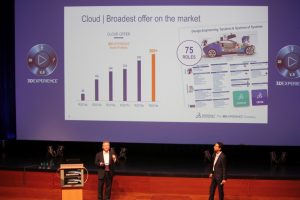
Willkommen zur DASSAULT SYSTÈMES User Conference in Hanau. Ich berichte live von dem Event im Hanauer Congress Park, zu dem sich über 500 Anwender der Dassault Systèmes-Lösungen rund um CATIA, SIMULIA und Simpack eingefunden haben. Der Congress Park integriert den historischen barocken Marstall des Hanauer Schlosses, der zur Stadthalle umgebaut wurde, mit einem modernen Anbau. In diesem ist auf zwei Stockwerken eine beeindruckende Ausstellung der Dassault-Systèmes-Lösungen sowie von Resellern und Partnern aufgebaut, die in den Pausen rege besucht ist. Gold Sponsors sind Cenit und Technia.
9:35: Philippe Laufer, CEO CATIA, und David Holman, VP SIMULIA R&D, eröffnen die Veranstaltung mit einem Überblick über die 3DEXPERIENCE Plattform. Die Plattform ist – unter anderem – Betriebssystem und Business Modell. Die 3DEXPERIENCE bietet inzwischen über 300 Rollen – das sind an bestimmte Aufgaben angepasste Funktionssets – in der Cloud.
Joby Aviation entwickelt ein elektrisches, autonomes Flugtaxi auf der 3DEXPERIENCE Plattform. Die Cloud ermöglicht die Zusammenarbeit rund um die Welt ohne IT-Supportaufwand.
ECAX Referenzmodell: Enterprise, Collaborative, Apps und Software as a Service. Enterprise bedeutet: Arbeiten mit lokalen Softwarepaketen, Collaborative ist die Verbindung dieser Pakete mit der Plattform. Werden die Pakete in die Plattform integriert, ist dies die Kategorie Apps, schließlich gehen die Pakete in der Plattform auf und stehen überall und auf jedem Medium zur Verfügung. Mit diesem Modell klassifiziert Dassault Systèmes den Digitalisierungsgrad von Firmen bei der Implementierung von Lösungen.
Laufer zeigt, wie nahtlos sich die Plattform in die Arbeit mit einem lokal installierten CATIA V5 integrieren lassen. Es ändert sich lediglich der Umgang mit Daten, diese werden bei der sogenannten POWER’By-Lösung in die Plattform gespeichert und von dort aufgerufen, statt mit Laufwerken zu arbeiten.
Die Trennung zwischen CAD- und Berechnungsingenieur ist keine “gottgegebene” Trennung, sondern entstand, weil die Werkzeuge so komplex waren, dass die Spezialisten sich auf eine der beiden Disziplinen konzentrieren mussten. Heute ändert sich das, weil die Werkzeuge einfacher und intelligenter werden. Holman erläutert nun das Simulia-Portfolio von der konstruktionsbegleitenden bis zur Multi-Body-Multi-Discipline-Simulation.
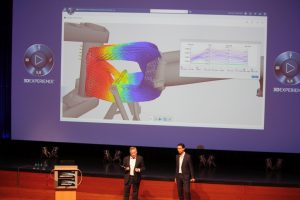
Laufer: “Wir entwickeln uns von CAD nach CAD – von Computer Aided Design nach Cognitive Augmented Design.” Das System unterstützt den Entwickler mit Generative Design und KI bei der Modellierung. Man modelliert nicht die Geometrie, sondern die Spezifikationen und die gewünschte Funktion, der Computer entwickelt auf Basis dieser Vorgaben eine optimale Geometrie.
Eine Industry Solution Experience besteht aus Rollen, die wiederum Funktionssets definieren – alles auf Basis der 3DEXPERIENCE Plattform. Der Kunde kauft nicht mehr fixe, umfangreiche Pakete, von deren Funktionsumfang er nur Bruchteile benötigt, sondern maßgeschneiderte Kombinationen, die auf die Prozesse in der Industrie abgestimmt sind. Die Experience für die Entwicklung von Elektroautos besteht beispielsweise aus neun Industrieprozessen, die Funktionalitäten aus allen Bereichen der Plattform enthalten.
