The following article is excerpted from DFMA for Construction: The 4 Perspectives Shifts Enabling Scalable Urban Development, a whitepaper developed by Dassault Systèmes. To read more about continuous integration, download the full whitepaper here.
Modeling tools have clearly benefited from digital transformation. Still, if a building model exists independently on its own platform and without dynamic access to manufacturing, assembly and project management data, it remains extremely limiting in its potential to support design automation and reduce repetitive tasks.
Such siloed data requires periodic synchronization that creates friction in the design process, redundancy and rework. The more tools in use, the more friction occurs whenever data is exported, imported and reconciled.
Alternatively, an integrated, model-based design centralized on a shared platform and continuously updated supports a designer’s ability to leverage design automation for exploring exponentially more solutions, feeding it with performance and process simulation data, and embedding the design with manufacturing intelligence.
In addition to representing the intentions of the architect and instructions for fabricators, a model-based design continuously reinforced with data from all phases of the building life cycle can reflect three additional perspectives: the project owner, the engineer, and the contractor.
With all viewpoints accounted for, architects are no longer forced to work in a vacuum to design a solution that needs to be successful in reality. Simulation data can move beyond simple clash detection to feed the model with fabrication equipment constraints, construction site limitations, and so on.
Continuous integration allows for the development of a virtual project to serve as an extension of reality for all stakeholders. A virtual twin creates a world where the entire building process can be rehearsed before committing to a design.
CASE STUDY
A data-driven design process delivered a gold-medal performance for the US Olympic Museum
MG McGrath Architectural Glass & Glazing is a nationally recognized façade company based in Minnesota. Upon securing a contract for the United States Olympic Museum in Colorado Springs, MG McGrath needed to accelerate its design-to-fabrication process to support the production of a large quantity of complex panel.
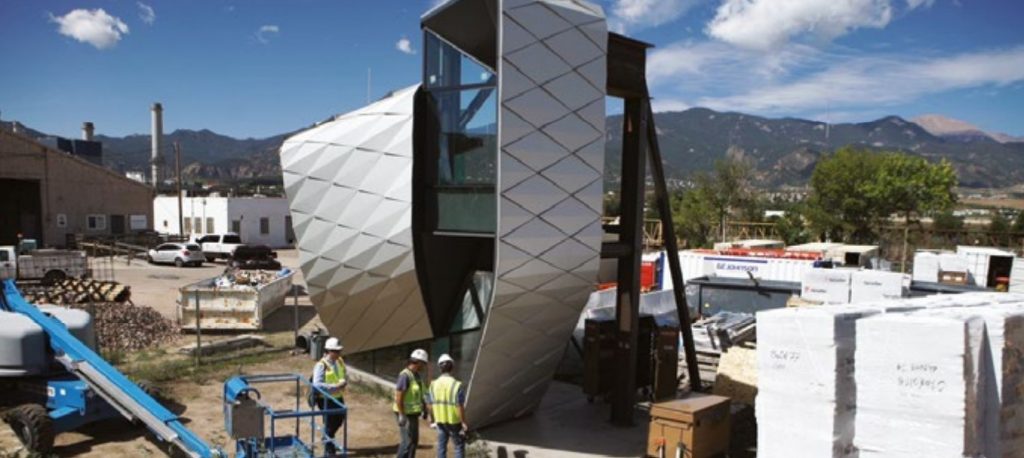
By implementing the 3DEXPERIENCE platform, the company streamlined its virtual design and construction (VDC) process and realized a range of benefits:
Speed. “An advantage to using the platform is the ability to automate our processes, which strips out a lot of the repetitive work,” notes Michael McGrath, president of the architectural surface design firm. For example, instead of modeling 10,000 pieces by hand, CATIA Template Designer on the 3DEXPERIENCE platform performs repetitive tasks for them.
“We used to spend hundreds of hours manually laying out complex pieces or components on the shop floor. Today, we can do the same thing in just a few hours. We can quickly provide feedback as it relates to constructability of different sorts of geometries and surfaces because the software allows us to analyze the geometry to a more granular level,” McGrath says.
Control. “We’ve shortened the amount of time spent during fabrication by providing the shop floor with 3D models that are clearer and easier to understand than text-based documents,” says Neil Meredith, VDC associate at MG McGrath. “A lot of time and effort goes into making very clear documentation. However, providing the actual models to the shop floor allows those fabricating and assembling components to easily understand how they’re put together.”
Flexibility. “Once a process or a workflow is automated, we can make changes quickly because we’re not worried about throwing out or losing that work,” Meredith says. “We are confident that we can get the same results we need for fabrication and construction thanks to the automated process.”
Scalability. MG McGrath designers save time and retain knowledge by creating templated components to be reused and adapted in future projects. “It’s not just one template for a specific challenge but a solution for several challenges that we’ll encounter in years to come,” McGrath says. “The 3DEXPERIENCE platform has allowed us to offer more custom solutions at a much more affordable price.”
Excerpted from DFMA for Construction: The 4 Perspectives Shifts Enabling Scalable Urban Development, a Dassault Systèmes whitepaper
Download our free whitepaper to learn more.
DfMA has the potential to transform the construction industry. This transformation will gain traction as project stakeholders increasingly discover the cost and time savings DfMA offers.
Shifting to modular assemblies demands an initial investment in time spent reengineering processes and the tools and equipment needed to support new components. Companies that
lead the change will see greater long-term benefits than those who try to catch up on the later side of the adoption curve.
Related links:
Dassault Systèmes Construction, Cities & Territories Industry