The design of vehicles is a challenging, time-consuming, and expensive process. Increased customer expectations compel automotive OEMs to design better-performing vehicles while reducing the cost and time for vehicle development.
In this article, we focus on virtual twin technology and how it can help in successfully addressing the vehicle design challenges, in particular the thermal aspects of design. A virtual twin is a virtual representation of a physical object and process that enables engineers and analysts to evaluate prototype design by simulation. This leads to a significant reduction in cost and time compared to development processes relying on physical testing.
For vehicle thermal design, we are referring to a process of setting thermal specifications for vehicles such as temperature limits for components, and ensuring that these thermal targets are achieved.
For automotive OEMs, not meeting thermal design targets has an immediate consequence of component failures and increased warranty costs. In 2020 in the US, there were 900 separate incidents of vehicle safety-related recalls, affecting 55 million vehicles, [1] and ‘thermal’ was the most commonly cited reason for the safety issues. However, a more serious issue is that vehicle thermal incidents impact passenger safety.
Virtual Twin Technology to Speed Up the Vehicle Design Process
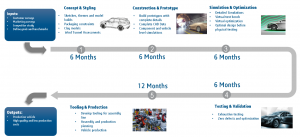
Vehicle development is a very time-consuming process. The total time from concept to production is typically three years. However, the time depends on the vehicle model and can range from three to six years. The design process is expensive, with costs up to four billion Euros.
Some of the factors that make vehicle design challenging, time-consuming and expensive such as the need to accommodate extreme driving conditions. For instance, vehicle design must succeed in start/stop city traffic, hill climbing, and driving under very cold and very hot weather conditions. Other design challenges include having a large number of parts (< 30,000), model proliferation, competing design objectives, and increasing regulatory pressures. Thermal design poses additional challenges that require vehicle testing at remote locations, in various weather conditions, and on test tracks. These complex test schedules add to the cost and time of vehicle thermal design.
Virtual twin technology, offered by Dassault Systèmes, can help to reduce costs and turnaround time for processes involving physical testing, as well as tackle issues during the vehicle design process.
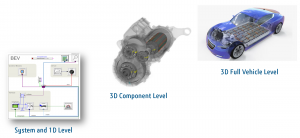
In figure 2, we see different levels of the virtual vehicle model, each representing operational aspects of the vehicle at a certain stage of its development. A system and 1D model applies to the early design stage in which design and basic vehicle layouts and functional specs are evaluated. At a later stage, we build virtual models that represent vehicle components at a 3D level with an exact geometrical representation. These virtual models are used in the construction and prototyping phase.
By applying these virtual twin models, a 3-year vehicle development process can be reduced to less than 20 months.
Vehicle Design Workflow Examples
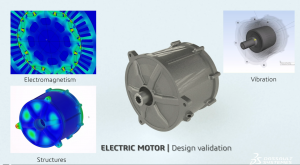
The workflows shown in figure 3, are all associated with an Electric Motor. The 3DEXPERIENCE platform® facilitates the design evaluation and analysis process associated with the e-drive by seamlessly integrating different workflows that evaluate different design specifications, for example, the evaluation of performance for electromagnetics, structures, and vibration design. In addition to the Electric Motor workflows, the implementation of a parametric CATIA model for the geometry allows the user to analyze a range of design options resulting in an optimal design.
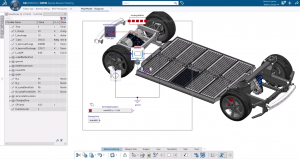
In figure 4, we see the implementation of Battery Pack workflows using the 3DEXPERIENCE platform. In this example, we simulate the battery range scenario as well as a battery-charging scenario. The platform enables users to switch between the two scenarios as well as between the 1D and 3D models.
High Fidelity Models for Accurate Test Procedures
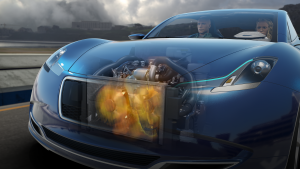
High fidelity models are used for the simulation and optimization stage of vehicle design. These models have all the geometrical details necessary for a virtual evaluation of the design and its changes to ensure that all the design objectives are achieved. In SIMULIA we have validated and automated simulation workflows that run high fidelity models to provide an accurate and timely implementation of test procedures and processes.
