Over the last decade, the construction industry has come to terms with the need to make significant changes. Most major players have taken steps to improve efficiency, borrowing lessons from manufacturing industries and adopting digital design, off-site construction and prefabrication strategies. However, there are critical differences between high-volume, mass-production, industrialized manufacturing and one-off, hyper-customized, large-scale construction projects. These differences demonstrate the need for an altogether new approach to construction delivery.
Lessons from the Industrial Revolution
Until the Industrial Revolution, craftsmanship was the sole solution for creating goods, including buildings. Each product was developed by hand, with the potential for quality to vary across goods produced.
THE TRAJECTORY OF PRODUCTION STRATEGIES THROUGH THE INDUSTRIAL AGE
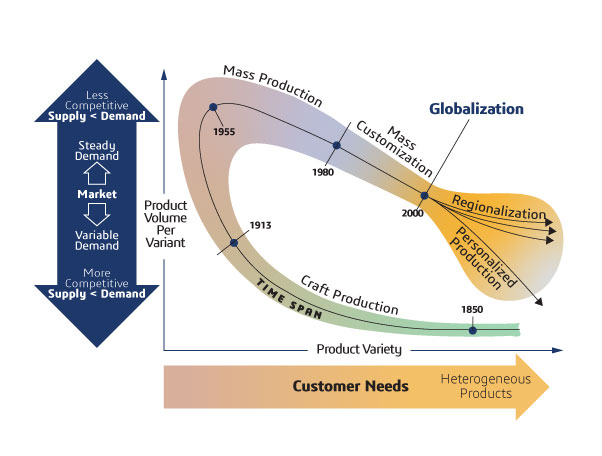
With the advent of the Industrial Revolution, manufacturers were able to mass-produce goods to satisfy demand with a high volume of products. The tradeoff is that mass production relies on component standardization and limited product variety to achieve cost efficiencies. This standardization at high volumes removes any opportunity for personalized production.
Manufacturers of mass-produced goods are now beginning to navigate this challenge as they recognize the limits of industrialization in their own context. The emergence of Industry 4.0 is meant to support manufacturers in harnessing data to drive greater flexibility in production processes and the mass customization of goods.
From Mass Production to Personalized Construction
It is often said that the construction industry has been slow in boosting its productivity. Globally, “labor-productivity growth” in construction has averaged only 1% per year over the past two decades compared with 3.6% in manufacturing. To be fair, the needs of the construction world are in direct opposition to the standardization that has driven the massive gains in manufacturing productivity.
An automotive manufacturing process may demand an investment of €1 billion in equipment and processes, which is recouped through a high volume of standardized goods. These processes would also harness the contribution of as many as 3,500 suppliers. Through the use of a digital twin, the factory might produce 30 to 50 vehicles each hour.
Construction players pushed to mimic the efficiencies of manufacturing have long recognized the drawbacks of mass production. The construction industry operates on a project-by-project basis within a fragmented and localized ecosystem. Each project faces unique site constraints and is customized to meet an owner’s specific demands. Each project is delivered by a team of tradespeople who may be operating together for the first time.
To date, technology has not yet addressed the realities of fragmentation, localization and the need for personalized production in construction. However, sustainability goals, increasing project complexity and technological advancements are opening the door for innovation and transformation. While the construction industry can learn from the efficiencies of high-volume manufacturing, its unique challenges demand a different approach to achieve creativity and scalability.
This article is excerpted from THE PRODUCTIZATION EFFECT: How integration-ready modules will transform the roles of general contractors, specialty contractors and the entire construction value chain. This white paper maps the path to productization and defines how general contractors, specialty contractors and the entire construction value chain can leverage virtual twins on an end-to-end collaboration platform, transcend the limitations of classic industrialization and leapfrog to personalized construction.
Download The Productization Effect
RELATED LINKS
- Dassault Systèmes Construction Solutions
- Dassault Systèmes Building Solutions
- Reinvent the Construction Industry With Productization
- Integrated Built Environment for collaboration& project management
- Building Design for Fabrication for digital continuity
- Build Smarter and Greener for Sustainable Construction