In an optimized design and construction process, the virtual twin captures the architect’s intent: the types of materials desired, styles of rooms, types of constraints to address, etc. The construction team can then assemble the building based on a list of integration-ready modular systems identified in the virtual construction twin.
With this approach, the GC (as prime integrator) orchestrates the work from virtual makers, prefab shops and microfactories, and determines the construction experience needed to deliver and install productized modules in the field.
Assembly OSM: A Modular Strategy in Action
New York-based Assembly OSM, founded by SHoP Architects co-founders Bill and Chris Sharples, was established as a modular construction company. The team engineers components and sub-assemblies (structural steel chassis; unitized facades; wall, floor and ceiling cassettes; mechanical, electrical, plumbing and environmental systems; kitchen, bathroom and casework pods; building cores with elevators and stairs) to fit a single platform of infinite combinations.
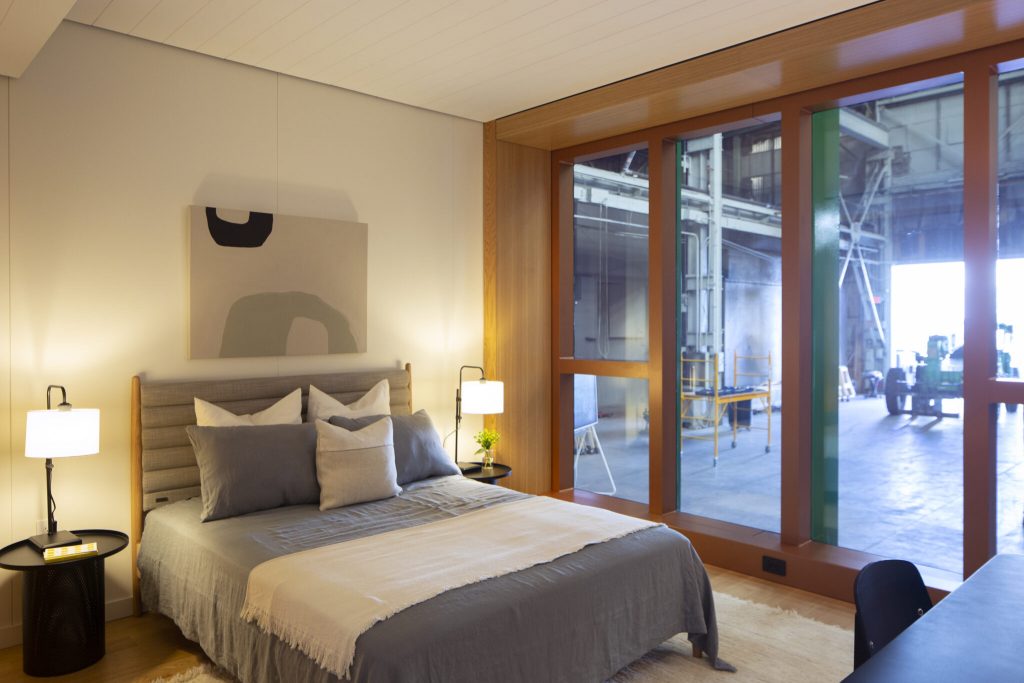
(Photo courtesy of Assembly OSM)
These individual modules can take a wide range of different dimensions and shapes, enabling tremendous variability in building type, size and layout. Buildings are designed by Assembly OSM as a 3D digital twin that embodies the dimensions and materiality of every single component. Components are manufactured by the company’s supply chain. Products are assembled by Assembly OSM and then “stacked” on the jobsite by the company’s general contractor partners.
Each end result aims for high-quality performance, high-end aesthetics, sustainable materials, and highly cost-effective delivery and operating expense. Projects also benefit from a significantly reduced time to completion due to the pre-engineering.
You can learn more about how productization transforms the construction industry.
This article is excerpted from THE PRODUCTIZATION EFFECT: How integration-ready modules will transform the roles of general contractors, specialty contractors and the entire construction value chain. This white paper maps the path to productization and defines how general contractors, specialty contractors and the entire construction value chain can leverage virtual twins on an end-to-end collaboration platform, transcend the limitations of classic industrialization and leapfrog to personalized construction.
Related links:
- Dassault Systèmes Construction Solutions
- Dassault Systèmes Building Solutions
- Reinvent the Construction Industry With Productization
- Design Dazzling Façades At Lightning Speed
- How to Accelerate Next Gen Data Center Innovation
- Integrated Built Environment for collaboration& project management
- Building Design for Fabrication for digital continuity