If you’ve ever been in a low humidity climate like the Northeast United States in the winter, you’ll be familiar with ESD – electrostatic discharge. This is the well-known phenomenon where your body builds up a static charge, perhaps from walking on a nylon carpet, and then rapidly discharges to the ground with a spark, usually by touching a metal door handle or railing.
This is an annoying and unpleasant experience, but not typically dangerous. However, ESD can be damaging and even cause explosions in industrial environments where volatile gases are used. It can also cause severe damage to electronic components in unprotected manufacturing environments or clean rooms. These types of environments are usually well protected by avoiding certain materials, controlling the humidity, and keeping workers attached to the ground so they cannot build up a charge. However, once components and devices are out of these controlled environments and in a consumer’s hands, they can be subjected to ESD via the phenomena we mention at the beginning. Imagine your smartphone is in your hand and unknown to you, charged up to the same level as the rest of your body. This time when you reach for the door handle the spark may jump between the handle and the metal case or a connector port on your phone. If not properly protected, your device may be ruined.
Due to how common an occurrence this is, electronics manufacturers pay very close attention to the susceptibility of their devices and how they can be protected. This has become even more important in recent years as lower operating voltages and reduced layer and junction sizes within integrated circuits have increased sensitivity. ESD may cause thermal-related damage, layer breakdown, or even electromagnetic interference causing signal or software failures.
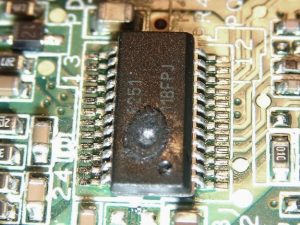
There are methods to improve ESD protection. For example, using Zener Diodes to shunt voltage spikes to the ground plane is one important technique to protect the device. The selection and placement of protection measures and then testing them under a range of environmental conditions are important steps in the overall design and certification process.
The IEC has defined testing various scenarios as shown in table 1. Soft failures are temporary and can be recovered. Hard failures are where permanent damage occurs.
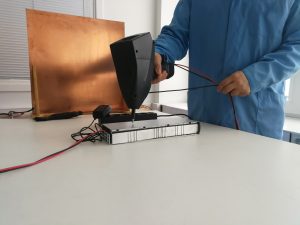
Test Item | Standard | Evaluation | ESD Source |
Electronic equipment | IEC 61000-4-2 | Soft failure
Hard failure |
Human body |
Automotive electronics | ISO 10605 | Soft failure
Hard failure |
Human body |
Electronic component | IEC 61340-3-1 | Hard failure | Human body |
IEC 61340-3-2 | Hard failure | Machine | |
Semiconductors | IEC 60749-26 | Hard failure | Human body |
IEC 60749-27 | Hard failure | Machine |
These standards define the circuitry used in the ESD generator where the circuitry models the human body capacitance and resistance and also the geometry of the metal generator tip as the physical source of the ESD.
Using this hardware, several tests can be carried out, such as direct and non-contact, various distances for the non-contact test, different voltages applied, and different environmental conditions such as humidity and speed of approach. All of the permutations of these tests can be very time-consuming and expensive to undertake, particularly considering the number of product variants and geo models a typical device manufacturer produces, as well as the large number of prototypes that might be created. Fortunately, physics-based computer simulation can be used as a pre-compliance measure to supplement testing very effectively, particularly during the early stages of a design. Passing a simulated test can give a very high degree of confidence that a physical test will pass as well. Simulation can also give a view of failure mechanisms and current flow and provide solution insights.
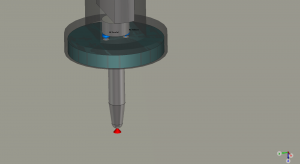
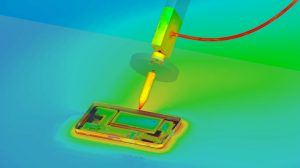
SIMULIA CST Studio Suite is a world-leading tool for modeling transient phenomena such as ESD. Using a transient solver to generate and propagate the voltage spike and using specialized meshing and material models to create the geometry and ensure speed and accuracy, allows the designer to gain rapid feedback on how a design will hold up. Both contact and non-contact model have been developed and both are fully compliant with the IEC standards and both have passed the calibration test used for physical generators.
Seamless integration into existing CAD workflows such as SOLIDWORKS and availability on Dassault Systèmes 3DEXPERIENCE Platform, give full traceability and end-to-end lifecycle management.
The models are available free of charge to SIMULIA customers.
SIMULIA offers an advanced simulation product portfolio, including Abaqus, Isight, fe-safe, Tosca, Simpoe-Mold, SIMPACK, CST Studio Suite, XFlow, PowerFLOW, and more. The SIMULIA Community is the place to find the latest resources for SIMULIA software and to collaborate with other users. The key that unlocks the door of innovative thinking and knowledge building, the SIMULIA Community provides you with the tools you need to expand your knowledge, whenever and wherever.