Der Industrieprozess für die Batterieentwicklung enthält unter anderem Simulationsfunktionen, die das chemische Geschehen in der Batterie abbilden, aber auch mechanische und vor allem thermische Simulationen.
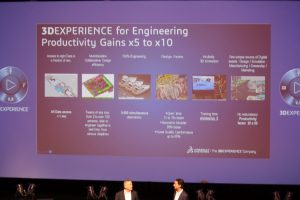
Die Einführung der 3DEXPERIENCE ermöglicht Produktivitätssteigerungen um das fünf- bis zehnfache. Laufer bringt einige Argumente, um dies zu unterfüttern – alleine die die Ladezeiten von Modellen werden 7-10mal kürzer, die Geometrieleistung steigt um 35 Prozent. 3D Immersion fünftelt die notwendigen Schulungszeiten.
Die Sprecher stellen das Champion Program und seine ersten Teilnehmer vor. Die 65 Teilnehmer sind besonders aktiv in den entsprechenden Foren und bekommen Zugriff auf neue Versionen, Funktionen und Apps, um diese zu testen.
11:00: Nach einer kurzen Pause geht es im großen Plenarsaal weiter mit Olivier Ribet, EVP Global Field Operation EMEAR. Er spricht über die Vision und Strategie von Dassault Systèmes in Cross Industry-Initiativen. “Digitalisierung funktioniert nicht, wenn man E-Mail und Daten mit einem SharePoint-Server verbindet, man benötigt eine echte Plattform.”
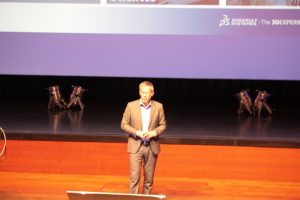
Er spricht über verschiedene Branchen, zunächst Aerospace. Die Produktionszahlen von Flugzeugen steigen von 1415 im Jahr 2015 auf 1816 im Jahr 2033, AM gewinnt schnell an Bedeutung, gleichzeitig steigen die regulatorischen Anforderungen an Flugzeuge, beispielsweise im Bereich der Lärmemission. Energieeffizienz und neue Antriebsarten spielen eine wichtige Rolle.
Ähnliche Anforderungen stellen sich im Bereich Life Sciences: Schnellere Innovationsraten, Bedarf an virtuelle Tests, steigende Regulierung, Kapitalisierung von Wissen und Knowhow sowie personalisierte und Präzisionsmedizin. Präoperative Planung an 3D-gedruckten Modellen der echten Organe des einzelnen Patienten, die direkt aus CT-Scans erstellt wurden. Dies ermöglicht eine sehr exakte Planung der Operation, bevor der erste Schnitt gesetzt wird. Das erleichtert dem Operateur die Arbeit und schont den Patienten.
High-Tech: In einem Chip in der Größe eines Fingernagels arbeiten mehr Subsysteme als in einem Flugzeug. Elektronische Geräte werden sich völlig verändern, wenn die Schaltungen direkt in ein Stück Kunststoff integriert werden können.
Dassault Systèmes bietet für all diese Herausforderungen Lösungen, die ganze Industrien abdecken und in einer Plattform vereinigen. “Vom Atom bis zur Stadt” reicht der Maßstab der Lösungen. Dassault investiert stark in Forschung und interessante Firmen. “We are here for the long run.”
11:38: Es geht weiter mit Additive: Steven Ribeiro-Ayeh spricht über “Print to Perform”, die Industry Experience für die additive Fertigung. Die Experience besteht aus den Apps Generative Design, Process Planning, Virtual Printing und Post Processing. Sie deckt nicht nur SLA-Metalldruck ab, sondern auch FDM-, MultiJet Fusion- und andere Druckverfahren – und das nicht nur in der Theorie, sondern in Zusammenarbeit mit den Herstellern und in der Praxis validiert.
