Indoor Air Quality and Air Filters
With increasing emissions, risks of pandemics and rising population globally, vehicle air conditioning units are not only responsible for our comfort anymore; they also ensure our safety.
Air quality inside the vehicle cabin depends on the surrounding air and the Heating, Ventilation and Air Conditioning (HVAC) unit performance. According to some studies, as much as half of the pollutants inside the car come directly from the vehicle ahead; furthermore contaminants released by sick occupants or even taken in from the surrounding air are becoming a growing concern. The HVAC unit must ensure that all occupants are kept safe whilst meeting performance and efficiency imperatives – with regulations requiring a full redesign of the HVAC to reduce polluting refrigerants use by 80% by 2047. This is a big challenge for vehicle Original Equipment Manufacturers (OEMs) and their suppliers, and they are looking into several ways to improve the HVAC and air filter performance to provide clean air with reduced contaminant spread inside the cabin. This must be done without considerably increasing manufacturing costs or affecting passenger experience.
The air filter is one of the most important but underrated components in any vehicle heating and cooling HVAC system. The filter is often located behind the glovebox inside the HVAC unit. It traps the airborne debris entering the vehicle HVAC unit, thereby providing clean cabin air and protecting the HVAC equipment. There are many types of air filters available in the market. Not all air filters clean with the same level of efficiency. Depending on the level of clean air required, the incoming air travels through one filter with higher efficiency, or through several filters. An example of contaminant removal process is shown in Figure 1.

The Minimum Efficiency Reporting Value (MERV) often determines the efficiency of the filter and its performance. It defines the air filter’s ability to block particles between 0.3 and 10 microns. MERV ratings are from 1 to 16 with higher values indicating higher particle trapping efficiency. In vehicles, High Efficiency Particulate Air (HEPA) filters are widely used. As per the government regulations, HEPA filters must remove 99.97% and 99.95% of contaminants in the US and Europe, respectively. Figure 2 shows different contaminants filtered by HEPA filters with different MERV ratings.
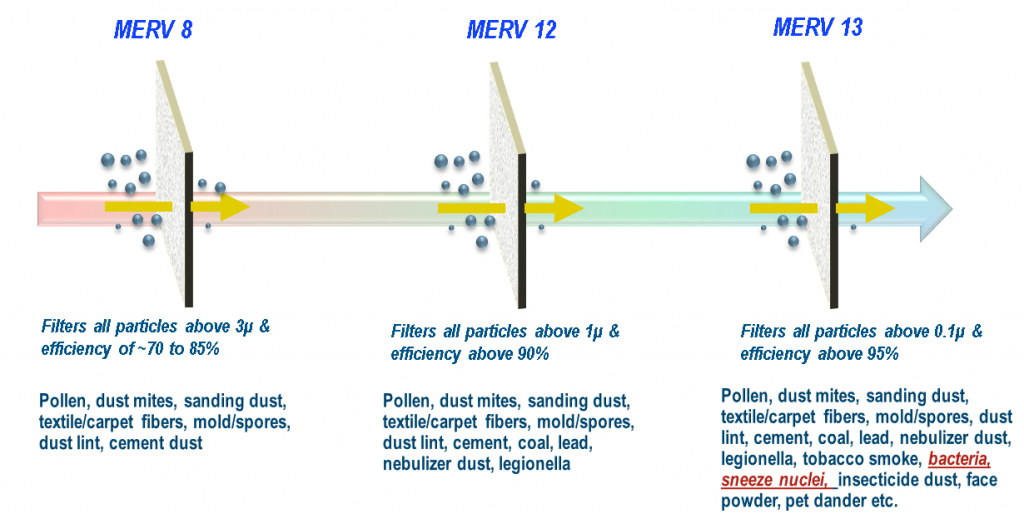
Challenges Faced by OEMs and Solutions with SIMULIA Tools
OEMs face the challenge of designing vehicle cabins of varying sizes whilst minimizing cabin air cleaning time. This needs to be done in the early design stage, as there is little flexibility in changing the design in late production stages. This challenge can be digitally addressed by modeling the detailed behavior of the filter, and its impact on flow performance, thereby evaluating the transport of contaminants, filter efficiency, filter life and contaminant removal inside the cabin within a reasonable turnaround time. SIMULIA solutions help to replicate real world scenarios to improve cabin air by virtually testing different filter designs and cabin configurations. Simulation also provides insights on the impact of fan position, filter changes and clogging on aerodynamics, thermal and acoustic comfort, and energy efficiency. Figure 3 shows SIMULIA vehicle filter design modeling capabilities.
