This article was first published in REVEAL Magazine Issue # 3.
In recent years, the US Department of Defense (DoD) has accelerated efforts to modernize existing reentry systems and develop new high-speed flight systems to counter significant advancements in hypersonic technology made by other nations. The term hypersonics generally refers to flight systems that travel at speeds greater than Mach 5—five times the speed of sound, or about a mile per second. The extreme environment of hypersonic flight requires that systems survive a much wider range of temperatures (70–5000+ °F) and pressures compared to traditional flight systems. Due to these challenging aerothermal conditions and the interdependent physical phenomena, time- and labor-intensive analysis and testing efforts are required to validate flight-critical components and the advanced aerospace materials from which they are made.
Currently, the US Navy is developing the next generation of strategic seaborne systems and hypersonic platforms, a process demanding innovative solutions to complex problems that include the design, characterization, qualification, and ground and flight testing of hypersonic system components. The Navy Strategic Systems Programs (SSP) and the Office of Naval Research (ONR) sought a numerical simulation approach using nonlinear finite element analysis (FEA) to perform modeling and simulation of candidate materials to be used in flight-critical components such as a thermal protection system (TPS).
Under a multi-year research effort culminating in a Small Business Innovation Research (SBIR) Phase III Rapid Innovation Fund contract, ATA Engineering, Inc., (ATA) developed COMPAS, a composite material modeling and simulation add-on for the Abaqus Unified FEA environment. COMPAS predicts the thermomechanical response (and associated statistical variability) of composites and improves modeling accuracy while reducing the reliance on today’s costly build/test paradigm for qualifying these advanced materials. In developing the COMPAS add-on, ATA leveraged many of the native modeling capabilities of Abaqus and integrated machine learning techniques to accurately and efficiently extract material properties from limited test data and to predict the nonlinear response of heat-resistant candidate materials when subject to thermomechanical loads.
ATA is an employee-owned small business headquartered in San Diego, California, providing analysis- and test-driven design solutions to support the engineering needs of customers and government agencies. ATA actively participates in the US SBIR/STTR Program to develop new engineering methods and tools, including this multi-year research effort to develop and validate COMPAS for use in computational characterization of the Navy’s candidate TPS materials as well as similar Air Force, Army, and NASA programs that have advanced COMPAS and Abaqus-based solutions over the past decade.
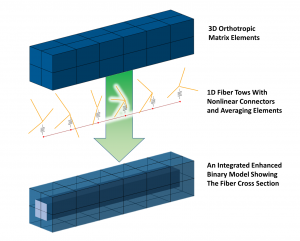
material architectures
TPS materials protect sensitive internal structures and components from the extreme conditions of hypersonic flight and the effects of aerodynamic heating, in particular. Engineers must ensure that a TPS design is capable of controlling erosion while minimizing heat transfer to the underlying structure, factors that, if not adequately addressed, could result in mission failure. Thus, TPS structures are fabricated from advanced heat-resistant materials, most often 2D and 3D woven carbon-carbon (C/C) composites, which are among the few suitable materials that can survive the demands of hypersonic flight. These advanced composites are orthotropic in nature and macroscopically heterogeneous, possessing irregular phase geometries and nontrivial degrees of porosity. C/C composites also exhibit extremely nonlinear progressive damage behavior with several damage and failure modes contributing to their aggregate performance across the very wide temperature range experienced from launch through flight.
Changes in raw material availability, along with the tremendous time and labor required to test and analyze new candidate composites, have complicated the design and manufacturing of TPSs for current and future highspeed flight systems. The need to replicate the severe thermal loads and other conditions of hypersonic flight make ground testing of these materials challenging and costly. As a result, material characterization test data is often very limited and not wholly representative of the damage encountered in the complex flight environment. To reduce the risk of failure during flight testing and to provide a more affordable means of virtual qualification of new TPS materials, the Navy sought an Abaqus-based solution in their call for innovative methods under SBIR topic N141- 082: Non-Linear Behavior Models for Design of Carbon-Carbon Composite Components.
ATA answered this call by developing COMPAS, which uses the nonlinear simulation capabilities of Abaqus and custom tools to extract material model coefficients (and associated scatter) from limited constituent material and mechanical test data to predict the response of novel TPS materials and component designs under thermostructural loading. Developed in the Python programming language, COMPAS is a modular package containing different modeling and analytical process flows, each with corresponding modules that guide the user through the process flow. The modules have graphical user interfaces (GUIs) associated with them that are accessed as Abaqus plug-ins for ease of use.
A key feature of COMPAS is a tool that automatically creates finite element models of arbitrary TPS architectures and part geometries using an innovative modeling formulation, the Enhanced Binary Model (EBM). The EBM is based on the Binary Model, which explicitly models individual fiber tows using 1D elements and the matrix-dominated material using 3D elements. These elements are rigidly connected in Binary Models to represent the composite material, and in the EBM, a nonlinear connector element between fibers and matrix additionally models the behavior of the fiber-matrix interface, as shown in Figure 1. Using built-in Abaqus material models, nonlinear constitutive behavior is defined for the fiber tow elements, matrix elements, and interface spring elements. Figure 2 shows the rapid setup of tensile coupon EBMs using COMPAS tools to support virtual testing of a 3D woven architecture.
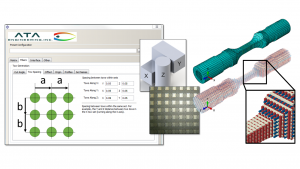
COMPAS leverages Abaqus to provide the user with two primary process flows the Material Model Correlation Process (MMCP), which is used to quantify mean values and corresponding statistical distributions of unknown material model parameters (e.g., directional moduli and strengths) by comparing predicted responses to measured responses that exhibit scatter, and the Multiscale Simulation Process (MSP), which enables the user to simulate responses across multiple length scales and capture the effects of local damage on the overall response of the structure. ATA has applied these tools to rapidly set up virtual test models, calibrate material model parameter statistics with limited data, and predict a variety of material responses and failure modes, including fiber rupture, matrix cracking, and fiber pullout, as shown in Figure 3.
ATA and other organizations have used COMPAS to accurately predict the thermomechanical response of a variety of C/C composites and ceramic matrix composite (CMC) materials, including orthogonally woven 3D materials. The availability of reliable material model parameters will accelerate the adoption of new material systems and foster more lightweight, capable, and affordable solutions for high-temperature composite structures, extending beyond TPS components to turbomachinery, propulsion, and nuclear power applications.
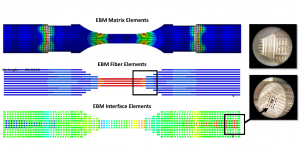
By making COMPAS available at no cost to US Government Abaqus users, ATA anticipates that the software will play a key role in supporting a key national security priority: leading the world in the fielding and sustainment of high-speed flight systems. ATA looks forward to continuing to support these organizations, their system integrators, and material vendors in applying
COMPAS and other Abaqus-based capabilities, such as the Co-Simulation Engine (CSE), in the development of next-generation hypersonic systems.
Learn more about ATA Engineering.
SIMULIA offers an advanced simulation product portfolio, including Abaqus, Isight, fe-safe, Tosca, Simpoe-Mold, SIMPACK, CST Studio Suite, XFlow, PowerFLOW, and more. The SIMULIA Community is the place to find the latest resources for SIMULIA software and to collaborate with other users. The key that unlocks the door of innovative thinking and knowledge building, the SIMULIA Community provides you with the tools you need to expand your knowledge, whenever and wherever.