Nature is many things—powerful, beautiful, destructive, and above all, intelligent. Plants and animals have developed some remarkable functions and adaptations. Beyond giving specific living organisms evolutionary advantages, some of these characteristics have inspired humans to build and create differently. Many researchers and inventors recognize the intelligence of nature and have taken ideas from it to design everything from Velcro to skyscrapers. This approach of taking ideas from nature is known as biomimicry, and it is responsible for some remarkable innovations.
Most people have heard of the pufferfish, and likely have a rather comical image of it—the fish absorbs water to swell its body to a much larger size when threatened, and then releases the water to return to its normal size when the danger has passed. While this is amusing to picture, and indeed has been depicted as so in cartoons, the behavior is serious business to the pufferfish, which relies on its expanding capabilities for its survival.
Humans in developing countries may soon owe their own survival to the behavior of the pufferfish. A recent Princeton University study took inspiration from the pufferfish to develop a novel method of water purification. Postdoctoral researcher Xiaohui Xu and Vice Dean for Innovation/Pomeroy and Betty Perry Smith Professor of Chemical and Biological Engineering Rodney Priestley developed a gel sponge that, when placed in water, soaks up the water but leaves contaminants behind. The sponge can then be placed in sunlight, where it releases the purified water.
The innovation could potentially be used to provide clean water to areas with little or no access to electricity or water purification technology. Xu and Priestley state that their technology delivers a higher passive solar water purification rate of any competing methods, and the gel can be used repeatedly, remaining effective for at least 10 cycles of soaking and discharge.
Contaminants that the gel is capable of removing include petroleum and other oils, heavy metals such as lead, small molecules, and pathogens such as yeast.
The gel consists of a highly porous honeycomb-like structure composed of long chains of repeating molecules known as poly(N-isopropylacrylamide) that are cross-linked to form a mesh. Within the mesh are both hydrophilic and hydrophobic regions. At room temperature, the chains are long and flexible, allowing water to easily flow into the material via capillary action to reach the water-loving regions. When the sun warms the material, however, the hydrophobic chains clump together and force the liquid out of the gel.
Two other layers surround the gel, keeping contaminants from reaching it. A dark-colored material called polydopamine forms the middle layer and transforms sunlight into heat while also keeping out heavy metals and organic molecules. An external layer of alginate blocks pathogens and other materials from entering the gel.
Xu, Priestley, and fellow contributors Sehmus Ozden, Navid Bismark, Craig B. Arnold, and Sujit S. Datta published their study in the journal Advanced Materials.
Another recent study, conducted by researchers at Australia’s University of the Sunshine Coast, involved the development of a climbing robot that mimics the movements of a lizard. The team hopes that their research will inspire next-generation robotics design for disaster relief, remote surveillance, and even space exploration.
Lizards, through years of evolution, have optimized their movement across difficult terrain. The researchers studied them for four years and concluded that the reptiles had practically perfected their movement for speed, stability and efficiency.
One surprise that the researchers discovered was that a lizard’s claws or sticky pads (in the case of a gecko) do not need to align with the direction of the creature’s climb. In fact, the lizard’s front feet rotate 20 degrees and its rear feet rotate 100 degrees. These discoveries could contribute to a formula for robotics optimization.
The study was published in the journal The Royal Society Publishing.
SIMULIA’s solutions have played a role in some other important biomimicry research, notably the work of Purdue University Professor and SIMULIA Champion Pablo Zavattieri. Professor Zavattieri is the director of the Multi-Scale Mechanics and Materials Design Lab at Purdue, and his research has included the study of some other invertebrates such as the mantis shrimp and the diabolical ironclad beetle.
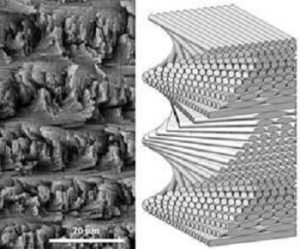
Zavattieri uses Abaqus to perform structural simulation to investigate hypotheses involving biological materials inspired by these and other creatures. The mantis shrimp, for example, has extremely strong, tough, and fast-moving club-like front limbs that it uses to pummel prey or attackers. These clubs are formed with a helicoidal or “Bouligand” structure, which includes slightly twisted layers consisting of multiple fibrils in a mineral matrix. Each fibril is made up of multiple proteins.
Zavattieri and his lab use multi-scale simulation to capture the behavior of the materials at each level and to study why the structure is so strong, as well as how cracks propagate through the surface. They can then 3D print composites with the same structure and conduct experiments to verify the failure mode identified by the simulation and the best selection of synthetic materials to substitute for the biological minerals and proteins.
The mantis shrimp’s helicoidal architecture is currently being applied to carbon- and glass-fiber reinforced composites. Zavattieri and his lab are also working on the 3D printing of cement using the types of architectures found in mantis shrimp, lobsters and crabs, and are seeing an increase in toughness.
The diabolical ironclad beetle is another astonishing creature, with a shell that can withstand the weight of a car. The beetle’s wing cases are made up of layers of chitin in a protein matrix, fused together by a complex, jigsaw-puzzle-like interface. This puzzle architecture allows for extreme toughness without reducing strength.
If the interlocking blades in the geometry were only slightly curved, the parts would pull apart; if they were sharply curved, the neck of the blade would snap. A curve somewhere in between resists both failure modes. Zavattieri’s group used simulation to test different puzzle geometries to find the optimal curvature for the puzzle architecture, which could potentially be used to join two different materials without welds or chemical bonds.
You can read more about the work of Zavattieri’s lab here, or read the full SIMULIA case study here.
These are just a few recent examples of how biomimicry can improve materials, create new robotics applications, and even potentially save lives. It takes work to adapt nature’s creations for human use, however, and simulation can make that work more effective by providing a means of evaluating and testing these innovations.
SIMULIA offers an advanced simulation product portfolio, including Abaqus, Isight, fe-safe, Tosca, Simpoe-Mold, SIMPACK, CST Studio Suite, XFlow, PowerFLOW and more. The SIMULIA Community is the place to find the latest resources for SIMULIA software and to collaborate with other users. The key that unlocks the door of innovative thinking and knowledge building, the SIMULIA Community provides you with the tools you need to expand your knowledge, whenever and wherever.