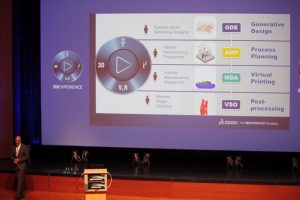
Generative Design kann Geometrie auf Fertigungsverfahren anpassen, beispielsweise Fräsen oder AM. Ganz neu integriert ist die Möglichkeit, komplette Baugruppen generativ zu optimieren. Lattice-/Gitterstrukturen erlauben es, extrem steife und leichte Bauteile zu generieren.
Process Planning arbeitet mit einem digitalen Zwilling des 3D-Druckers, das es ermöglicht, den Bauvorgang sehr genau und realitätsnah zu planen. Supportstrukturen lassen sich interaktiv erzeugen und ändern. Damit lassen sich Druckzeiten und -kosten genau vorhersagen.
Virtual Printing bedeutet, den Druckvorgang genau zu simulieren. Die App enthält eine Prozesssimulationsarchitektur, die auf Basis der Teilegeometrie, der Materialdaten und des digitalen Zwillings der Maschine realistische Simulationen des Druckvorgangs erzeugt. Das Mesh Intersection Tool generiert auf Basis der Slices optimale Netze für schnelle Berechnungen. Sogar die freie Oberfläche des Pulverbetts wird bei der Wärmeverteilung berücksichtigt. Parallel zum Druckprozess werden Risse entdeckt und in der Simulation berücksichtigt, um den Prozess anzupassen und die restlichen Teile sauber fertigen zu können. Multi-Laser-Systeme können simuliert werden, aber auch die HP MultiJet-Fusion-Anlagen, die mit Hilfe der Dassault Systèmes-Lösungen entwickelt werden.
In der Post Processing-App lassen sich Wärmebehandlungen und die Fräsbearbeitung zum Entfernen der Teile von der Bauplattform sowie der Supports simulieren. Auch die verbleibenden Eigenspannungen und duie daraus sich ergebenden Auswirkungen auf die Lebensdauer lassen sich analysieren.
Shape Compensation: Die Teile verdrehen und verbiegen sich in der Wärmebehandlung. Diese App ermöglicht es, das CAD-Modell so “vorzudeformieren”, dass sich nach der Wärmebehandlung durch die Verbiegung die gewünschte Form ergibt.
12:00: Mit kleiner Verspätung geht es in die Mittagspause. Danach starten parallele Sessions, ich werde die Highlights aus den vielen Vorträgen von Dassault Systèmes, Partnern und Kunden weiter live berichten.
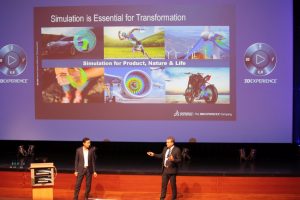
13:30, Paul Hindemith-Saal: Eric Bienvenue, VP Worldwide Sales SIMULIA, gibt einen Überblick über das Simulationsportfolio von Dassault Systèmes. Er wird von David Holman unterstützt. Die Frage ist: Wie bringen wir die bisher getrennten Silos Modellierung und Design zusammen, um Mehrwert zu erzeugen? Simulation ist unerlässlich für die Transformation.
Interessanter Vergleich: Als der Elektromotor die Dampfmaschine ersetzte, ergab dies in der Fertigung zunächst keinen Produktivitätsschub, der kam erst 20 Jahre später mit der Erfindung des Fließbands. Neue Technologie an sich ist nicht genug, es braucht einen Wechsel des Mindsets.
Multibody-Simulation ist ebenso aus der Spezialistenecke heraus wie Multidisziplinsimulation. Komplexe Produkte lassen sich mit Model Based Systems Engineering organisieren, Elektromagnetik ebenso analysieren wie Akustik.
