dabei verletzen. So kann sich an der Stelle des Stents – der ja eine Verengung einer Herzarterie beseitigen soll – wieder eine Wucherung bilden. Ziel von Wiesents Forschung ist es, den Stent so aufzuweiten, dass er sich parallel oder mit nach innen gebogenen Kanten öffnet.
Es ist beeindruckend, wie detailliert Wiesent das Falten des Ballons und das Aufbringen des Stents auf den Ballon simulieren konnte. Die gefalteten Positionen und auch das Aufblasen wurde mit Schnitten durch reale Stents verglichen und mit einer Hochgeschwindigkeitskamera gefilmt – die Abweichung zwischen Simulation und Realität lag unter einem Prozent!
Wiesent konnte durch steifere Enden des Stents ein besseres Aufweitungsverhalten erreichen, was einen großen Fortschritt in der Stentforschung bedeuten würde. Chapeau!
12:00 Uhr: Mittagspause und eine Gelegenheit, etwas durch die Ausstellung zu streifen. Eine ganze Reihe von Partnern zeigt Lösungen rund um die Dassault Systèmes-Produktfamilie, Cenit ist beispielsweise mit Generative Design dabei, weitere Aussteller im Foyer sind unter anderem Technia Transcat, Schwindt und Wacom mit seinen beeindruckenden Tablets. 3DConnexion ist mit den Space-Mäusen vertreten und auch CT Core Technologie, :em Engineering Methods, Desys und andere zeigen Flagge auf der User Conference.
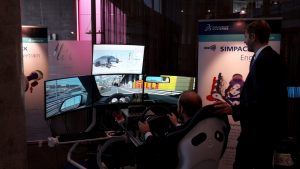
Dassault Systèmes selbst ist mit seinem 3DEXPERIENCE Playground vertreten, herausragend ist ein Stand, an dem gemeinsame VR-Konferenzen gezeigt werden. Vor Ort zwei, insgesamt bis zu vier Personen können sich in der virtuellen Realität treffen und, ausgerüstet mit VR-Brillen, beispielsweise einen Prototypen betrachten und miteinander kommunizieren.
Daneben ist ein Fahrsimulator aufgebaut, in dem man die Formel-Eins-Rennstrecke von Monaco nachfahren kann. Das Besondere: Das Verhalten des Fahrzeugs wird in Echtzeit über Simpack berechnet und gesteuert. So lässt sich beispielsweise per Knopfdruck ein platter Reifen simulieren.
Die Stände sind gut besucht, die Besucher zeigen großes Interesse an den gezeigten Lösungen.
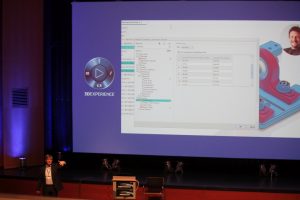
13:30, Paul-Hindemith-Saal: Ich habe mich für den Materials-Track entschieden. Andrew Reilly von Granta Design findet drastische Worte, um seine langjährige Verbindung mit Dassault Systèmes’ CAD-System darzustellen: “If you cut away my arm, you can probably read CATIA o the inside.” Während der CAD-Anwender sich an einem Material nur für den Namen und vielleicht noch die Dichte interessiert, brauchen die “Simulanten” wesentlich umfangreichere Daten, bis hin zum Verhalten bei unterschiedlichen Temperaturen.
Granta Design liefert eine Datenbankanwendung namens MI mit diesen Daten. Eigene Daten werden mit Materialeigenschaften aus Standard-Materialdatenbanken ergänzt. Ermüdungstestdaten werden bei neuen Materialien erst nach Jahren bekannt – weil die Tests eben so lange dauern. Die Granta-MI-Datenbank hat eine Schnittstelle zur 3DEXPERIENCE, wobei sich eine Materials Authority zwischenschalten lässt, die entscheidet, welche Materialwerte aus Granta in die Plattform synchronisiert wird.
Aktuell konzentriert sich MI auf die Simulation-Rollen der Plattform, in der Zukunft soll ein Dashboard-Widget zum Durchsuchen der Granta-Datenbank entstehen.
