Dassault Systèmes is hosting its second annual Science in the Age of Experience ‘megatrends’ event, May 16-18 in Chicago. The conference brings together hundreds of scientists, technology experts, customers, thought leaders and industry influencers to discover how science, engineering and technology are joined together to simulate and create a better world – to imagine the impossible and innovate the invisible.
We had the chance to catch up with Subham Sett, a director from Dassault Systèmes SIMULIA brand who is focused on strategic initiatives including Additive Manufacturing & Materials. Sett is the driving force behind one of the key event tracks, the Advanced Manufacturing (AM) Symposium taking place on Day 1, and is also running the Day 2 Hackathon. The AM Symposium explores how companies are embracing and adopting additive manufacturing to transform their business, while the Hackathon is a contest pitting additive manufacturing (or 3D printing) design teams against each other to see which team can create and print the best 3D design. Winners will be announced at the conclusion of the event, and we can’t wait to see the printed products.
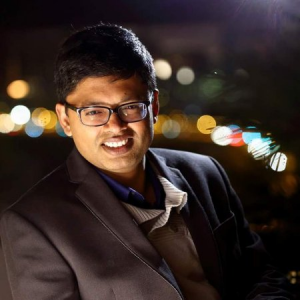
Q: Subham, can you give us a brief history of additive manufacturing – what has fueled its adoption? What’s all the buzz about?
Subham Sett: Over the past century we have witnessed amazing milestones in manufacturing. The most impactful achievements share one important commonality – they brought greater simplicity and automation to the design and production process. From the roll-out of Henry Ford’s moving assembly line in 1914, to the launch of the first CAD Software in 1954, and then the arrival of industrial robots in 1973, each of these revolutionary developments allowed manufacturers to speed production and bring better products to the marketplace more quickly, while advancing society technologically. Today we are witnessing the next mammoth milestone -the widespread adoption of additive manufacturing technology, popularly known as 3D printing, in production. Invented for rapid prototyping purposes in the 1980’s, 3D printing had many niche applications that were mostly non-structural, but the technology’s true potential remained untapped for decades. With the advent of highly controlled materials and processes, we are now seeing the proliferation of much more functional engineering applications using layer-wise manufacturing methods.
At the moment, there’s a lot of buzz about using additive for parts that even several years ago were unthinkable to produce. Metal additive is hot, no pun intended, while the need for speed, better yield rates and the progress towards product part are all in everyone’s mind. The excitement is not only for metals but for polymers as well, with new processes coming online to produce parts at a rate that perhaps in the near future will enable volume production, or mass customization in units of one!
Q: What role does simulation play in additive manufacturing?
Subham Sett: I see simulation playing a tremendous role in 3D printing whether we talk design, material characterization or the manufacturing process. With our ability to now for topology optimization in a design environment we are empowering designers to extend the design freedom that additive already provides them, but do so keeping the parts function in mind. Designers can also stay in the comfort of their design environment and make design variations, knowing very well that their changes are backed by simulation validation.
Finally, the part that’s being produced has to come off the build plate and post-processed. While simulations will help with both, we need to remember that while the manufacturing engineer may be finished producing a part to spec, additive can introduce enough history (e.g. voids, cracks, defects) into the part which if not analyzed for in-service can lead to catastrophic failure in the field. Simulation of in-service, fatigue, failure and durability while accounting for the manufacturing history has the potential to accelerate the time to market of additive parts.
Q: How do Dassault Systemes’ brands SIMULIA and BIOVIA enable us to “imagine the impossible and innovate the invisible?”
Subham Sett: Science is at the core of our mission at Dassault Systèmes in harmonizing product, nature and life. With SIMULIA and BIOVIA we have an incredibly strong team of scientists and engineers that dare to change how we innovate – bringing designs to life that are based on the fundamental principles of science. For additive manufacturing, it holds particularly true. With BIOVIA we can design materials based on first principles of molecular dynamics. Whether we are dealing with metal crystallanity or putting a polymer chain together, we can do so virtually before a single composition is created in the lab. Armed with this knowledge of the thermo-physical behavior we can then connect these micro-scale models, at the mesoscale level, to a part level product. Now, at the part level, our process simulation tools coupled with the specificity of the manufacturing process allow us to engineer, re-engineer, or redistribute individual bits of material – whether its powder particles or fibers. Additive manufacturing is usually talked about in the context of design freedom, but by joining the atom to the airplane we can create, what Dassault Systemes CEO, Bernard Charles said at last year’s conference, a material for a purpose rather a purpose for a material.
