Many people are familiar with the television show ‘Friends,’ and for some not a day goes by without having watched an episode of this sitcom. In one of the more humorous episodes, the character Joey Tribbiani complains that his car has broken down, only to report back that his car doesn’t have a transmission anymore! For the Friends trivia enthusiasts, it’s in episode 7 of season 4. And while most of us are not prone to such monumental gaffes, it does go to show how neglected the role of the transmission system is, despite being one of the most vital cogs in virtually every industrial application.
In recent times, environmental sustainability has become a key driver of government and corporate policy decisions. The European Union has taken a lead on this, and its low carbon economy roadmap has set a target of reducing greenhouse gas emissions to 80% below 1990 levels, by the year 2050. As a result, the role of the automotive and industrial equipment industries in reducing the carbon footprint is increasingly in the spotlight. As per EU regulations, the target for heavy machinery is to reduce CO2 emissions by a massive 30% by 2030. The automotive industry also requires an average reduction of 30% in CO2 emissions by 2030, compared to 2021 emission levels. The efficiency of the transmission system will play a vital role in achieving these targets.
Another driver for a renewed focus on transmission systems is the pace of product development. One reason is the rapid shift towards electrification, which has led to a need for compact and lightweight gearboxes. This requirement dovetails with the second reason, which is the need for higher reliability of gearboxes to reduce failure risks and avoid downtime. A study by Caterpillar Inc. suggests that idle time due to repairs ranges between 400 to 800 non-productive hours and an average repair costs around $1,560-$3,120, per machine per year.
Optimizing the lubrication in gearboxes to reduce oil-induced drag torque can lead to a significant improvement in energy efficiency, as high as 10% or more. However, nearly one in every five failures in heavy machinery is a result of inadequate lubrication in the transmission system. Analyzing lubrication systems can thus be highly rewarding, but also requires careful analysis!
3DEXPERIENCE Platform
Dassault Systèmes’ 3DEXPERIENCE Platform has a host of tools that are well-suited to the analysis of lubrication in transmission systems. To begin with, the platform acts as a repository for all the geometry and simulation data for seamless data management. In addition, it has tools such as CATIA, a class leading CAD software, which allows the user to create parametric geometry and also filter and clean it up for downstream processes.
Integrated Modeling and Simulation – MODSIM
The 3DEXPERIENCE Platform allows for the integration of design and simulation tools, also referred to as MODSIM, enabling a more holistic design process. A key enabler for this approach is the Power’by functionality. This allows non-native simulation tools to be used on the platform natively, taking advantage of the platform’s project and data management capabilities.
The tool used via Power’by, for the assessment of the lubrication system performance, is SIMULIA XFlow. It is a state-of-the-art computational fluid dynamics (CFD) software based on the Lattice-Boltzmann method. It uses a fully Lagrangian approach on top of an underlying computation lattice which makes it extraordinarily tolerant to the quality of the design geometry.
One can easily import the geometry into XFlow directly from the platform via the Power’by connector.
As a consequence of its approach, XFlow reduces the geometry modification and cleanup required, which is generally one of the biggest hurdles in such an analysis. However, XFlow does include some tools that allow the user to make some geometry modifications, such as an automated hole-detection and fixing tool, without having to switch to a native CAD tool.
Ease of Setup
A CFD engineer’s job must revolve around post-processing simulation results and identifying insights that can lead to meaningful design improvements. Therefore, the less time spent in pre-processing, the better. XFlow provides a few unique features that enable the engineer to be more effective. The first of these features is the ease with which motion can be assigned to the gears, and also verified within a few seconds. This functionality goes a long way in ensuring that the user does not make a simple mistake and ends up running the simulation with incorrect meshing gears.
The second productivity feature is the absence of a traditional computational mesh. The XFlow solution relies on a Cartesian lattice that is generated by the software via an automatic algorithm directly during run-time, based on a single refinement input from the engineer.
The simulation can then be run directly via the platform, either locally or in a high performance computing (HPC) cloud environment. The setup can also be run externally on a different cloud. Usually, transmission system fluid simulations can be computationally expensive and could take on the order of weeks to run. However, this class of problems is particularly suited for XFlow and is highly scalable, reducing the turnaround time significantly.