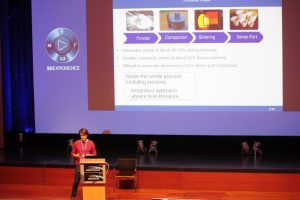
13:55: “Thermomechanische Modellierung der Pulververdichtung und Keramisches Sintern” mit Daniel Kempen, der diese Arbeit an der Universität Trento erarbeitet hat, inzwischen aber schon bei Dassault Systèmes arbeitet. Er kümmert sich um den Press- und Sinterprozess von Keramikprodukten, vor allem um den großen Schrumpfprozess bei diesem Vorgang, der bisher vor allem im “Trial&Error”-Verfahren angenähert wurde. Das bedeutet, dass die Rohform, die wesentlich größer ist als das Endprodukt, so lange geändert und gesintert wird, bis die Endform erreicht ist.
Kempen will nun mit Hilfe der Simulation die Schrumpfung möglichst genau vorhersagen. Das Problem ist, dass aufgrund der extremen Härte des Keramikmaterials keine sauberen Materialkenndaten erhoben werden konnten, Kempen musste ein eigenes Mikromodell des Materialverhaltens entwickeln, das wesentlich genauer wurde als die bisher verfügbaren Werte. In Abaqus als User-defined Function implementiert, können nun die Spannungen berechnet werden, die aufgrund der Schrumpfung entstehen. So lassen sich viele Experimente einsparen, weil die richtige Form schneller gefunden wird – allerdings muss dafür noch der Weg zurück vom fertigen Teil zum Rohling erforscht werden.
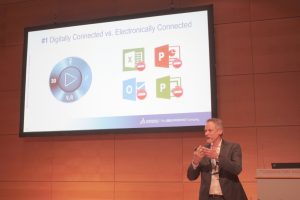
15:50, Brüder-Grimm-Saal B: Endspurt, ich sitze im Track “Collaboration and Information Intelligence”. Tom-David Graupner von Dassault Systèmes spricht über “Closing the Loop fron Virtual to Real and back with 3DEXPERIENCE Twins.” Bisher wird oft versucht, die Silos, in denen die Daten der verschiedenen Abteilungen eines Unternehmens liegen, mit Schnittstellen zu verbinden. Die bessere Idee ist es, die Daten auf eine gemeinsame Plattform zu transformieren, wo sie allen Beteiligten vorliegen.
Die Plattform besteht aus drei Engines für Science, Collaboration und Data Science. Auf diesen Engines arbeiten über 500 Apps, die inzwischen auf der 3DEXPERIENCE Plattform verfügbar sind.
Der digitale Zwilling ist ein virtuelles Modell eines Produkts, eines Prozesses oder eines Service. Das ist nichts Neues, nur war es bisher nicht möglich, die Daten live in das Gesamtmodell einfließen zu lassen – so war das Gesamtmodell quasi ständig veraltet. “Das Schöne an der 3DEXPERIENCE ist, dass wir datengetriebene Analyse und modellierte Simulation zusammenführen können und die Vorteile beider Ansätze verbinden können.”
Graupner zeigt Praxisbeispiele, in denen der digitale Zwilling schon verwirklicht wurde: Eine Roboterzelle, in der Langzeitversuche mit der Öffnung und dem Schließen von Autotüren durchgeführt werden – der Zwilling ermöglicht hier die Offline-Programmierung der Roboter am digitalen Modell. Ein Versuchsaufbau bei Fraunhofer, in dem die Öffnung einer Heckklappe am realen Objekt und einem gekoppelten virtuellen Modell untersucht wird. Ein Aftersales-Projekt, bei dem der Wartungsmann alle Daten der Maschine zur Verfügung hat.
Er bezieht sich auf den Vortrag von Acatech-Präsident Karl-Heinz Streibich auf dem 3DEXPERIENCE Forum in Göttingen, der zeigte, dass die Digitalisierung einen Keil zwischen Unternehmen und Kunden treibt und dass Plattformen nach den “The winner takes it all”-Prinzip funktionieren. Es ist deshalb wichtig, in der Digitalisierung vorn dabei zu sein.