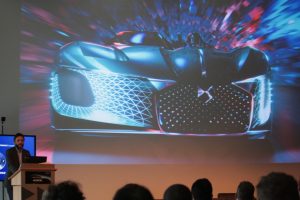
14:05: Weiter geht es im Design-Track mit Nicolas Deluy von DS Automobiles. Er zeigt eine Designstudie, deren netzartiges Beleuchtungskonzept in realen Modellen der DS-Baureihe wie dem DS7 umgesetzt werden sollte. Im DS3 Dark Side wurden erstmals 3D-gedruckte Gitterstrukturen aus Titan eingesetzt. Die Struktur, die sich aus dem DS-Logo ableitet, entstand durch parametrische Programmierung in Catia.
14:30, Brüder-Grimm-Saal: Nicolas Deluy ist auch Teilnehmer eines Design-Roundtable zum Thema “The next Mobility Experience”. Weitere Teilnehmer sind Taiki Furuki von Kubota und Gray Holland von UX-FLO. Furuki spricht über immer kleiner werdende Landmaschinen, die zusammenarbeiten. Auf japanisch bedeutet “Co-Design” “Zusammenleben”. Der Kunde ist das Ziel aller Entwicklungsanstrengungen und wird in Entwicklungsprozesse eingezogen.
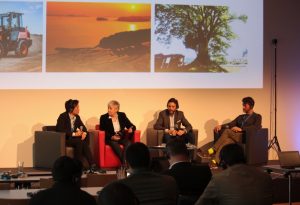
Anne Asensio von Dassault Systèmes, die das Gespräch leitet, sagt, dass wir nicht mehr Produkte designen, sondern Produkterlebnisse. Gray Holland: “Menschen mögen eigentlich keine Veränderungen. Holland designte eines der ersten Elektrofahrzeuge, das vor etwa 40 Jahren bei GM entwickelt wurde. Er nutzte dabei die damals sehr neue Stereolithographietechnologie. Grey: Der Job des Designers sei es nicht, Trends zu folgen, sondern Trends zu setzen und zu stützen – Experiences zu erzeugen. Dabei ändern sich Marken – sie sind nicht mehr unzugängliche “Helden”, sondern eher ein Bestandteil des Kunden.
Deluy: Der Designer wird zu einem Hybriden, der nicht nur das Design, sondern auch Technologien bestimmt und in seine Arbeit integriert. Deluy: Wir sind Designer, die mehr über die Werkzeuge lernen müssen, mehr über die Technik, die wir bisher lediglich verpackt haben. Furuki: Die Veränderungen in der Gesellschaft müssen in das Design einfließen.
Holland ist Berater und hilft Unternehmen dabei, Teams aufzubauen, die moderne Technologien implementieren. Interessantereise erlebt er die Widerstände gegen Veränderung im Unternehmen oft stärker als zwischen Unternehmen und Kunden. Asensio lobt die drei Designer als Prototypen der neuen Designergeneration, die eine neue Aufmerksamkeit gegenüber ihren Werkzeugen haben.
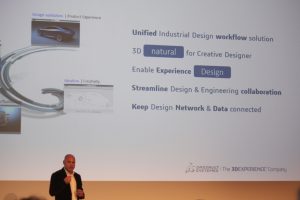
14:42: Die Designer sind schnell, fast 20 Minuten vor der Zeit – Xavier Melkonian von Dassault Systèmes freut sich, dass er mehr Zeit hat, die Strategie & Trends für CATIA Design zu präsentieren.Er sieht es als essentiell an, dass Designer, Systemarchitekten und Konstrukteure nahtlos zusammenarbeiten, weil die Disziplinen und ihre Arbeit zusammenwachsen. Kümmerte sich der Designer früher vor allem um die Außenhülle, so verschmelzen Design und Funktion heute immer stärker – siehe die aktiven Oberflächen in verschiedenen Concept Cars, bei denen Bewegung, Funktionen oder auch die Beleuchtung die Flächen des Fahrzeugs erobern.