For any CFD tool, validation is of paramount importance. We have worked with multiple partners across academia and the industry to validate this approach, including specifically for gearbox lubrication. Our tests have involved simple academic studies, as well as complex transmission systems. In fact, one of the biggest challenges faced with designing lubrication systems for gearboxes is the difficulty of physical testing. The violent sloshing that occurs inside permits very low visibility for the engineer, and insight about the oil slosh pattern must be gained through indirect observations, such as burnt out bearings. This also makes physical testing an expensive proposition, in terms of time as well as money. A validated tool like XFlow affords deeper insight at a fraction of the cost, and the speed of computation keeps it head and shoulders above the competition.
Take a look at the video below to see an example of how XFlow can help effectively visualize the flow of oil inside a gearbox.
We will now consider a particular gearbox designed for use in a piece of industrial equipment. Typically, post-processing revolves around quantities such as the drag torque acting on the gears and shafts i.e., the churning losses, and the total wetted area of the gears. These quantities can be plotted directly within XFlow using the inbuilt post-processing capabilities. It would also be worthwhile to note that the results can be exported to the 3DEXPERIENCE platform for visualization and to be further shared across the team.
A few observations can be made by looking at the Volume fraction (VOF) iso-surface for the oil. The first insight is that there is significantly more oil in the left half of the gearbox as compared to the right half i.e., the oil distribution is not balanced.
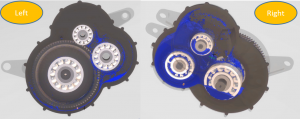
This is also reflected in the churning losses. The oil is almost absent in the right side, and therefore the churning losses in the gears on that side are very low, while the losses from the left hand-side are quite high.
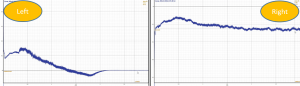
The second insight is that there is very little oil entering the oil collector. The collector is responsible for redistributing the oil across the two halves of the gearbox.

Design Optimization
One can now consider improvements to the existing design based on the insights obtained. The objective is to reduce the drag torque i.e., the churning losses, while increasing the wetted area. This has been achieved via a single change – transforming the orientation of the gearbox. This can be easily achieved via the transformation tool using the existing setup, and then run, all from within XFlow.
One can now take a look at the improved results. From the graphs, it can be seen that the churning losses have reduced by a fair amount, while the wetted area has also increased by a large margin.

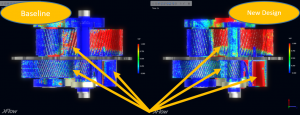
In addition, one can plot the VOF iso-surfaces again to look at the oil splash pattern. There is an increase in the oil being fed into the oil collector, which balances the oil distribution across the left and right-hand sides of the gearbox.
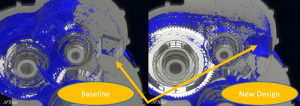
Conclusions
A comparison of the numbers shows that the design change has come with an improvement of 45% in the churning losses and 113% in the wetted area. These are huge improvements for a gearbox, and have been obtained without creating a single prototype. The promise of MODSIM is front-loading simulation to facilitate rapid design improvements via enhanced product insights. By reducing the number of prototypes and failure tests, one can achieve faster product development cycles at low cost. For transmission systems, the ability to consider design changes at an early stage allows for the exploration of a larger design envelope, the realization of a significantly better product and, hopefully, a cleaner environment.
See all our Transportation & Mobility solutions by visiting: https://www.3ds.com/products-services/simulia/solutions/transportation-mobility/
SIMULIA offers an advanced simulation product portfolio, including Abaqus, Isight, fe-safe, Tosca, Simpoe-Mold, SIMPACK, CST Studio Suite, XFlow, PowerFLOW and more. The SIMULIA Community is the place to find the latest resources for SIMULIA software and to collaborate with other users. The key that unlocks the door of innovative thinking and knowledge building, the SIMULIA Community provides you with the tools you need to expand your knowledge, whenever and wherever.