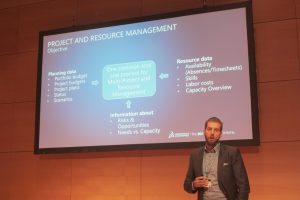
15:20: Sebastian Kress von Dassault Systèmes spricht über “Data-driven Portfolio Visualization”, über Projekt- und Ressourcenmanagement. Top-down-Planung muss von teambasierter Planung aus dem ausführenden Team heraus ergänzt werden. Mit Enovia und Exalead lässt sich auf Basis von Realdaten ein jederzeit aktueller Projektplan erzeugen, der den Input von allen am Prozess Beteiligten aufnehmen kann – im Gegensatz zu einer Planung, die von “oben” nach “unten” läuft und ständig an Realitäten angepasst werden muss, die bisher “oben” nicht bekannt waren.
So lassen sich im 3DEXPERIENCE Dashboard Flaschenhälse schnell erkennen und bei Bedarf zusätzliche Ressourcen zuordnen. Im Enovia Project Management lassen sich Ressourcen direkt im Gantt-Chart des Projekts umplanen. Die neue Rolle Project Planner in Version 2019x ermöglicht – auch auf dem Tablet – die erwähnte teambasierte Planung in das Gesamtprojekt einzubringen – immer mit komplettem Zugriff auf alle Ressourcen, Personen, deren Status und so weiter. Die Verbindung von Eniovia und Exalead ermöglicht es, die Projekt- und Programmergebnisse direkt mit dem Produktportfolio zu koppeln. Projektausrichtung, Planung und Ressourcen lassen sich koordinieren, überwachen und anpassen.
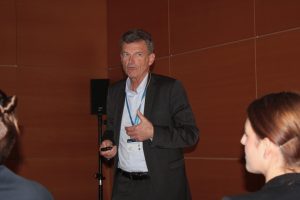
15:50: Das Privileg des letzten Vortrags des Events hat Joachim Bauer von Dassault Systèmes mit dem Thema “Variantenmanagement in der 3DEXPERIENCE Plattform.” Die wachsende Individualisierung treibt die Variantenvielfalt, beim VW Golf dauert es im Schnitt sieben Monate, bis die exakt gleiche Konfiguration vom Band läuft. Problem: Je kleiner die Stückzahl einer Variante, desto mehr überholen die Produktionskosten den erzielbaren Erlös. Modularisierung, Standardisierung von Komponenten und Prozessen sowie Teilewiederverwendung sind die Lösung.
Das immer wiederkehrende Kopieren der Daten für jede neue Variante führt schnell ins Chaos, ein Werkzeug muss her, das die Varianten mittels Verknüpfung der Komponenten erzeugen kann. “Wir nutzen Modelle statt Dokumente” – Modellbasiertes Konfigurationsmanagement. Ein Engineering Item enthält Modelle, Attribute, Zeichnungen und Dokumente wie rechtliche Hinweise oder anderes. Aus Engineering Items entstehen Module, Modulvarianten und schließlich Produkte.
Dazu gehören Regeln und Optionen, die dann die Konfiguration des Produkts in einer projektplanungsähnlichen Ansicht ermöglichen. In der Enovia-Rolle lassen sich die zulässigen Kombinationen, Abhängigkeiten und Zwangsbedingungen visuell definieren.
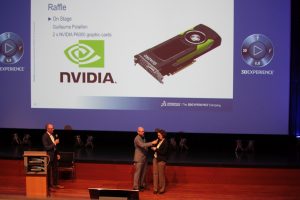
16:30, Paul-Hindemith-Saal: Florian Jurecka und Michael Clark leiten die Abschluss-Session im großen Saal. Die erste gemeinsame User Conference der CATIA- u d SIMULIA-Gemeinden geht zu Ende. Ich fand die Kombination – ergänzt durch Informationen zur 3DEXPERIENCE – sehr logisch und fruchtbar und die gute Stimmung während der zwei Tage bestätigt diese Beobachtung. Dassault Systèmes hat mit dieser Veranstaltung eine schöne Ergänzung zum eher auf der strategischen Ebene angesiedelten 3DEXPERIENCE Forum gefunden. Eine Reihe hochwertiger Preise – ein Wacom Tablet, zwei CAD-Mäuse und eine Space Mouse von 3DConnexion und zwei Nvidia P6000-Grafikkarten – werden an die verbliebenen Teilnehmer vergeben.
Aufgrund des positiven Feedbacks ist die Entscheidung gefallen, die Veranstaltung im nächsten Jahr zu wiederholen.
Ich bedanke mich fürs Mitlesen und verabschiede mich vom Liveblogging und aus Hanau.