None would argue that automotive crash testing is important. According to a recent press release by the National Highway Traffic Safety Administration (NHTSA), traffic deaths spiked in 2015, with more than 36,000 people losing their lives on US roadways, and another 2.44 million injured. Although autonomous driving should substantially reduce accidents, safety standards and crash performance will remain critical development factors.
Yet crash test dummies are expensive. So too are the smashed cars, the proving grounds and test facilities, and the salaries of those who spend their days deliberately wrecking automobiles. These are just a few of the reasons why automakers want to make vehicle crash testing as efficient as possible, reducing the number of test crashes required during vehicle development while still providing accurate results.
Thanks to some really cool software and very powerful computers, automakers are beginning to do just that. By partnering with companies such as Dassault Systèmes SIMULIA, provider of the Abaqus FEA software suite, OEMs are reducing product development costs while increasing safety, without the sound of breaking glass or crumpled metal.
Physical Crash Test Constraints But how does crash testing work, and how can any software system possibly simulate what happens when a vehicle hits another object at disastrous rates of speed? Frontal impacts, roll-overs, small and moderate overlaps—literally dozens of tests exist, each of which involves slamming a vehicle into poles, barriers, other cars, and even people (don’t worry, they’re not real).
This dramatic event is recorded by high speed cameras, monitored by hundreds of sensors mounted to the vehicle and its faux inhabitants, and the results carefully analyzed post-mortem by skilled engineers. In 2013, the Texas A&M Transportation Institute announced that it had run more than 3,000 such tests to date, each one costing roughly $50,000 to perform. That’s $150 million in testing expense for this one facility alone, costs that invariably trickle down to vehicle consumers.
Nor are these tests perfect. According to the Insurance Institute for Highway Safety (IIHS), not all vehicles are tested, and the safety ratings of those subjected to recalls are not reevaluated. And while these tests produce a wealth of information, they can only be performed once—after the car has been destroyed and its secrets uncovered, the sad, twisted mass is issued an “unrepairable” certificate and hauled off to the scrap heap for recycling.
Toward Virtual Testing to Zero Prototyping
But these and other facilities are turning to more elegant testing solutions. For example, the Center for Collision Safety and Analysis (CCSA) at George Mason University in Fairfax, VA works with automakers and government agencies alike to augment real world crashes with virtual ones, using sophisticated software to model vehicles, obstacles, and crash test dummies and predict how each will fail on impact.
Automaker Honda is doing similar work. In collaboration with Dassault Systèmes’ 3DEXCITE, the two companies have developed a crash test simulation tool based upon 3DEXCITE’s DELTAGEN that “delivers a highly-realistic display of 3D visualizations with real-time interaction.”
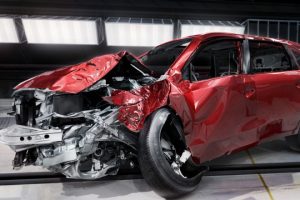
The potential benefits of such tools are huge. Simulations can be run over and over again—once the vehicle model has been developed, the only cost to crashing it is computer and analysis time. Simulations can be sped up, slowed down, attempted from different angles and under different driving conditions. Want to crash into an oak tree instead of a concrete barrier? Simply model whatever object is needed and crash away.
Perhaps most important to automakers is the ability to test multiple iterations of a vehicle while it’s still under development. A concept known as zero prototyping, it allows designers to virtually test 3D models of their wares, avoiding the tremendous expense of manufacturing not-ready-for-prime-time cars and trucks only to crash them, see what happens, and then start again. Worse, these prototype vehicles don’t always mimic the final product, potentially costing millions in rework.
This situation was avoided recently at BMW, which used Dassault Systèmes’ SIMULIA suite to test its Gran Coupe series. According to a 2015 company case study, “Confidence in the final design eliminated the usual soft tooling stage for prototyping, so that BMW Group could proceed directly to series production with hardened production tooling. Physical crash test results from these early series production vehicles closely matched the simulation predictions.”
Physical testing will never be eliminated, but there is a bright light at the end of the crash testing tunnel. Virtual tools like these promise to greatly reduce vehicle development costs, an important achievement for manufacturers and consumers alike. Better yet, the ability to repeatedly crash cars in a virtual world (and far less expensively) allows for more testing, in turn producing safer vehicles, less warranty issues and lower costs for all.