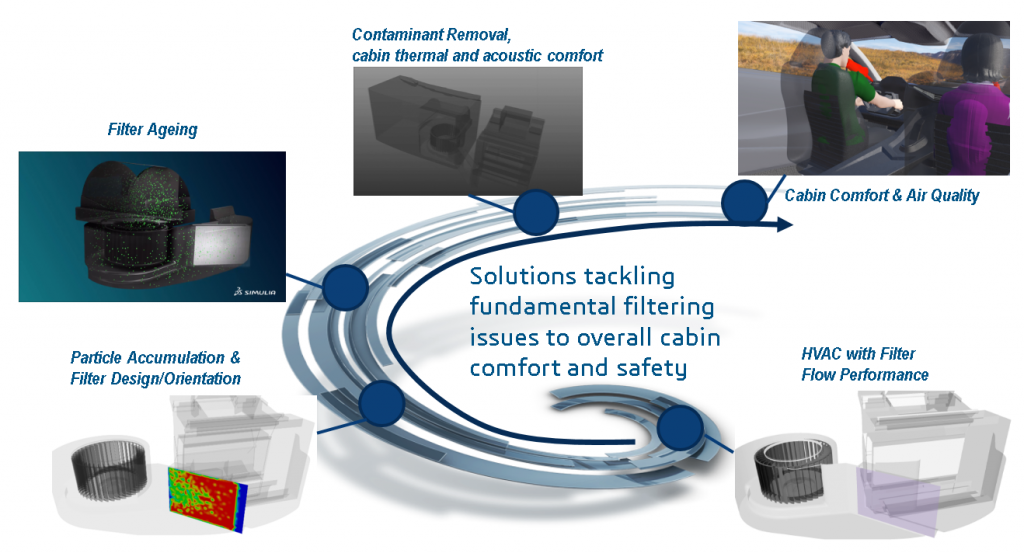
Simulation Geometry and Methodology
The number and placement of air filters in an HVAC unit varies; OEMs like BMW can have two air filters, sometimes placed before the blower, and other OEMs like TATA or Valeo have one air filter placed after the blower. The placement of the air filter before and after blower affects the pressure drop, flow resistance, contaminant accumulation and filter efficiency. This can all be modeled in simulation, including the effect of variations of the filter properties, as shown in Figure 4.
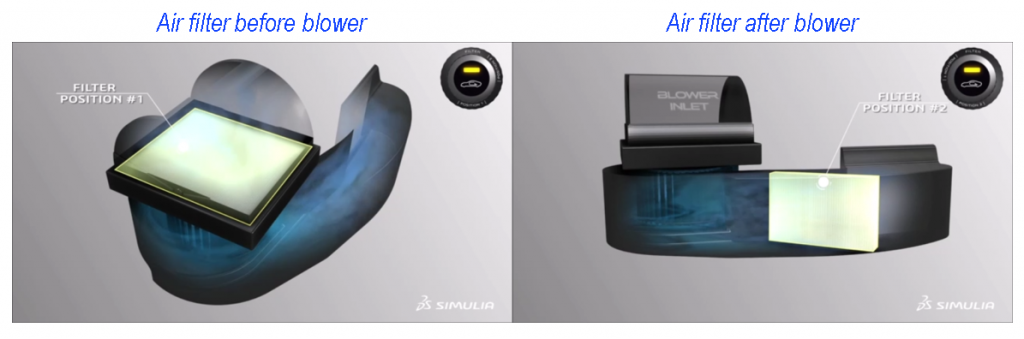
A highly accurate and inherently transient Lattice-Boltzmann-based PowerFLOW solver with Particle Modeling is used to model the flow behavior, contaminant transport, accumulation on the air filter and pressure drop for different filter ratings and positions. The filter design simulation is integrated into our cabin comfort simulation framework. In the HVAC simulation, the contaminants are injected into the system through a prescribed boundary condition. The filter is modeled as a particle screen which controls the particle opening size and pass through fraction for different filter types and ratings. It provides the user with insights about filter/system efficiency and models the effects of clogging from contaminant accumulation either uniformly or non-uniformly. Figure 5 shows the HVAC geometry with particle screen and flow path:
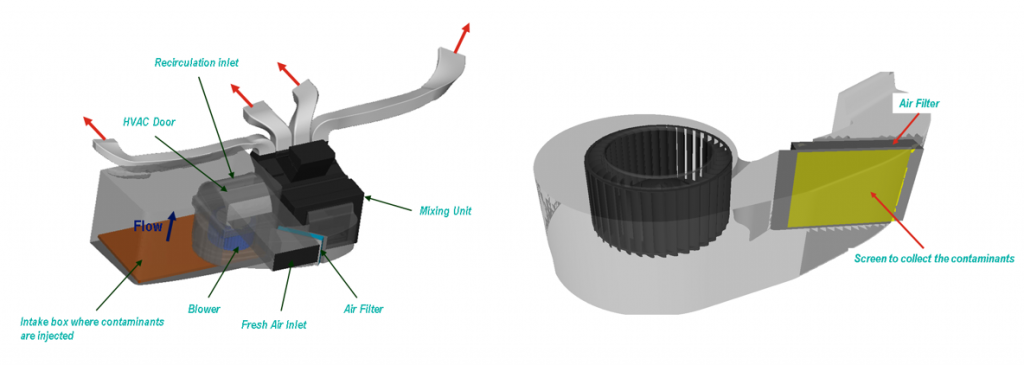
Simulation Driven Design
Designing a filter involves a careful balance between imposed pressure drop and filter efficiency. Flow behavior in general is affected by the accumulation of particles on the air filter. Coarser filters like MERV8 will let more particles through, but last longer between replacements and require less powerful blowers – thus reducing energy consumption. The filters must also be positioned in such a way that their surface area is facing the flow. Figure 6 shows the example of flow behavior for filters placed before and after the blower. For filter placed after blower, only a part of the filter is facing the flow due to angled shape of the casing, and hence more flow is concentrated on one side. For the filter before the blower, the flow spread around the filter remains uniform.
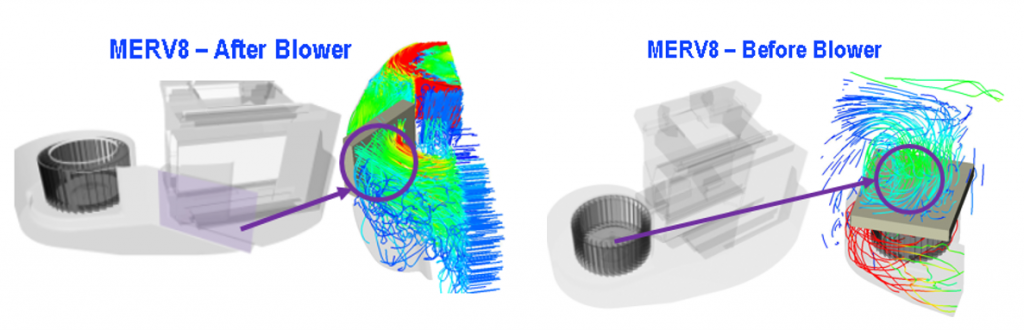
Choosing the right filter rating is also important when balancing performance. Higher rating finer filters like MERV12 and MERV13 block more particles and are more efficient, but will require a more powerful blower and will clog up more easily. Less flow is seen passing through the filter due to a higher pressure drop imposed by the filter, and more accumulation. Flow distribution with fine filters is shown in Figure 7.