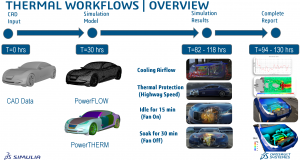
Figure 6, shows validated Thermal workflows that simulate standard testing procedures automotive OEMs use for product development. With automated tools, the total time from CAD to complete a report requires less than six days for all workflows and thus provides significant savings to the vehicle design process in both turnaround time and cost.
Cooling Airflow simulations enable the design engineer to optimize the cooling system layout and evaluate trade-offs with vehicle drag and interior noise. The Thermal Protection workflow identifies components that exceed design temperatures, fixes thermal issues, and optimizes shielding. The Idle and Soak workflow simulates the vehicle testing under transient conditions such as key-off/soak and accurately identifies temperature spikes.
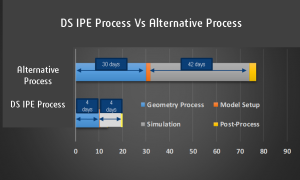
In figure 7, we compare the turnaround times for the Dassault Systèmes process and an alternative competitor process. We observe that the turnaround time for both the geometry and simulation process is significantly faster with the Dassault Systèmes process. The key enabler is using the exact vehicle geometry with no simplifications since the PowerFLOW solver has the robustness to handle complex geometries. For an alternative process, an approximate geometry is necessary, otherwise, the simulation runs the risk of solution divergence. For the simulation turnaround time, PowerFLOW runs significantly faster for transient simulations than the alternative process.
We found that thermal workflows offered by Dassault Systèmes provide faster turnaround and lower cost by requiring less prototype build for the vehicle design process. However, a necessary requirement for a simulation-based process is the simulation tool’s accuracy. In the following, we show some validation results for PowerFLOW.
PowerFLOW Delivers Accuracy in Validation Results
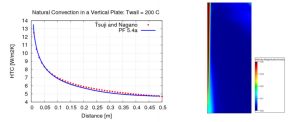
In figure 8, on the left, we compare the heat transfer coefficient on a vertical plane as a function of vertical distance with experimental data from [2] and observe good agreement between simulation and experiments. On the right, we observe the natural convection-driven velocity field for the vertical plate.
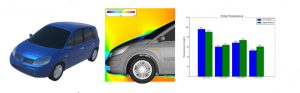
In figure 9, we compare thermocouple measurements for the Renault Scenic 2 vehicle with simulation results documented in [3]. We observe a good correlation as shown in the bar chart on the right. On the left, we show the image of the test vehicle, and in the middle, the velocity field in the y plane.
Dassault Systèmes offers virtual twin technology that enables a complete digital evaluation of vehicles from concept to production. With proven accuracy, SIMULIA simulation tools and workflows enable a reduction in costs and turnaround time of the vehicle development process.
References
- https://www.automotive-fleet.com/10156924/2020-saw-900-safety-recalls-nhtsa-urges-action
- Tsuji, T., and Y. Nagano. “Characteristics of a turbulent natural convection boundary layer along with a vertical flat plate.” International journal of heat and mass transfer 31, no. 8 1723-1734, 1988.
- Mukutmoni, D., Alajbegovic, A. and Han, J., Numerical simulation of transient thermal convection of a full vehicle (No. 2011-01-0645). SAE Technical Paper, 2011.
SIMULIA offers an advanced simulation product portfolio, including Abaqus, Isight, fe-safe, Tosca, Simpoe-Mold, SIMPACK, CST Studio Suite, XFlow, PowerFLOW, and more. The SIMULIA Community is the place to find the latest resources for SIMULIA software and to collaborate with other users. The key that unlocks the door of innovative thinking and knowledge building, the SIMULIA Community provides you with the tools you need to expand your knowledge, whenever and wherever.