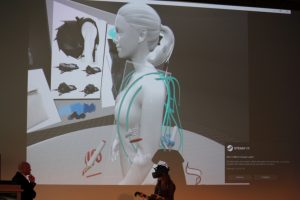
Designer müssen deshalb am 3D-Modell arbeiten können – und zwar am gleichen wie die Konstrukteure. CATIA Natural Sketching ermöglicht zeichnen in 3D. Es ermöglicht, 3D-Modelle auf dem Wacom-Tablet zu öffnen und darauf zu zeichnen. Mit Release 2019x erweitert Dassault Systèmes dieses zu Immersive Design, das mit der VR-Brille genutzt wird. Eine Kollegin von Melkonian zeigt eine faszinierende VR-Design, in der sie auf ein 3D-Modell eines Menschen einen Rucksack designt – einfach indem sie in der Luft zeichnet, spannt sie Flächen auf, positioniert und editiert Kurven. Sehr beeindruckend.
Catia Imagine & Shape: Im Zentrum der Entwicklung stehen Produktivitätssteigerungen, neue Funktionen und ein einheitlicher Workflow über die verschiedenen Modelliertechnologien hinweg. Verschiedene Kurven – verschieden in Bezug auf die dahintersteckende Mathematik – können miteinander verschnitten und aneinander angepasst werden. Ein beeindruckendes Video zeigt, wie die Technologie bei Honda Power Products zum Einsatz kommt.
15:25, Konferenzraum 5: Modellierung eines Aerospace-Teils im generative/additiven Prozess mit Andrés Bellés Meseguer von Prime Aerospace, einem österreichischen Engineeringdienstleister für die Luftfahrt. Die Prime-Konstrukteure entwickelten ein Scharnier für die Wartungstüren der Triebwerke des Airbus A340 neo. Durch eine Optimierung mit Abaqus/Tosca konnte eine Reduzierung des Gewichts auf 25% des ursprünglichen Teils erreicht werden – bei verdoppelter Steifigkeit!
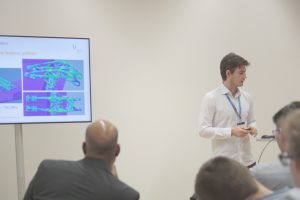
In einem zweiten Schritt wurde ein Workflow entwickelt, um diesen bisher relativ komplexen Ablauf zu vereinfachen. Ein Menü in der 3DEXPERIENCE führt durch den Prozess, der dennoch eine Menge ingenieurtechnisches Wissen erfordert, um ein sinnvolles Ergebnis zu erzielen. Je nachdem, welche Constraints definiert werden, verändert sich das Ergebnis der Optimierung sehr, der Konstrukteur muss viel nachjustieren – der Beweis dafür, dass es mit der vielbeschworenen “künstlichen Intelligenz” doch nicht weit her ist. Der Optimierungsalgorithmus tut genau das, was man ihm eingibt, ohne Rücksicht darauf, ob das Ergebnis Sinn ergibt. Nichtsdestotrotz sind die Ergebnisse sehr eindrucksvoll.
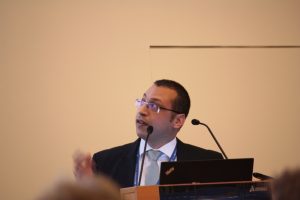
16:20, Saal Landgraf: Nach der Kaffeepause geht es weiter mit einer Kundenpräsentation aus dem Simpack-Bereich: Dr. Basem Abdelfattah von BMW und Magdalena Niedhammer von Dassault Systèmes sprechen über die Analyse von Kettenantrieben in Automotoren. Es wurden die Steuerketten verschiedener Motoren – und zwar als Modell mit allen Kettengliedern – analysiert.
Mit Hilfe der Simpack-Analyse konnte Abdelfattah zeigen, dass sich das bekannte Kettenjaulen durch Versteifung einer Lagerhalterung reduzieren ließ. Eine Überarbeitung des Simpack-Solvers in Release 2018x und 2019x ermöglichte dabei eine Reduzierung der Rechenzeit auf ein Viertel.
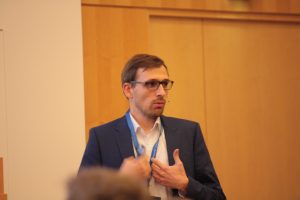
16:50: Carsten Schulz, CAE-Professor an der Anhalt University of Applied Sciences spricht über “Maintenance Prediction using Real-time Digital Twins”. Die Intention der Untersuchung war es, statt festgelegter Wartungsintervalle die wahre Belastung eines Getriebes zu berechnen und basierend darauf die Wartung dann durchzuführen, wenn sie tatsächlich notwendig ist.