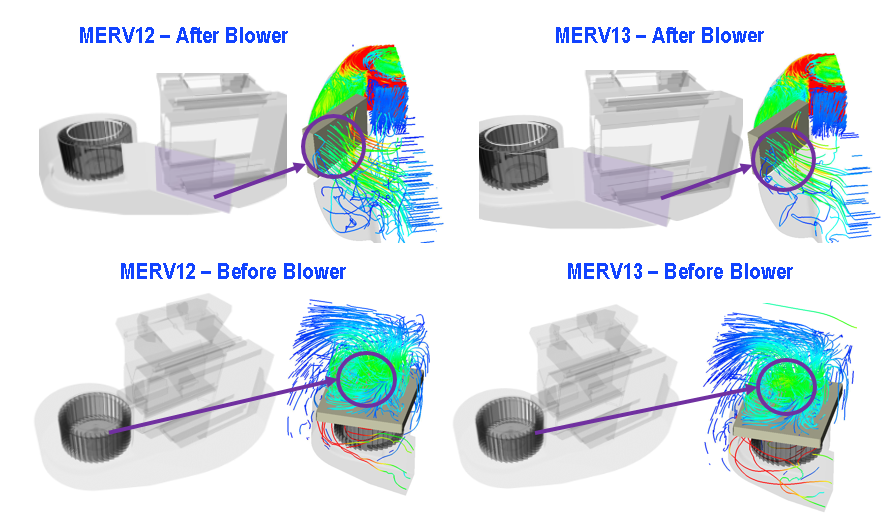
Contaminant accumulation on the air filter provides information on its replacement lifecycle, effective placement of the filter and efficiency of the system. In the inclined air filter placed after the blower, lifecycle and efficiency of the air filter are low due to asymmetrical accumulation of contaminants; they also deposit on the blower thereby introducing the need for frequent cleaning of the blower. This type of inclined filter design as shown in the system of Figure 8 suffers from significant drawbacks, and is thus not recommended for real life usage.
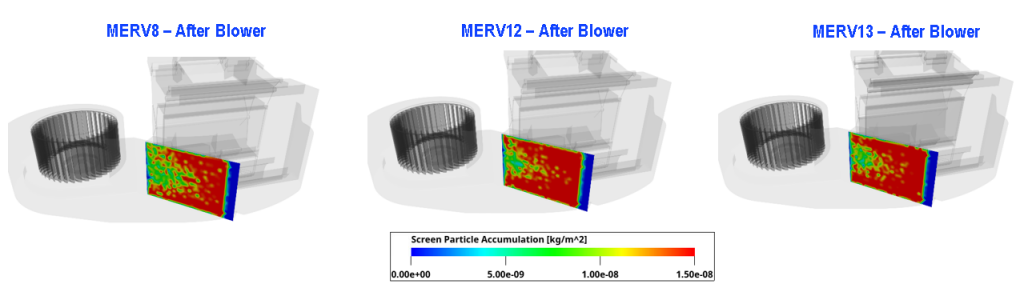
When the air filter is positioned before the blower, the contaminants are accumulated in the center and gradually increase towards the sides. Though flow resistance and pressure drop increase with higher MERV ratings, no asymmetrical accumulation occurs. This type of filter design shown in Figure 9 indicates increased longevity as the full surface area of the filter is effectively used.
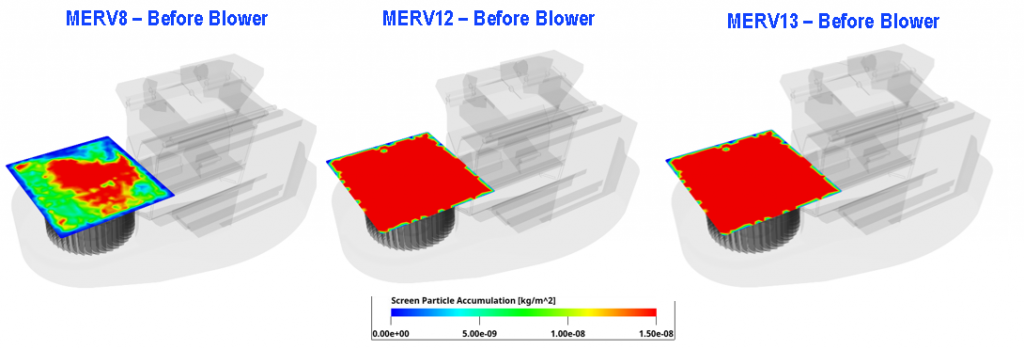
Figure 10 shows the amount of particles that pass through the filter with different MERV ratings. The efficiency and air quality will be high for high rated fine filters but the flow resistance will also be higher, resulting in higher energy consumption, and frequent replacement of filters.
