This is the second blog post in a new series where we talk to SIMULIA employees about current projects they are working on and developments they see in the simulation world. Recently, we talked to Matthias Tröscher, a Senior Business Development Executive at SIMULIA, about how electromagnetic simulation is helping transform the auto industry from mechanics to high-tech electronic systems. Check out our first SIMULIA Talks interview, here.
Who are you and what is your role in the company?
My name is Matthias Tröscher and I am a Business Development Executive focusing on electromagnetic applications in the Automotive Industry.
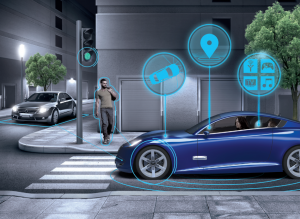
What developments are you most excited about in your industry?
The automotive industry is undergoing a huge change, away from the traditional approach that focuses on the mechanics, and towards high-tech electronic systems with electric drivetrain, autonomous driving and advanced driver assistance systems (ADAS), with a large number of sensors and electronic control units. In 2010, the electronic content in cars accounted for 30 percent of an automobile’s total production cost. By 2030, that amount will reach about 50 percent, as projected by various economic advisors. The entire automotive industry is in flux, and it is thrilling being a part of it.
How is electromagnetic (EM) simulation playing a role in those developments?
For more than 20 years, electromagentic (EM) simulation has been widely used in the automotive industry, e.g. for antenna development (performed by the supplying industry) and investigations on installed antenna performance (usually performed by the automotive Original Equipment Manufactuers (OEMs)). With the increase of electronic systems in automobiles, EM simulation helps to better understand electromagnetic emission effects and to mitigate electromagnetic compatibility (EMC) issues. Simulation tools are able to generate results that would be very time consuming to produce with measurement techniques or that would simply not be possible. Examples include the display of current (return) paths in electronic control units (ECU) and enclosures, visualization of electromagnetic emission effects, and detailed analyses of EM interferences (EMI) between antennas, consumer electronics, ECUs, and other devices. In order to perform such a detailed EMI analysis, a large amount of measurements would have to be made in order to obtain all the coupling paths between the individual electronic devices. With EM software, all the relevant information can be achieved in one simulation run.
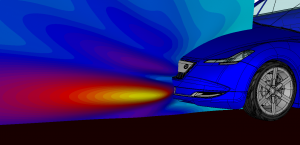
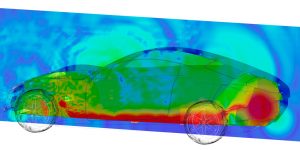
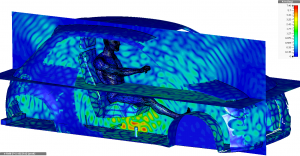
Which areas of the automotive industry are new to using EM simulation in their workflow and what are they working on?
Vehicle electrification is relatively new to the OEMs, so there is no well-established EM simulation process yet. In fact, the automotive industry is adapting the methodology from the aerospace industry, where model-based system engineering (MBSE) has been widely used for some time. Lots of individual workflows will still need to be developed to address all aspects of the production process, such as electric machine design, battery systems improvements, power electronics simulations, or human exposure analysis due to (high-voltage) electromagetic emissions. Another focus is multiphysics analyses, as they are gaining more importance in order to better understand how to mitigate noise and vibration effects of the electric drivetrain. The facilitation of multiscale and multiphysics design is key for the industry, and the leading-edge technology from Dassault Systèmes provides important tools to achieve this.
Where do you think EM simulation can provide a benefit where it hasn’t been adopted widely yet?
In the past, electromagnetic simulation was mainly used by Tier-1 and Tier-2 suppliers to develop and optimize single electronic components in standard test setups. However, the full potential of electromagnetic simulation can be tapped if it is used for the analysis of complete electronic systems consisting of e-motors, antennas, cables and ECUs in the real environment inside the vehicle.
Even though some of the companies have already realized that EM simulation is helpful at an early stage of development (during the concept and design phase), many others just use simulation when prototypes fail to pass emissions regulations or when measurements techniques reach their limits. This is a waste of resources, time and money because simulations can be run on virtual prototypes, helping to optimize them before hardware production. There is still huge potential for OEMs and suppliers to save costs and reduce the time to market.
Want to learn more about Dassault Systèmes’ simulation solutions for electric vehicles? Visit: go.3ds.com/TrustTheDrive