Q: Tell us more about the AM Symposium? What can attendees expect?
Subham Sett: While additive conferences are happening across the globe almost every other week, they focus on core topics related to the process, to certification, qualification, best practices and other methods. We at Dassault Systemes are quite uniquely positioned with what we are offering in the space in terms of the digital thread from design, materials and manufacturing. The 3DEXPERIENCE platform is enabling the entire AM network whether it’s inside one’s organization or outside. The AM Symposium is meant to bring this community together so we can listen from leaders who will share their experience on several topics including business transformation, design for additive, materials and certification and best practices. To pick a few instances here, I am quite excited to hear what adidas has to say about their AM evolution or what Vijay Jagdale, United Technologies Research Center (UTRC) has to say on physics based modeling of laser powder bed fusion process, and everyone else in between.
The Additive Manufacturing Symposium is truly the first of its kind in our community and I hope we can reward our attendees by providing them with a very unique experience
Q: The Hackathon seems like a novel concept for the simulation community? What are you expecting to make or break?
Subham Sett: We’re really excited to host a Hackathon! This two-day experience will give participants an immersive opportunity to learn about additive manufacturing from design to manufacturing, engage with software and hardware developers, consult with industry experts to address design and simulation challenges while learning about new trends in materials, processes and new applications. The Hackathon challenges will be design statements based on real-world problems proposed by industry experts. Teams will be assembled based on area of interest and attendee expertise and comprise industry, and academia and each team will be assigned a dedicated Dassault Systèmes mentor.
At the end of the Hackathon, teams will have the opportunity to print their designs and present their solutions to a selected panel of jurists. Winners of the Hackathon will be announced before the conclusion of Science in the Age of Experience. By the way, we just held a design hackathon at our Design in the Age of Experience event in Milan. It was a great success! 3D-printing changed the way makers bring their ideas to life. We are attempting to do the same thing here – only this time, we are enabling participants to expand their design horizons digitally before realizing their creations.
Q: What other exciting sessions, activities or general themes should attendees look for?
Subham Sett: For over a year, we’ve partnered with industry, government labs, universities and research centers. Much of the work has been focused on getting the virtual solution right – that is, does it match real world results. Can we predict distortion trends? Can we predict residual stresses? What about the evolving microstructure of the material? How about composites additive manufacturing? Can we include multiphysics optimization to narrow down design choices? Much of this work will be shown at a technical level – where experts in the audience scrutinize the results but also learn from the early adopters. For attendees, who are just getting started with additive manufacturing or perhaps are aware of their own organization’s venture into additive these sessions will be excellent. These technical papers are spread out across a number of sessions, so follow the conference schedule well so you don’t miss out.
Q: Who is your Science superhero and why?
Subham Sett: That’s a tough question to answer! If you’d asked me who is my current day superhero, I would say without a doubt Iron Man or his real-life avatar Elon Musk! I am amazed how ordinary people empowered by science can innovate and reach the sky, beyond and back. If I had to pick one, Stephen Hawking egged me on to question everything I saw and learned through the lens of science. In his book, A Brief History of Time, he brings forth the debate on the origins of the universe and goes on to say, “Recent breakthroughs in physics, made possible in part by fantastic new technologies, suggest answers to some of these longstanding questions. Someday these answers may seem as obvious to us as the earth orbiting the sun – or perhaps as ridiculous as a tower of tortoises. Only time (whatever that may be) will tell.” I think the same is true for additive manufacturing. There are many questions still about whether this technology will truly become a mainstream discipline. Only time will tell if, but for now I am very hopeful.