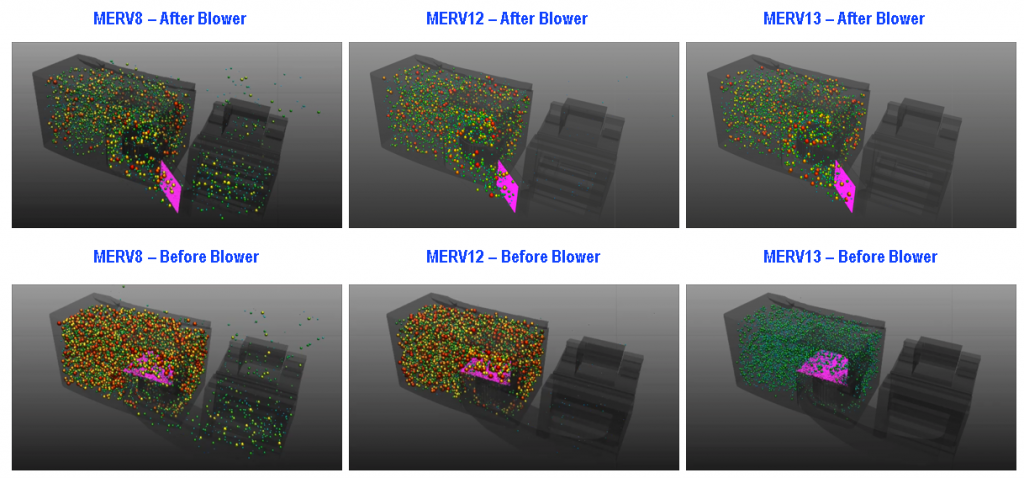
Simulation can also predict the particle age, which indicates how quickly a contaminant can be removed from the system. Here the particle age of the contaminants is around 1 to 2 seconds. If the HVAC is operated over a long period of time, the simulation can be used to verify that a vast majority of particles are captured by the filter. This provides information about the overall HVAC filtering efficiency, as shown in Figure 11, for different MERV ratings and installation configurations.
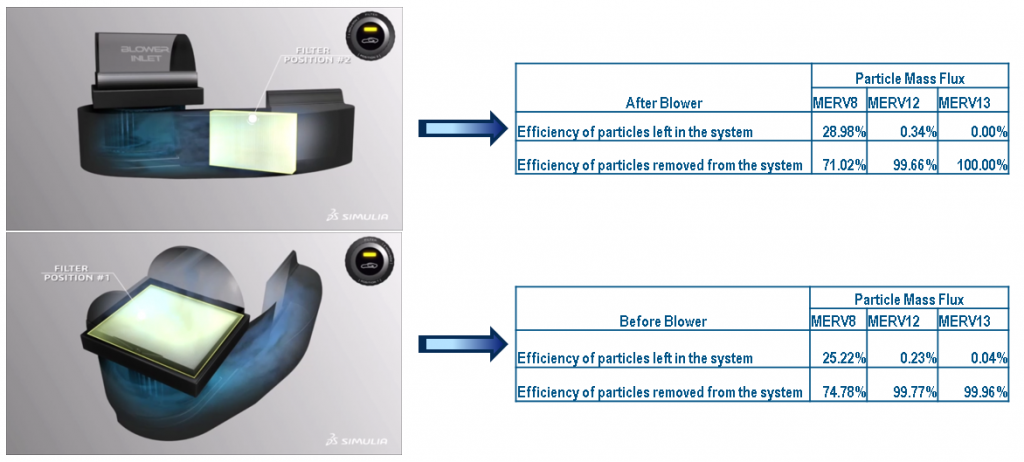
Time taken for contaminant removal inside the cabin is predicted by modeling the detailed cabin, including breathing occupants, to assess real life filter removal rates. An initial flow simulation is carried out until the flow is stabilized inside the cabin. A global Velocity Freeze simulation with scalar transport model is then used to predict the contaminant removal rate and time taken for contaminant removal inside the cabin. Driver and passenger breathing rates are specified in terms of contaminant emission. Initially a negligible amount of contaminants is introduced into the cabin through the vent inlets. During the simulation, the contaminants leave the cabin through the recirculation outlet and they are recirculated back into the cabin through the vent inlets. Depending on the type of the filters selected, the percentage of contaminant removal rate with time is modeled in the simulation. Initially the cabin will have contaminants from infected occupants or from outside. During the simulation, the heavier contaminated particles settle on the surfaces. The lighter aerosols circulate inside the cabin; some of them reach the recirculation outlet. They then pass through the HVAC filter where the contaminants are accumulated or filtered and clean air enters the cabin through the HVAC vents. This process is carried out until most of the aerosols are filtered thus allowing fresh and clean air into the cabin. The position of HVAC filters and outlets is important since it plays an important role in faster removal of the contaminants. Aerosols circulating in low flow, damp areas are trapped and continue to circulate there for a long time. Simulation helps in providing insights and guidance to select the appropriate filters, their placement, age, time taken to remove contaminants and achieve clean air inside the cabin.
