A new era in manufacturing tech is dawning—one that deserves the name “renaissance.”
So say some of the sector’s most respected voices. They point to the convergence of synergistic and maturing technologies—the Industrial Internet of Things (IIoT), super-fast Internet, mobile communications, big data, virtual and augmented reality, digital twins and 3D printing among them—that are pushing our mass production methods into the future.
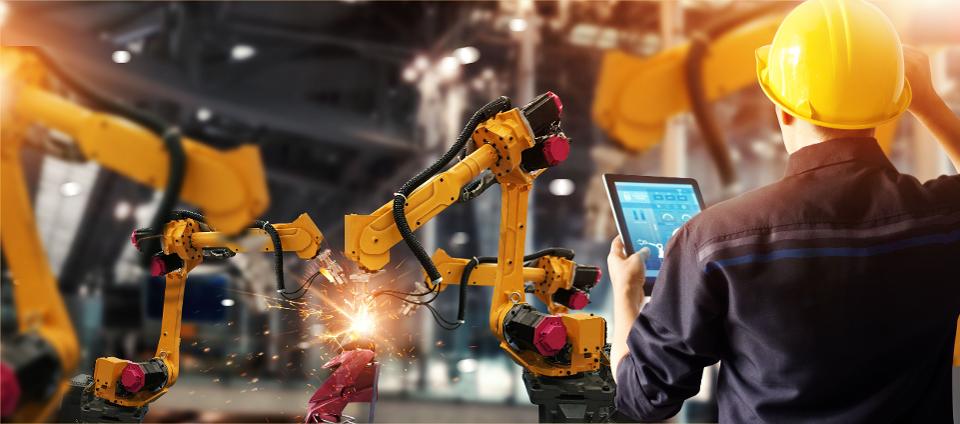
“This Industry Renaissance is global and it’s bringing new ways—both real and using virtual technology—of inventing, learning, producing and trading,” said Bruno Latchague, Senior EVP, Global Brands, Dassault Systèmes. “It’s shaking all the existing sectors of the economy and society. We’re seeing new categories of industrial firms creating new categories of solutions for new categories of customers.”
Here are five crucial points about the Industry Renaissance that everyone should be aware of.
New Methods Are Disrupting Manufacturing
New technologies and methods are creating disruptions in industrial manufacturing.
“Digital twin” technology, for example, involves creating a virtual copy of a product, a component, a production line, a factory or even an entire city. This simulation allows manufacturers to virtually implement and test equipment and processes before implementing them in reality.
Advances in virtualization technology now mean that digital twin testbeds are more accurate than they were before. Manufacturers can tweak their ideas in virtual form without needing to build physical versions first—saving money and time.
Virtual testing can take place as part of a digital experience platform that links the diverse players in a production cycle—from the resource extraction stage to production and then on to the safe disposal of byproducts. Such a platform functions as a central information-sharing hub, letting participants better collaborate with each other.
The result is synergy that improves manufacturing. A supplier may notice that a factory is using a sub-optimal material for a component and suggest a better alternative; or a consultant, exposed to data that gives a picture of the entire system, may discover management flaws and suggest solutions. Each stakeholder benefits from this whole-system view.
One especially compelling example of virtualization tech is Dassault Systèmes’ digital twin of the city of Singapore itself. Using an array of images and data—including geometric, topological, environmental, road-traffic and other information—the company’s technicians created a detailed model of the city-state.
The digital model allows users to explore the impact that proposed projects will have, optimizing logistics, infrastructure, environmental and disaster management and security—and beyond.
Fundamental Economic Shifts Are Changing Industry
The manufacturing sector has in recent years “been heavily challenged” by a deep transformation of the economy, said Guillaume Vendroux, CEO of DELMIA, Dassault Systèmes. DELMIA delivers solutions to model, execute and optimize global operations.
That transformation has to do, he said, with a shift towards the “economy of the experience.” Theorized as the successor to the service economy, the experience economy involves consumers’ placing increasing value on the “experiences” that goods or services can provide them, in distinction to placing it on the ownership of material objects themselves.his shift has left the manufacturing industry, which by definition specializes in physical products, at a crossroads. In Vendroux’s words, it “has triggered a very deep movement to totally transform our way of doing things.”