Das heute übliche Condition Monitoring ermöglicht die Dokumentation des Lebenslaufs, aber keine echte Voraussage über die Zukunft. Virtuelles Condition Monitoring dagegen – das mit realem Condition Monitoring validiert wird – ermöglicht es, die nächsten 30-40 Sekunden vorherzusagen und sogar eine Motorsteuerung so zu beeinflussen, dass beispielsweise Eigenfrequenzen vermieden werden. Mit Hilfe eines selbstgebauten Getriebes wird dies derzeit real erprobt, später sollen Versuche an einem kommerziellen Lokgetriebe folgen. Die Idee ist, eine kontinuierlich fortgeschriebene und mit den realen Werten korrigierte Lebensdauervorhersage zu erhalten.
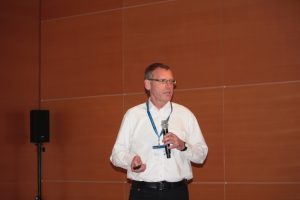
17:10, Gebrüder-Grimm-Saal B: “Concept Modeling @ Ford” mit Axel Hänschke von der Ford Motor Company. Der Autohersteller hat ein vierstufiges Entwicklungskonzept von der 1D-Funktionssimulation bis zur detaillierten Simulation und der Übergabe des Konzepts an die Detailkonstruktion. Bisher war es jedoch nicht möglich, die Ergebnisse aus der Detailkonstruktion zurück in die Konzeptphase zu spielen, beispielweise für die Entwicklung einer neuen Fahrzeuggeneration. Hänschke hofft hier auf die Einführung der 3DEXPERIENCE Plattform bei Ford.
Hänschke spricht über die mathematische Erfassung und Optimierung von Design Spaces im Auto. Die notwendigen Komponenten wie Räder, Antrieb, aber auch Passagiere und deren Sichtfelder werden in einer Matlab-ähnlichen Sprache erfasst und angeordnet, der Platz dazwischen ist dann der Bauraum für die Fahrzeugstruktur, in dem beispielsweise mit Generative Design eine optimierte Struktur definiert werden kann.
Tayeb Zeguer von Jaguar Land Rover konnte nicht anwesend sein, sein Vortrag wird deshalb von Nikolai Baumeister von Dassault Systèmes gehalten. Es geht um die Verbindung von SFE mit der 3DEXPERIENCE Plattform, also der Konzeptmodellierung von Karosserien. Jaguar Land Rover hat diesen Prozess auf der 3DEXPERIENCE Plattform zu Teilen automatisiert, um Teile der Karosserie mit Hilfe der Simulation zu optimieren. Unter anderem werden Positionen von Dachholmen und deren Querschnitte in Bezug auf Dachcrashsimulationen optimiert.
JLR hat hier einen interessanten Prozess implementiert, der die Vorteile der Integration von Modellierung beziehungsweise Geometrieerzeugung mit der Simulation auf einer Plattform beispielhaft zeigt. Sicher auf einem hohen, komplexen Niveau, aber mein “Takeaway” von heute ist es, dass wir viel stärker über die Integration der Simulation in den Konstruktionsprozess nachdenken sollten. Die Fortschritte in den Simulationstools und auch das Aufkommen von Plattformen oder integrierten Dateiformaten machen dies viel einfacher als dies noch vor Jahren war. Die Vorteile und Potentiale dieser Kombination sind jedenfalls in der Praxis nachgewiesen und wirklich verblüffend groß.
17:50: Ende der Sessions. Es folgt eine Abendveranstaltung und wir sehen (beziehungsweise lesen) uns hoffentlich morgen früh ab 9:00 Uhr wieder. Ich wünsche einen schönen Abend!
Hier geht es zum Liveblogging von Tag 2 der User Conference.