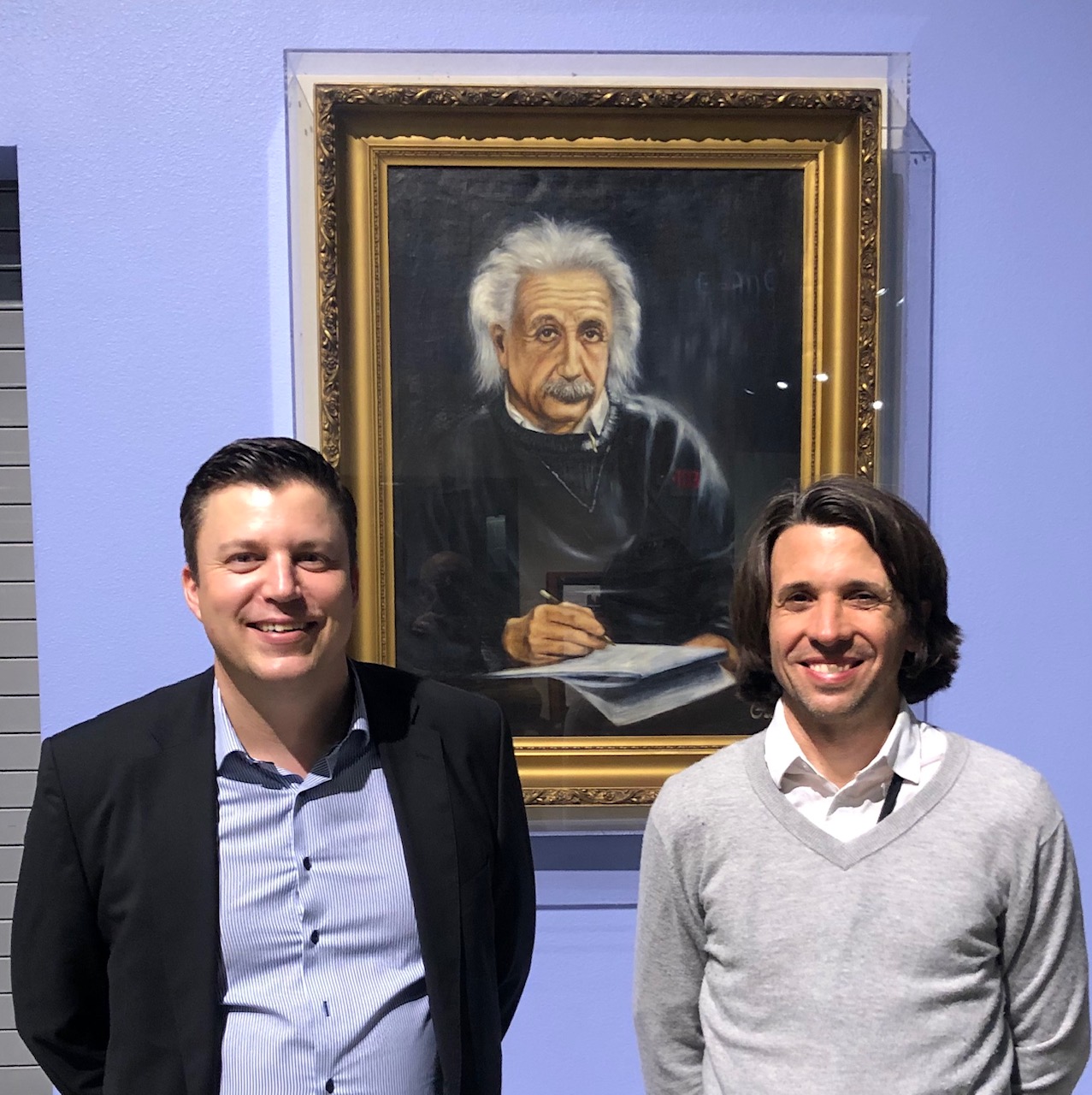
Designing and building a car for a Formula One racing team is quite different than designing and building an everyday automobile. These cars are subject to faster speeds, obviously, as well as increased stresses. Therefore, a great deal of careful design and thought must go into creating a Formula One car that can perform well on the race track. Many Formula One teams have begun utilizing newer technology to design and build their vehicles, including additive manufacturing, topology optimization, generative design, and more.
Recently, Dassault Systèmes CATIA and SIMULIA teams participated in the 2019 Topology Optimization Roundtable, which was organized by United States Association for Computational Mechanics (USACM) and hosted by Sandia National Laboratories in Albuquerque, New Mexico. The event posed a challenge to participants: use topology optimization software to design a part for a Formula One racecar. Whoever came up with the most effective design would be declared the winner.
The part in question was a suspension upright, which attaches the wheel, brake rotor, hub, brake caliper, and steering arm to the vehicle. This particular part is subject to significant forces due to braking and cornering, and thus the design would need to accommodate a variety of loads. These included various inside/outside cornering, and forward and rearward braking cases.
Approach to the Challenge
The Dassault Systèmes team used Function Driven Generative Design which is a physics-based approach that uses Cognitive Augmented Design technology where the design is driven by functional specifications with the goal of creating innovative lightweight products. This technology streamlines a previously disjointed process and allows engineers to come up with new shapes in a reduced amount of time.
The software is comprised of a combination of CATIA design and SIMULIA FEA apps including Tosca’s Topology Optimization software to design and simulate a suspension upright with the objective of minimizing mass. They designed three versions of the part – one to be additively manufactured, one to be milled, and one to be cast. The materials to be used were aluminum, titanium, and steel.
The software allowed the team to create surfaces for the part fully automatically with a single mouse click, and in less than a minute. Each surface was automatically connected to the non-design areas to create a solid. The load cases from the initial simulation (or from the optimization) were automatically duplicated on the result concept for a continuous validation of the design.
The design process for each manufacturing method was a little different than the others; the additively manufactured part, for example, could be generated as a final shape right away while the milled part needed an extra step to include the material that the part would be milled out of. Each part, however, took only minutes to create from initial concept to final design.
Results: Dassault Systèmes Takes First
The efficiency and effectiveness of Dassault Systèmes’ software impressed the competition judges, who awarded the team first place.
The competition was a great example of how Dassault’s technology can be used to generate, simulate, and perfect a complex part in minutes. The Formula One racing world can benefit greatly from these tools, which allow for the creation of better, stronger, more effective parts that give race cars and their drivers an edge over the competition.
The applications of this software go far beyond Formula One, as well. From the general automotive world to the aerospace and defense industry, topology optimization is playing a bigger and more important role in improving performance and safety – without sacrificing cost or time to market. It is, in fact, helping manufacturers create parts faster than ever before, optimizing them so that they, and their customers, can be assured of the best possible performance.