Human Resources Will Be a Key Investment
Vendroux believes that human resources is a key development area given the new industrial realities and will require significant investments of time and training.
“Knowledge and know-how will become the value of each company and the differentiating factor between them,” he said. “Industry needs to find ways to capture knowledge store it and provide it to their teams in order to continuously improve their work.”
At present, he said, industry is seeing something of a gap at the managerial level when it comes to awareness of how to use these new technologies to create value. Organizations need to overcome that gap.
Meanwhile, traditional boundaries between different industrial and business sectors and disciplines are breaking down. That means both managers and workers need to diversify their skill-sets and function as specialists in multiple areas.
Boosting employers’ understanding of technological advances and the potential they offer remains a challenge. Yet, suggested Dr. Karel Eloot, Senior Partner, McKinsey & Company, the growing awareness of the role the IIoT can play in industry is a positive sign.
“In 2016, we looked around the globe and asked firms how enthusiastic they were about the Industrial Internet of Things,” he said. “We found in Japan and Europe that they were thinking, ‘Is this hype or is this real?’ But in 2017 we found that the enthusiasm had gone up.”
China Is Leading The Renaissance
The Industry Renaissance’s disruptive influence is also being felt geopolitically, as emerging economies seek to catch up with the developed West.
“China has always been more enthusiastic” about the opportunities the Industry Renaissance has to offer, Eloot said.
“They see it as a real opportunity to lead, because they know there is a gap with the Western world and they want to accelerate the closure of this gap by using these new tools and digital approaches,” he said.
As one example, the Chinese government is doubling down on a strategic and industrial plan announced in 2015 called Made in China 2025.
That plan, Eloot said, is highlighting key industries that whose development will be accelerated with help from these technological tools driving new industrial breakthroughs.
The IIoT Is Creating New Value
Eloot said the latest technological ability to monitor product performance has opened up new value channels in manufacturing.
The IIoT-enabled ability to monitor employee movements around a potentially dangerous shop floor, for example, is triggering a decline in the incidence of workplace accidents. IIoT monitoring tech can now collect data that, fed into a virtual digital twin of the shop floor, can drive changes in workspace design and workstation placement.
The IIoT also unlocks equipment predictive maintenance. Sensors can monitor wear and tear on gear, triggering maintenance before equipment breaks down—and in the long run making the workplace safer.
Analytics tools can also help with predictive maintenance, crunching system data and making correlations to forecast errors before they occur. Such advances boost efficiency and cut downtime, offering manufacturers value-added services.
Companies Are Shifting From Capex To Opex
“Companies are looking at how can they shift focus from capital expenses to operational expenditures and how we can have our customers grow with the business,” Eloot said.
That is consistent with a general shift from a consumer-based economic model to a user-based one.
Aviation companies, Eloot said, are now “offering aircraft engine hours rather than just selling aircraft engines.”
That lets customers shift from business models based on one-time capital expenditures to those that revolve around smaller, recurrent operational expenses. Customers get not only easier accounting out of such deals, but better service, too. The providers own and manage the gear. This gives them the incentive to make sure it runs optimally.
If a supplier can guarantee the minimum performance of a particular product or component, Eloot said, it creates value for the end user in the form of more tightly controlled operational costs.
Big Data Drives The Engine
The original Renaissance encompassed a range of developments: cultural achievements, philosophical transformations, and bold scientific discoveries, in addition to technological breakthroughs. Though legendary individuals played their part in that era, it really was the product of various phenomena.
Today’s Industry Renaissance is much the same. It’s the product of a number of technologies that are coming together to create powerful multiplier effects. The common denominator is data—our era’s powerful new data-collection and analytics capabilities, and their ability to create connections between people and assets.
“Data is the new oil,” Eloot said. “People are collecting data from their equipment and turning that into insights that can create new value.”
You can read the full report, created based on the presentation done by Dr Karel Eloot during the event Manufacturing in the Age of Experience in September 2018 in Shanghai, China.