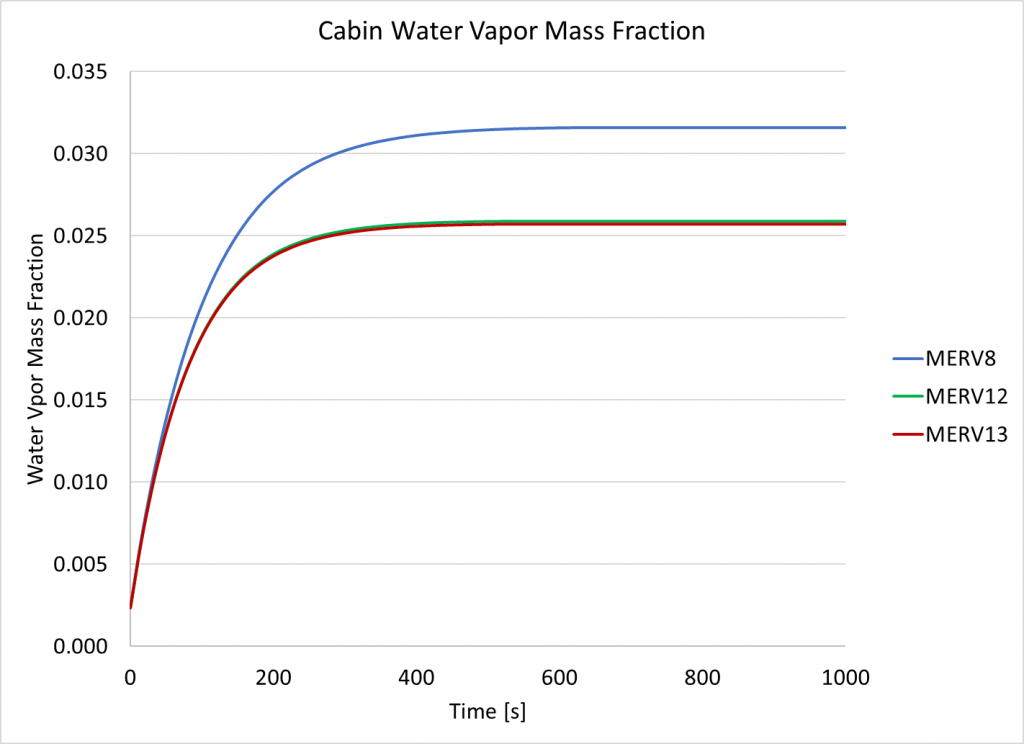
As seen from the Figure 12, contaminants are higher with MERV8 compared to MERV12 and 13. Most of the heavy particles are filtered and only lighter aerosols are recirculated inside the cabin. Aerosol spread will decrease and become negligible over time with fresh & partial recirculation mode.
Conclusion
The HVAC filter design methodology presented here shows SIMULIA PowerFLOW’s capability to model the transport and filtering of contaminants with different filter configurations. Flow performance as well as air quality performance of the HVAC can be assessed in detail and improved concurrently. The placement of filters can be optimized to increase maintenance intervals, minimize cabin cleaning time and improve overall interior air quality. The filter can be integrated and its properties tuned to maintain optimal HVAC performance for thermal and acoustic comfort, as well as energy efficiency. The time taken to remove the contaminants inside the cabin and percentage rise or fall of contaminants with time inside the cabin can also be predicted to ensure safety of occupants.
SIMULIA solutions enable you to overcome new challenges around cabin air quality, whilst maximizing the comfort of passengers, and the energy efficiency of your vehicle.
Want to connect with other HVAC experts and access HVAC resources? Visit the HVAC overview page in our SIMULIA Community to start exploring.
SIMULIA offers an advanced simulation product portfolio, including Abaqus, Isight, fe-safe, Tosca, Simpoe-Mold, SIMPACK, CST Studio Suite, XFlow, PowerFLOW and more. The SIMULIA Community is the place to find the latest resources for SIMULIA software and to collaborate with other users. The key that unlocks the door of innovative thinking and knowledge building, the SIMULIA Community provides you with the tools you need to expand your knowledge, whenever and wherever.