On April 27th, Dassault Systèmes inaugurated the 3DEXPERIENCE Center at Wichita State University (WSU) in partnership with the National Institute of Aviation Research (NIAR). The grand opening of the center caps a 3-year effort to bring together a number of emerging technologies in one place, including virtual reality, additive manufacturing, advanced robotics, and other advanced design and manufacturing technologies.
3DEXPERIENCE CENTER AT WICHITA STATE UNIVERSITY
Dassault Systèmes’ 3DEXPERIENCE Center is part of an interconnected community of top researchers, companies and laboratories to accelerate innovation. When completed, the Innovation Campus at WSU will consist of 24 buildings located on 120 acres, including 9 partner buildings, including companies like Airbus.
The 3DEXPERIENCE Center, which is located in the Experiential Engineering Building, is a 22,000 square foot facility designed to accelerate Aerospace companies’ ability to innovate from initial requirements through certification.
CUSTOMER COLLABORATION ROOMS
Three Customer Collaboration Rooms (CCR) are located in the 3DEXPERIENCE Center. Each CCR allows up to 8 people from various functions including program and subcontract management, engineering, manufacturing, testing and certification, and marketing to seamlessly work together in a state-of-the-art collaborative space. These rooms include dual monitor high performance work stations, a high resolution interactive touch display, and web conferencing tools along with the full suite of 3DEXPERIENCE platform solutions from Dassault Systèmes.
Customer Collaboration Rooms allow teams to seamlessly collaborate both on-site and with teams in other locations around the globe from defining the initial program requirements, developing the systems engineering architecture, developing a system DMU, optimizing designs with simulations, digitally designing the manufacturing process and combining virtual and physical testing to complete certification. This can rapidly accelerate new programs from concept to takeoff while significantly cutting development costs.
VIRTUAL REALITY & IMMERSION
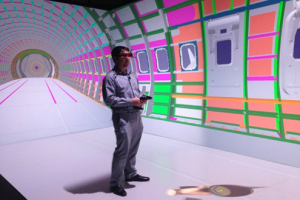
Virtual and augmented reality technologies allow business leaders, program managers, and various functions to view new innovations in a rich 3D immersive environment before they exist into reality. Simply stated, these environments enable “virtual creation before physical creation.” Teams can explore new designs in 3D and see the results of multiple simulations ranging from system level mission simulation to specific multi-physic simulations like seat crash and bird strike, and many others.
The virtual creation and mission simulation of new systems before the physical creation allows teams to ensure confidence in the conceptual design to meet their customer’s stated requirements as well as drive organizational alignment early in the design cycle. This alignment avoids potential downstream changes and rework which reduces program risks, improves system quality, increases schedule predictability, shortens cycle times, and ultimately lowers costs.
ADDITIVE MANUFACTURING
The Additive Manufacturing lab allows engineers to optimize standard parts for cost and weight, prototype and produce complex parts quickly and cheaply without tooling, and cut material waste compared to traditional milling methods. Engineers leverage the 3DEXPERIENCE platform to design and simulate highly optimized parts based on space allocation, loads, constraints, manufacturing processes, and multi material requirements (polymers, metals, and engineered materials) and then use various 3D printers in the lab to produce these optimized parts.
Generative Design Engineering (GDE) combined with Additive Manufacturing can be used to optimize the part/system – typically resulting in reduced cost and weight reductions to the order of 70% and more – as well as reduce overall part counts, lower tooling costs, and avoid material wastes. This allows aerospace companies to create both prototypes and final production parts at significantly reduced procurement lifecycles and lower costs than traditional methods while accelerating the pace of innovation.
MULTI-ROBOTICS ADDITIVE MANUFACTURING (MRAM)
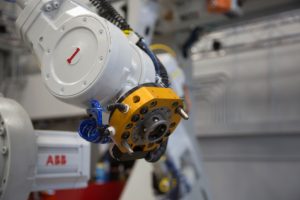
The Robotics lab hosts the Multi-Robotic Advanced Manufacturing (MRAM) cell (currently the largest hybrid manufacturing cell in the world) to provide a flexible and scalable manufacturing process by automating the factory floor leveraging Multi-Axis Subtractive and Additive Hybrid Manufacturing processes and methods. Now it is possible to build highly customized parts and systems with multi materials, lower the number of parts, improve quality versus traditional production methods and reduce material waste up to 90 percent.
MRAM allows customers to manufacture, assemble and inspect a new system without expensive tooling leveraging Multi-Axis Subtractive and Additive Hybrid Manufacturing to create more complex shapes, with a broader selection of materials for a single cell. The future factory will enable customers to create fully functioning assembled systems (e.g. UAVs, airplanes, cars) manufactured leveraging the technology, methods, and processes associated with MRAM, accelerating production and lowering part counts while enabling greater customization and quality.
REVERSE ENGINEERING & INSPECTION
The Reverse Engineering Lab enables reverse engineering technologies to create virtual models from existing physical parts by using 3D scanning technologies. This can generate computer-aided design (CAD) models for detailed design, simulation analysis, prototyping, model testing, model failure analysis, and quality assurance or allow teams to digitally inspect tooling and purchased and manufactured parts/systems to ensure they comply with their specifications.
Reverse engineering can bridge the gap between the physical and the virtual work. Reverse engineering allows customers to rapidly create 3D CAD models for legacy or purchased parts, eliminate discrepancies between “as designed” and “as built,” and ultimately improves overall quality.
THE POWER OF THE 3DEXPERIENCE PLATFORM
Companies will also be able to leverage the power of Dassault Systèmes 3DEXPERIENCE platform for Aerospace companies to enable all functions to work together simultaneously on a single collaborative platform to bring new innovations to life Dassault Systèmes Industry Solution Experiences for Aerospace help companies to:
- Increase win rates through by exploring and validating 1000x design proposals to optimize the proposal to win.
- Accelerate maturity from concept to manufacturing while driving 40-60% of cost out
- Expand virtual testing across the lifecycle to reduce the physical testing to certify the new aerospace system.
- Ensure manufacturing can deliver on target the first time every time from ramp-up to rate adjustments for ongoing production.
The 3DEXPERIENCE Center creates a unique capability to combine the virtual and the physical to accelerate the design process.
THE CUTTING EDGE OF INNOVATION
The center brings together a number of cutting edge technologies and seamlessly integrates them end-to-end. Companies can come and innovate, create new products, prove out new processes and systems of work, and experiment with new technologies alongside the top experts in academia and industry. They can accelerate innovations from initial concepts to launch, as well as prove out new processes and systems of work to determine how to transform into their operations.
While in the “heart of Aerospace” in Wichita, Kansas, the 3DEXPERIENCE Center can host any industry to demonstrate the power of the 3DEXPERIENCE platform; host workshops, seminars and training; and act as an incubator for startups and established companies to accelerate new projects via 30 to 90 day engagements by providing the expertise and facilities to drive innovation.
Learn more about the 3DEXPERIENCE Center at Wichita State University.